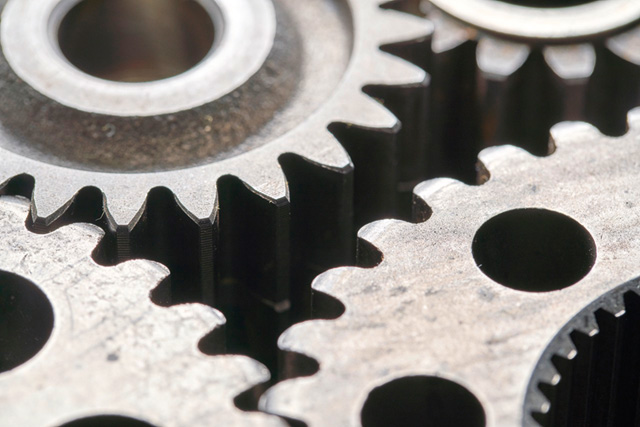
Marcus Schneck, CEO of norelem, says engineers and plant managers must ensure that their drive technology is fit for purpose as manufacturing continues to evolve towards smarter, greener, and more efficient production.
Drive technologies provide process control and efficiency for systems such as fans, compressors, pumps, and conveyors found in industrial contexts all over the world by controlling torque and speed. The demand for efficient, effective drive technology is growing as automation becomes more prominent.
Operators stand to benefit from lower operational expenses and lower energy usage by optimising power transmission processes. With multiple systems and options available to the market, it’s essential to specify the right type of equipment for increased accuracy and higher productivity.
Picking the right drive system
When considering the right drive system for an application, engineers must consider the key advantages that each technology provides:
• Chain Drives – A chain drive is comprised of sprockets, sprocket disks and a roller chain, with some applications supplemented with tensioners and deflectors. This is the toughest and most durable system, and norelem’s chain drives are manufactured to the DIN / ISO 606 standard.The teeth are milled and hardened, exactly aligning the groove with the tooth tip. This choice will greatly benefit engineers looking to implement a drive system featuring considerable power transmission over a short distance with low maintenance requirements. The alternative addition of stainless-steel chain wheels also makes this a common choice within the food industry.
• Toothed Belt Drives – Featuring a toothed belt alongside two or more belt pulleys, there are multiple advantages to a toothed belt system. Toothed belts can run large forces with high acceleration while also ensuring exact positioning and guarantees constant speed. When the system is correctly installed and tailored with the necessary components for its given purpose, toothed belts can be energy efficient, quiet and precise – allowing for high acceleration values if required. Due to this, the system lends itself well in mechanical engineering industries such as automotive and aerospace.
• Gears, Racks and Bevel Gears – Gear drives are also common in mechanical engineering applications, allowing for customisable torques to be transmitted from one shaft to another all within a compact and simple design. Engineers can simply adjust torque or speed by exchanging individual gears, allowing for greater flexibility when required. Similar to chain drives, gears are also low maintenance and can deliver high forces across short distances all within a slip-free, form-fitting design.
• Worm Gears / Worm Gear Sets – The aptly named ‘worm’ refers to a shaft with one or more screw threads which is then connected to a worm wheel (helical toothed), forming the worm gear. The axis of the system is offset by 90°, allowing for large ratios to be translated into slow speeds. With norelem’s worm gear sets capable of continuous operation at high speeds and torques, the system is naturally resilient due to its construction. However, it’s worth noting that because the drive is powered by both a rolling and sliding movement, the gear is not as efficient as the other drive options also available.
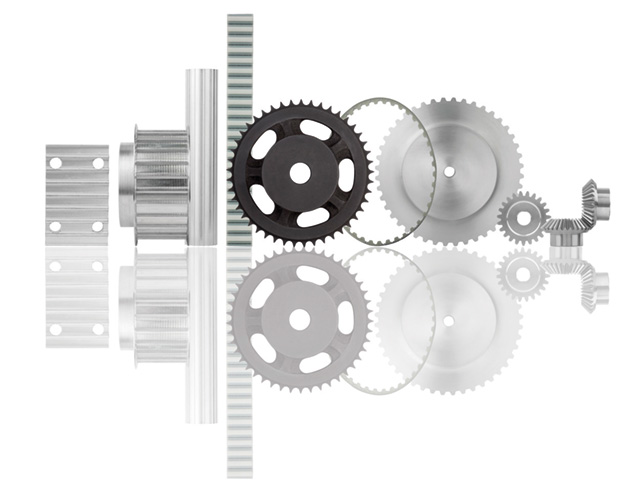
The benefits of installing the correct drive technology system
There are multiple benefits to drive technology that is fit for purpose – with each system offering unique capabilities tailored to specific applications.
For example, while the service life and low maintenance of chain and gear drives will better serve mechanical engineering industries, toothed belt drives will better suit applications demanding precision process control and high production rates. Equally, the choice of stainless-steel components will better serve applications where hygiene is a higher priority, such as the medical or food manufacturing industries.
By selecting the correct system, engineers can choose a drive that’s fit for purpose and aids production efficiency. By integrating the correct system into the process, manufacturers will benefit from optimal power transmission, decreased wear and maintenance, increased system longevity and constant gear ratios.
In the long term, a finely tuned drive system will not only provide optimal efficiency performance but also reduce the energy needed to power the system, helping to lower operational costs and reducing carbon footprint.
www.norelem.co.uk | info@norelem.co.uk | t: 0121 222 5320