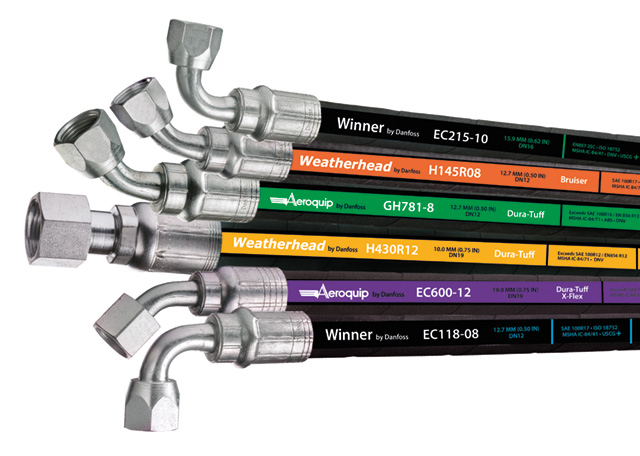
By Christopher Schwab, Global Product Management Leader, Rubber Hydraulic Hose and Fittings, and Aaron Clark, Global Material Science Leader, Danfoss Power Solutions.
Hydraulic hoses are the arteries and veins of a wide range of industrial equipment. They are responsible for safe, consistent operation. An unreliable hose could result in significant losses due to equipment downtime; it could also seriously injure a machine operator. Given the variety of applications in which they operate, not every hose is made the same, and careful attention should be paid to proper selection.
Hydraulic hose is far from a commodity. Its functionality and performance depend on the rubber from which it was manufactured, the quality standards with which that rubber was formulated, and the rubber formulation’s accounting for the specific performance demands in its intended end-use application. While not the only factor, rubber formulation is one of the most important contributors to reliable hose performance.
The characteristics of high performance
The general performance characteristics of a hose typically fall into several categories: temperature, flexibility, weathering resistance, abrasion resistance, and durability.
• Temperature – Rubber hydraulic hoses face a range of different temperatures in their everyday operating environments. In many hydraulic systems, increased demand for more power, speed, and flow have driven up system temperatures. Higher flow rates increase friction, leading to higher fluid temperatures. Today’s hoses must withstand these hotter temperatures, and performance is highly influenced by the rubber compound.
• Flexibility – Flexibility is a measure of the force required to bend a hose and is important for a few reasons. Hydraulic hoses must be flexible enough to be installed in a customer’s application, with the ability to bend and fit into compact spaces. In addition, hoses that move during equipment operation must have the right flexibility while maintaining durability.
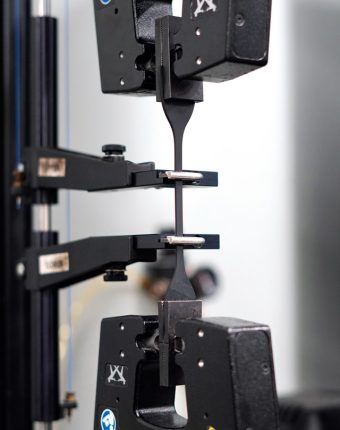
• Weathering resistance – Hydraulic hoses are often used in applications where they are exposed to direct sunlight or ozone during operation. Continuous exposure to these conditions can degrade rubber compounds, potentially leading to cracks in hoses that have not been formulated with weathering protection in mind.
• Abrasion resistance – Once in service, some applications regularly subject hoses to contact with other equipment parts or environmental hazards. Continuous rubbing or scraping against other surfaces can erode the hose cover, which can lead to corrosion or fatigue of reinforcement layers and eventual hose failure. Because abrasion is the most common failure mode for hoses, high tear strength is critical.
• Durability – Long service life is highly important for hydraulic hoses, especially in applications where downtime due to a broken hose can result in significant monetary losses. Longevity is often influenced by a hose’s ability to withstand high pressures, with dynamic pressure being the most challenging. In applications where pressure is rising and falling continuously, fatigue can cause a hose to fail. Durable compounds specifically designed to resist fatigue in impulse applications are required.
Formulation is key
Each of these hose performance characteristics is highly influenced by rubber recipes and hose construction. Formulating for a particular set of desired performance attributes can be a challenge. For example:
• A certain chemistry that can deliver higher flexibility may detract from abrasion resistance;
• Specifications that require a certain level of rubber hardness may not necessarily account for high tear strength;
• A certain polymer blend that grants a hose high temperature resistance may not be compatible with certain types of system media or hydraulic fluids.
Finding the proper chemical and polymer balance for a critical hose application requires a high level of formulation expertise, experience, and the right development process to achieve.
Raw material sourcing and supply are also of critical importance to hose quality. Even when the formulation is correct, a hose is only as good as the materials from which it is made. Manufacturing processes should be tightly controlled, and traceability is important. In the event of failure, the ability to pinpoint a flaw in production can help prevent similar occurrences in the future.
Making the right selection
When selecting or replacing hoses, keep in mind that not all hoses are created equal. Ensuring the hose meets pressure, temperature, bend radius, and other system specifications is critical. Selecting hose optimized to provide safe, reliable, and long-lasting performance from a reputable manufacturer can have a direct impact on the bottom line.