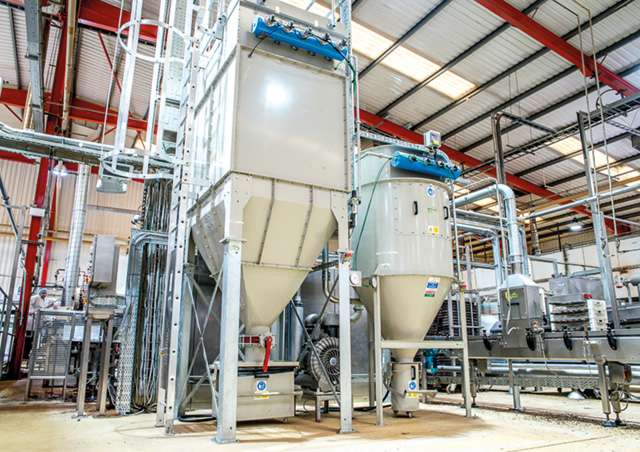
Careful consideration is needed before selecting a filtration system for your industrial application, says Dustcheck product manager Andy Darby.
Of the many types of solid particulate filtration systems available, there are two main categories: ‘dry’ and ‘wet’ filter units.
Fundamentals of dry filter separation
These units typically feature permeable filter media to separate solid particulates from a gas stream. Dry filter units used in industrial applications usually have a method of automatic cleaning to dislodge filtered particulate, although some units are designed as simple barriers.
Depending on the type of application, filter elements will need to be periodically cleaned or changed. Dry filter systems are suited to many different applications, reliable and low maintenance.
Limitations of use
Dry filter units using membrane type medias usually contain filters: either pleated cartridges or cassettes, tubular bags or flat bags.
They essentially use a permeable media which requires filtration to occur on the surface, or sometimes through the material. As such these types of filters are challenged if there are high moisture levels in the extracted air which can saturate the filter media, or the particulates are very adhesive and difficult to remove with an automatic cleaning system.
For particulates in liquid form, there are other extraction solutions available.
High moisture levels that exist in a gaseous state are not necessarily a problem so long as any temperature differences between the extracted air and filter unit are considered so the air is not cooled to ‘dew point’ which is when condensation will occur.
Other considerations for dry filters are around potential ignition sources, for example metal grinding producing sparks, and limitations of protection when handling highly explosive and volatile dusts.
Most dry filter medias are flammable. Introducing ignition sources can pose a fire risk unless some means of protection is implemented such as spark extinguishing.
If dust being extracted is explosive, risks are even greater. Even with adequate explosion protection this type of application may pose a high enough risk to move away from a dry filter solution.
Another limiting factor with dry dust filters is the maximum level of explosion protection available. The vast majority of particulates handled in industry are well within the capabilities of a dry filter system. However care should be taken when handling dusts with high explosibility levels. In this instance it is unlikely a dry filter unit will be suitable.
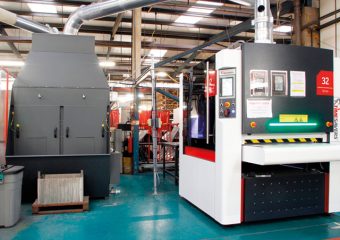
Fundamentals of wet filter separation
A wet filter unit typically separates solid particulate from a gas stream by passing it through an atomized liquid. Particles become encapsulated by droplets and are submerged into a tank where sedimentation occurs. There is no requirement for replaceable filter elements as with a dry unit.
Wet dust collectors are mass separators. Efficiency of collection is determined by the mass of the dust particle present in the extracted dust cloud relative to the size of the water droplets generated.
Wet collectors are more suited to particles with heavier mass. They function by generating very fine droplets or aerosols in the ‘spray generation zone’. These droplets will impinge on, and encapsulate dust particles of similar momentum.
Wet collectors are recommended when machining reactive white metals such as aluminium, titanium and magnesium due to their highly volatile nature. They are also ideal for handling sticky particulates or dusts extracted with liquid moisture.
Limitations of use
Wet units create a liquid waste stream which is also the medium in which particulate accumulates. This requires regular manual cleaning.
Treatment must also be added to the water to minimise corrosion, and this requires regular checks to maintain correct levels.
A proportion of water is consumed and given off as vapour. This is a visible discharge plume, so a permanent water supply is required to allow operating levels to be maintained. Consideration must be given to the unit discharge position because of the vapour plume.
Filtration efficiency based solely on particle size is limited when compared to dry units. Typically, the mean particle sizes in a wet unit need to be >25 microns to achieve the same levels of efficiency as dry units handling dusts at five microns. Careful consideration of required filtration efficiency and particle size distribution should be applied before selecting a wet unit.
The main applications for wet filtration are based around mechanically generated dusts such as polishing, linishing, grinding and crushing.
In conclusion
Industrial filtration is extremely varied with many factors influencing product selection. We recommend advice is obtained in terms of application before selecting a product.
www.dustcheck.com | louise.smallwood@filtermist.com | t: 07870 646788