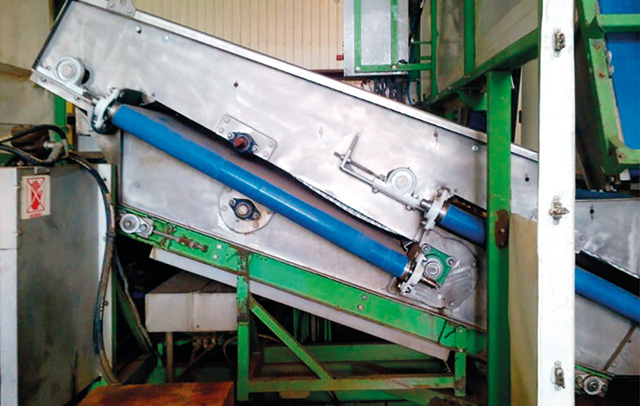
Continuous high speeds, demanding hygiene standards and challenging operating conditions demand robust, reliable bearings that deliver cost-effective production at food and beverage plants, says Simone Albarak of NSK.
Any bearings deployed in these applications must reliably prevent the onset of corrosion, which is a common threat on production lines subject to harsh wash-down regimes. Central to NSK’s product offer for the food and beverage industry is its RHP Silver-Lube® range of bearing units. These innovative bearings are comprised of a host of corrosion-resistant components, including inserts with high-grade stainless steel rings and balls, cage, flingers, and set screws. Furthermore, the inserts sit within a high-strength PBT thermoplastic housing featuring a stainless steel grease nipple.
Excellent protection against corrosion, chemicals and detergents ensures Silver-Lube® can endure challenging operating conditions at food plants around the world. An example of this involved the processing of baby leaf greens, the growing global demand for which is driving the requirement for reliable, highly productive harvesting machines.
Baby leaf greens include spinach, arugula, kale and lettuce harvested at just a few weeks old. Harvesting the crops at this stage is gaining popularity due to good leaf size, colour and texture, as well as thicker leaves that allow for longer shelf life. These products often contain a mix of baby leaf greens selected for their flavour, nutrition and aesthetic qualities. With demand so high, there is no margin for production downtime due to the failure of bearings on process-critical equipment.
Among those able to provide testimony to this fact is a facility in Europe that processes baby leaf products for leading supermarkets. Here, the leaf harvester previously featured numerous low-cost mounted-unit bearings of different sizes to support shafts of various diameters. Unfortunately, during the harvesting season, the machine was prone to ongoing failures due to the ingress of dirt and water into its bearings. The eventual conclusion was recurring production downtime whenever a failure occurred to allow for repair work. These situations could also lead to ruined crops in some instances.
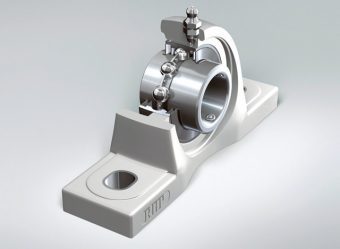
NSK experts accepted an invitation to review the application and operating conditions. This appraisal process ultimately led to the replacement of the existing mounted units with Silver-Lube® featuring an innovative flinger seal arrangement and stainless steel bearings. During the subsequent harvesting season, just two bearing failures occurred, improving productivity and generating savings of €63,300 thanks to significantly lower production losses. This figure represents a halving of the previous costs.
As this success story illustrates, Silver-Lube® bearing units are ideal for applications requiring frequent wash-downs, optimal hygiene standards and good chemical resistance over a broad temperature range.
As well as high protection against corrosion, Silver-Lube® offers durable and heat-resistant silicon rubber seals that protect against penetration by water or dirt, which is important to prevent the onset of defects and avoid washout of the bearing’s wide temperature USDA H1 food-grade grease. Notably, this type of grease consists of entirely food-based ingredients, including base oil, thickening agent and additives. Complementing the Silver- Lube® seal is the stainless steel flinger, which prevents the ingress of bacteria and helps the seal to resist impact damage.
Further Silver-Lube® advantages include a paint-free resin housing to eliminate any risk of chipping or flaking; a smooth finish to prevent dirt adhesion; a cavity-free design to avoid ‘bug traps’ that might harbour bacteria or mould; suitability for working temperatures from -20 to +90°C; long service life; and low cost of ownership. Silver-Lube® is also NSF-approved, meeting strict standards for public health protection.
Another noteworthy attribute is the ability of Silver-Lube® bearings units to accommodate any initial misalignment from mounting errors, making them ideal for use in food and beverage plant machinery such as shakers, fillers, centrifugal separators, bottling machines and conveyors.
NSK engineers can work with customers to analyse critical points in the production process, measure and monitor efficiency, and propose the optimal bearing solution.
www.mepax.com | albayrak-s@nsk.com | t: +49 2102 481 2152