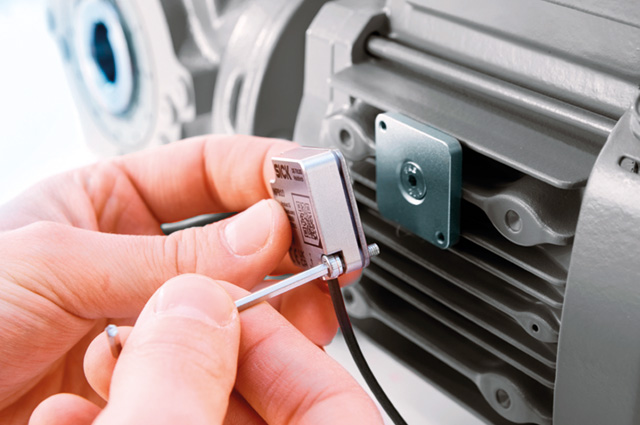
Smart sensors are combining with digital services to open windows for operators to both ‘see’ and ‘understand’ what is going on inside their machines to improve service and maintenance, explains David Hannaby, SICK UK market product manager for presence detection.
Approaching predictive maintenance from a sensor’s eye view means you begin from the ground up. We can ‘plug in’ eyes and ears wherever they are needed to unlock previously-hidden data. We can then represent that data to enable operating personnel at all levels to get health checks in real time and to see data in new ways to learn fresh insights. The technology doesn’t have to be complex, time-consuming, intrusive or insecure. It can be incremental, low-risk and transformative.
Most people are now familiar with the ability of Smart Sensors to output diagnostic data and provide additional information, either about their own status, e.g. “Does my screen need cleaning?” Or their process performance: “How many times have I detected something?” Even this simple data can lead to more informed maintenance interventions.
However, because sensors are often positioned right in the heart of machinery, they can provide additional insights over and above their function. These do not have to be complex IT systems or big programming projects. New insights are achievable in very practical ways, using simple, ready-to-use and even bolt-on services.
Data from the heart of a machine
Newly-developed sensor technology is providing the opportunity, quite literally, to bolt on real-time, continuous condition monitoring to many different machines, including motors, pumps, conveyor systems or fans. The SICK Multi Physics Box, for example, measures vibration, shocks and temperature. It can be set up to alert when measured values exceed pre-configured thresholds. By considering previously disparate sets of data together, new insights are gained. As a result, changes in performance are detected early and maintenance work can be planned based on real data.
Getting visibility to the data from your machines is just the first step to taking proactive, rather than reactive, service and maintenance decisions. Digitilisation is providing new levels of transparency for operators to understand and interpret the data that sensors produce. In Maintenance 4.0, data from sensors is enabled through networked connectivity and software, either locally on site or in the cloud, to give people the power to visualise trends and identify patterns.
As part of SICK’s portfolio of digital services, SICK offers the Monitoring Box which is a software platform that facilitates the integration and visualisation of sensor data for SICK customers. It enables plug-and-play condition monitoring to assist with preventative and predictive maintenance of sensors, machines, processes and plants.
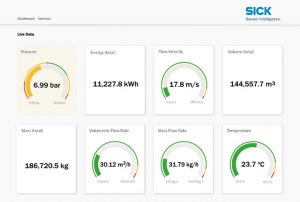
Switching Data to Visual
When enabled using pre-configured Apps running on smart sensors, the Monitoring Box provides transparent data monitoring through an intuitive, browser-based dashboard. It can be adapted for all sorts of operating requirements to provide live status feedback and historical analysis supporting more effective maintenance and optimised efficiency.
Depending on your requirements, information such as operating hours, wear, temperature, energy usage or level of contamination, is turned into a valuable resource.
Crucially, the software affords users the power to predict e.g. to help to calculate based on real measurement values when a particular component or device is going to reach the end of its operating life, so that it can be replaced before it leads to downtime.
Maintenance programmes to keep your devices and systems in good condition can be inferred based on diagnoses and statistics. This makes it possible to carry out inspections, repairs and maintenance in a quick and tailored way, and to plan servicing more reliably.
Transparency
This new transparency could be enabled on a smart watch of an operative patrolling a shop floor, just as much as it allows for easier monitoring by a management team in the company headquarters on the other side of the world.
We are already seeing how early adopters are gaining unexpected insights. For example, using SICK’s monitoring app for its FTMg multifunctional flow sensor, our customer was able to identify energy cost savings from compressed air usage. By visualising and tracking consumption over time, compressed air energy losses were easier to spot and correct.
Sensors and sensing systems are the building blocks of Maintenance 4.0, affording added flexibility to unlock data that saves routine service and reactive maintenance hours. Decisions can be based on real data in real time. Intervals between service visits can be optimised, machine availability maximised and stoppages avoided.
Better condition monitoring and predictive maintenance therefore benefits Overall Operating Efficiency and leads to greater commercial added-value.