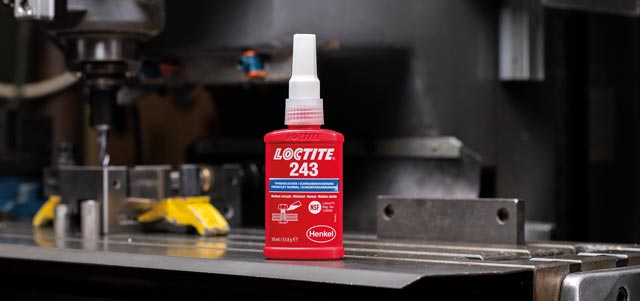
Loosening of screws and fasteners in electric motors can lead to damage. Bob Orme, senior technology specialist at Henkel Engineering Adhesives Division, outlines a solution.
Electric motors provide the heartbeat of many industrial applications, including any that involve mixing, lifting, pulling, pumping or grinding. Air conditioning units and fans also rely on electric motor technology. For uninterrupted productivity and long service life, electric motors must withstand vibration, torque, thermal cycling and corrosion. With this in mind, increasing numbers of maintenance engineers are turning to the latest thread locking adhesives in preference to conventional solutions such as lock washers.
There are a number of common difficulties relating to the use of threaded fasteners on an electric motor. For instance, the loosening of motor assembly screws and cover screws due to vibration and shock loads is a frequent occurrence, leading to potential damage of the housing and frame. Another hazard is the loosening of through-bolts that hold the housing end plates in position. In some situations it has been known for the through-bolts to shear off completely.
Further issues include the seizure of threaded fasteners, while the loosening of motor mounting bolts can lead to shaft misalignment and consequent damage to rotational components.
All these failures can usually be traced back to one factor – the gap between the male and female threads. It may be a surprise to learn that metal-to-metal contact in fastened joints is only around 15% – the remaining 85% is just gap. Because of this gap, any side-to-side motion caused by vibration can lead to loosening.
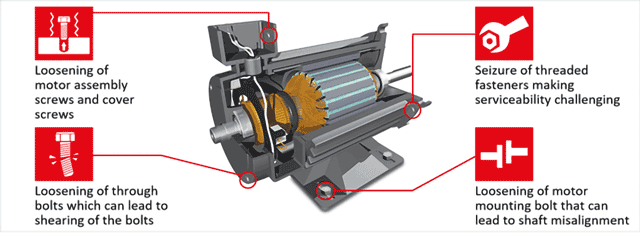
The liquid alternative
Lock washers, while providing some level of maintained torque for a period of time, do not close the gap and consequently prove ineffective. A liquid thread locker, on the other hand, overcomes the issue entirely.
Two Loctite thread locking products from Henkel are proving particularly popular for electric motors: Loctite 222 for small diameter and long-engagement bolts (such as motor through-bolts), and Loctite 243 for all other bolts.
By using these two thread lockers, the clamp loads of fasteners are maintained, to ensure the reliability of a motor over its full working life, while shaft alignment with driven equipment is assured. In addition, the threads are sealed to prevent seizure and to provide easy servicing when required – joints can be disassembled using nothing more than hand tools. The sealing function also protects against the ingress of liquids, to prevent corrosion.
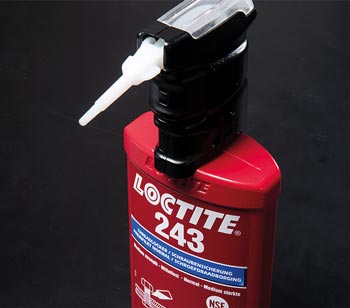
More applications
Aside from thread locking, there are many other electric motor applications that benefit from the introduction of adhesives. Take the use of retaining compounds on parts such as bearings, commutators and armatures, all of which must be held in position on the shaft.
In common with thread locking adhesives, retaining compounds form a 100% contact between mating metal surfaces, eliminating the need for expensive replacement parts, time-consuming machining or the use of mechanical methods such as pins, splines, clamp rings and shrink fits.
Electric motors typically pick up speed with a jerk. The repeated jerk can lead to the loosening of bearings and commutators, in turn reducing the transmitted torque and leading to potential component damage. Loosening can be prevented by the application of a retaining compound.
Loctite retaining compounds are proven for applications that include securing the inner bearing diameter to the shaft, as well as the outer diameter of bearings to the end cap housing. Using these products will help increase the torque load transfer of existing designs and provide an even distribution of loads and stresses. Commutators and armatures can also be retained in position.
Ultimately, electric motors need to meet demanding requirements for increased durability and motor efficiency. By relying on the latest adhesive technologies, the performance and service life of electric motors can be assured.