Automating schedules and work allocation, as well as integrating with other IT systems, can pay dividends, says Gary Watkins, chief executive of Service Works Global.
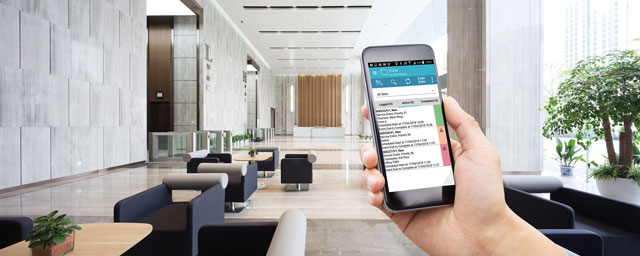
Following a difficult year dealing with furloughs, closures, and frequent business strategy changes, facilities management teams are faced with having to do more, in shorter timescales, with less resources. Computer-aided facilities management systems are widely used for asset and maintenance management, but they often have the capacity to do much more to ease the workload of the facilities manager, and in turn improve return on investment.
Automation
The pressure on a facilities management help desk in managing hundreds of work requests, and especially dealing with Covid-19 related absences and shift pattern changes, can be intense. Bottlenecks and incorrectly allocated work lead to an inefficient team, but these processes can be easily automated through a CAFM system without involving the IT department. This can range from using the software to automatically apply a priority level to a reactive job based on predefined criteria, to batch allocation of jobs – with each task being emailed or sent to the mobile phone app of the operative with the correct skills.
Integration
Automation can be taken one step further. Integrating CAFM with building management systems or an IoT network can remove the need for human interaction completely. If a sensor on an asset predicts or identifies a breakage, a job can be raised automatically on the CAFM and automatically dispatched to an engineer. Once the issue is fixed, the job can be marked as completed on the app, which in turn alerts the BMS to turn the asset back on (if applicable).
Finance and health and safety systems are also commonly integrated, allowing the CAFM to share the same data securely – saving time and reducing errors created by adding data manually. Service Works Global’s FM Tech Survey 2020 found that of respondents who reported their CAFM system was helping their organisation save money, 75% were using an integrated system.
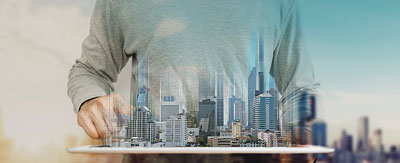
Assisted planning
Finding time for planned preventive maintenance and reactive schedules is difficult in general, let alone during the disruption caused by coronavirus. CAFM can create these schedules, making short work of administration and thus minimising asset downtime. A PPM check could be set to occur every four months, avoiding weekends, and assigned to a mechanical engineer with availability in their schedule. Reactive works can be scheduled around the PPM calendar, even combining visits where appropriate, to reduce travel and speed up rectification times. Should the engineer not complete a PPM task, it is automatically reallocated to ensure assets are not run until they fail.
Centralised data
Social distancing and the need to maintain consistently high standards across all facilities management services – especially cleaning – has meant even small teams are experiencing communication challenges. Where spreadsheets and paper job sheets might have been sufficient before, moving data to a centralised environment has become a necessity.
A CAFM’s integrated helpdesk can be accessed from any internet browser to keep track of all jobs including deadlines, the workload for each team member, and outstanding tasks, meaning the likelihood of duplicated work or missed tasks is greatly reduced. External contractors can also be given access to the CAFM system, with reduced access rights, so that all work across the site is accounted for.
Building information modelling
19% of FM professionals are currently using building information modelling, according to the FM Tech Survey 2020, and interest is growing most rapidly in the areas of digitising existing buildings (rather than in using BIM to plan and construct new builds). Virtual 3D models can be created from existing blueprints or with laser scanning and photography to provide the facilities management team with a scaled, digital replica of the building.
Once integrated with a CAFM system, this becomes a goldmine of information for the FM team, and can dramatically improve site efficiency. When allocated a task, an operative can use the BIM model to identify any access issues, such as confined spaces or permit requirements, as well as seeing an asset’s maintenance history, manuals, warranty dates, part serial numbers and more, thus reducing the necessity of a return visit.
Further information: contact Service Works Global on info@swg.com
www.swg.com