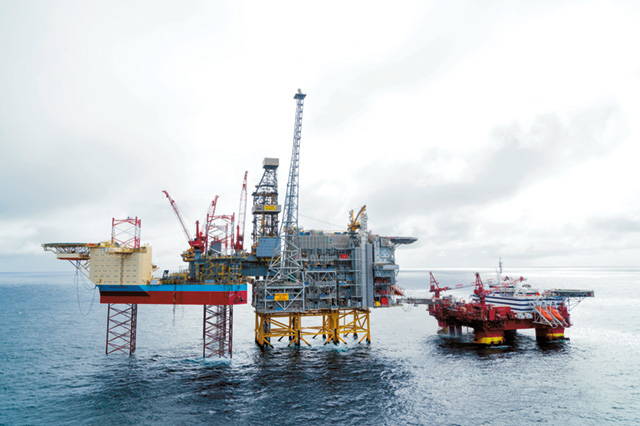
Advanced automation technology and remote support services are helping to improve the performance and safety of offshore oil and gas platforms says John Ellis, UK sales director for systems and software at Emerson.
Remotely operated offshore oil and gas platforms that help to minimise the number of people on board are providing the industry with significant cost and safety benefits.
Reducing accommodation requirements has major platform weight and cost implications, while transporting less personnel offshore minimises operating costs and improves safety by keeping workers far from potential hazards.
Digital automation solutions help to achieve safe and efficient operation, which is vital in terms of both control and maintenance. The latest advanced control and safety systems use cyber secure remote access services to enable control and monitoring of all equipment from the safety and comfort of an onshore control room.
Asset performance and health information are also accessible, with operators increasingly turning to equipment vendors to provide remote support services to help optimise the maintenance of offshore assets.
Maintenance activities
Costs related to equipment upkeep and repair is a core component of offshore operating expenditure. The industry has increasingly implemented strategies for asset performance management and proactive reliability management to counter declining operational performance while improving process availability and lowering operating costs.
To identify developing faults, there is now much greater use of online monitoring and predictive diagnostics on asset health to enable more efficient planning of maintenance activities.
Asset management software is increasingly used to manage maintenance tasks, providing plant wide visibility into the performance and health of intelligent field devices, and delivering troubleshooting information when an issue is detected. These software tools use open standards and communication protocols to enable connection to a wide range of machinery health monitoring systems, devices and sensors.
The software presents real time condition data for critical equipment, enabling maintenance teams to respond quickly and make better informed decisions to improve the maintenance, availability and performance of these key production assets.
Remote monitoring
For remotely operated assets with fewer onboard personnel, there is a greater reliance on remote monitoring solutions to support equipment inspections and maintenance. By installing advanced wired and wireless sensors throughout the platform and leveraging secure communications and analytics software, experts located onshore can have real time access to equipment health and performance data, enabling them to provide insights and reassurance.
Remote monitoring also minimises the number of maintenance trips required, thereby lowering costs and enhancing safety.
In depth knowledge is required to turn data from critical equipment such as turbines, pumps and compressors into actionable information. Critically, as a result of recent advancements in cyber secure solutions for remote connectivity, operators are now able to have the confidence to give outside experts access without exposing themselves to data breaches or disruptions.
Sensor data is analysed by specialists, increasingly provided as a service by the vendor or maintenance provider, who use the information to anticipate issues and perform adjustments to maximise key performance indicators.
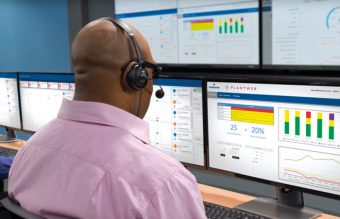
Lifecycle service
Remote support services from automation vendors are being expanded to include the maintenance and lifecycle management of valves, instrumentation, control systems and software. Sub optimal performance of automation systems can lead to serious process disruptions and costly unscheduled downtime. However, it is increasingly challenging for users to ensure that software and hardware are up to date to ensure system security and reliability.
To support them, system vendors provide a prognostic service that enables real time management of automation systems, to optimise their security, reliability and performance. The user is provided with aggregated data about platform architectures and applications, technical support, software updates, and proactive information on risk management, incident management and lifecycle management.
To reduce the time taken to manually download and install updates, an automated patch management service enables automatic downloads.
Offshore service agreements
Emerson provides a range of digital lifecycle services. The Norwegian energy company Equinor is adopting some of these to support operations on its pioneering Martin Linge platform in the North Sea. Emerson has signed a five year operational support service contract with Equinor to ensure continued safe and optimised oil and gas production.
The service agreement covers maintenance and upgrades of control technology, software and instrumentation. These technologies are helping to empower remote operation from onshore.
Emerson’s DeltaV distribution control system, advanced measurement instrumentation, critical control, emergency shutdown and isolation valves, metering technology and asset management software enable both the platform and the floating storage and offloading vessel to be mainly operated from an onshore control room in Stavanger, Norway.
Offshore operators can access the control system interface via mobile handheld devices, resulting in increased worker flexibility and efficiency. Controlling the production facilities in this manner enables three shifts of operators to work from onshore rather than offshore, reducing risk to personnel and minimising costs.
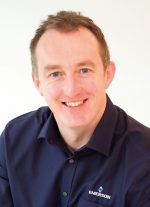
John Ellis
UK Sales Director for Systems and Software
Emerson