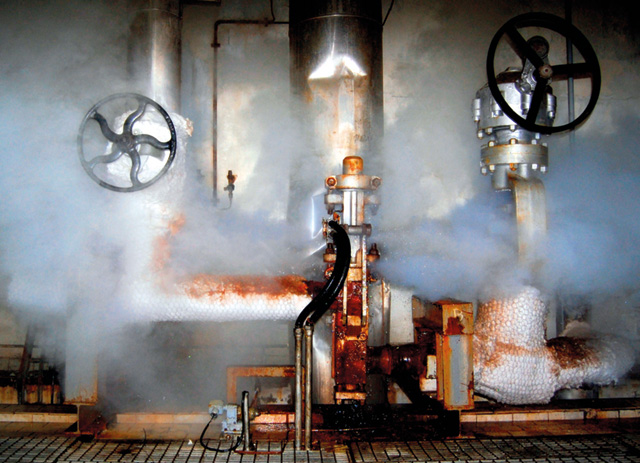
Reusing heat from condensate and steam means plants can reduce unwanted steam clouds, save energy and lower their operating costs, says Michael Povey of TLV Euro Engineering UK.
Clouds of steam vapour are a common sight in some process plants and are often considered to be an inevitable by-product of steam heating processes.
However, steam clouds can be considered an eyesore and create a safety issue from subsequent algae growth or freezing of falling water.
Vapour clouds can also make a plant hot and unpleasant if vented internally. Additionally, due to unprecedented fuel prices, this issue constitutes valuable heat energy going to waste.
When used in heating processes, steam loses its latent heat energy and condenses. The resultant condensate is usually over 100°C and may contain as much as 30% of the heat energy originally held by steam. When flash steam from condensate is vented to atmosphere, this valuable heat energy – much of which can be recoverable – goes to waste.
Some heating processes that use direct steam injection – such as steamers, autoclaves, sterilisers, and rubber vulcanisers – need to release steam from their systems. These vents may provide an opportunity for energy use rather than venting to atmosphere.
By collecting and reusing viable heat from condensate and steam, plants can reduce unwanted steam clouds, save energy and lower operating costs, all at the same time.
Here are some common examples of steam clouds within plants:
Steam vented to atmosphere from a condensate collection tank
Steam billowing from a condensate collection tank is a sign that although condensate is being properly collected in the tank, excess heat is escaping from the condensate and venting to waste.
Plants with this problem can implement one of the following counter measures to make better use of the excess heat energy:
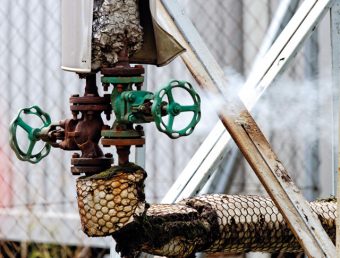
1. High pressure condensate recovery
The condensate can be returned directly to the boiler using a specialised, high pressure condensate pump rather than sent to the feed tank.
2. Flash vessel
The condensate can be allowed to flash, then used for preheating other applications or sent to the hotwell.
3. Steam compressor
The condensate can be allowed to flash, then used for preheating other applications or sent to the hotwell. The low pressure flash steam can be pressurised and reused in various processes.
4. Steam condensing heat exchanger
The flash steam can be used in a heat exchanger to heat water.
Steam clouds emitted from the boiler blowdown
It is common to see boiler blowdown vessels excessively venting and – depending on the installation – it can be excessive due to several reasons, including improper water treatment or incorrectly set maximum TDS. If the blowdown cannot be reduced, then recovery via heat exchanger and flash vessels is possible.
Steam clouds billowing from a flash vessel vent pipe
In some steam systems where condensate is recovered, clouds of steam can occasionally be seen billowing from vent pipes acting as flash vessels.
Vent pipes lower the pressure on the outlet end of steam traps, enabling condensate to be pumped and traps from other low pressure equipment to drain into those return lines. Flash steam billowing out of these vents can be collected and reused.
This flash steam can be pressurised and used in various processes via a steam compressor or sent to a steam condensing heat exchanger and used to heat feed water.
Steam clouds caused by a lifted safety valve
Are your safety valves lifting? Due to difficult visibility, common safety valve vent headers or lack of training, safety valves installed to protect steam using equipment from high pressure can often be left venting valuable steam. This waste steam can be prevented by identifying and repairing or replacing locations with safety valves installed.
Steam clouds emitted from condensate drained into a pit
This can be caused if the boiler is too far away, there is not enough condensate to justify return, or the condensate’s pressure level is too low. Whatever the reason, many plants choose to waste condensate into drain pits rather than recollect it.
In many cases, plants can achieve energy savings by routing condensate from processes into a collecting tank to return to the boiler using a pump (condensate recovery) or allowing it to flash and then using the resultant steam in a local heat exchanger (steam condensing heat exchanger).
www.tlv.co.uk | sales@tlv.co.uk | t: 01242 227223