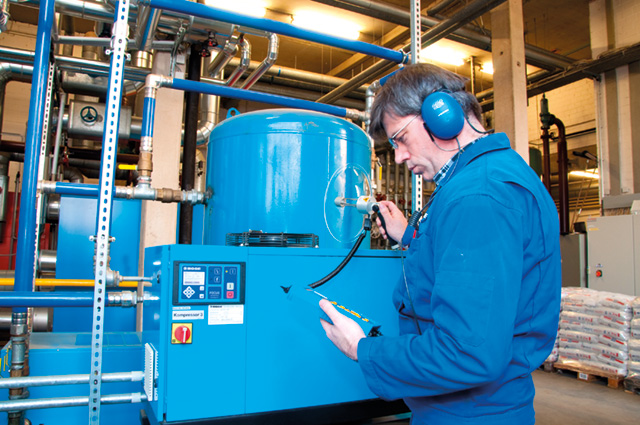
With the cost of energy soaring in the UK, it is vital that compressed air systems are as efficient as possible. Those that find their system wanting will need to decide whether to repair it, rent a replacement or purchase a new compressor outright, says BOGE’s General Manager, Mark Whitmore.
Compressed air is a vital industrial resource, but each year in the UK over 10 TWh of electricity – equivalent to the output of almost one-and-a-half power stations – is used to produce it. This is significant, given that UK manufacturers are warning that their energy costs are currently spiralling out of control, with nearly half reporting that their electricity bills have shot up by over 100% in the past 12 months and 53% expecting the same fate in the coming year.
Unsurprisingly, many manufacturers are evaluating their compressed air systems to maximise their energy efficiency. Those with older systems will have a tough decision to make; do they repair what they have, rent a system or invest in a completely new one? All three options have their merits.
Short term option
Repair is likely to be the cheapest short term option if certain parts of the compressor can be easily replaced. It can also yield significant returns. The leak rate on a poorly maintained compressed air system, for instance, can be as high as 40-50% of the generated output, and in certain applications even higher figures have been measured.
Indeed, one 3mm hole in a compressed air system could cost a business well over £1000 a year in wasted energy. A well maintained system should only lose around 5-10% of the compressed air it generates to leakage. Operating at these levels could reduce energy consumption by as much as 20%.
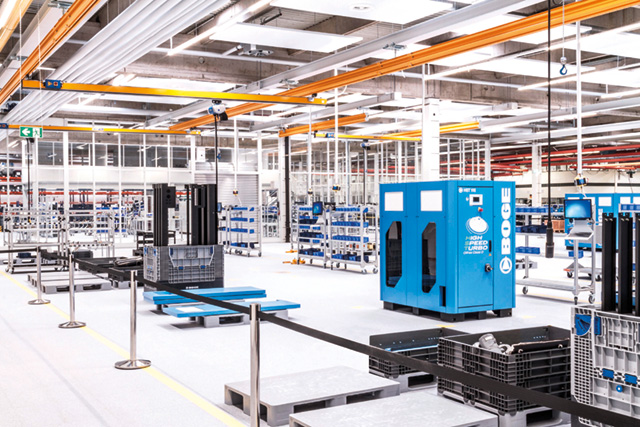
Lifetime costs
Before settling for a repair, however, it is worth looking at the lifetime costs of owning and operating an air compressor. Only around 15% of the total cost is represented by the initial investment, and 10% by commissioning and maintenance. The remaining balance, around 75% of the total cost of ownership, is taken up by the energy needed to run the system. Opting to repair an old and energy-hungry system could therefore be an exercise in false economy.
Stop-gap
Renting a compressor might be a good option if a manufacturer does not currently have the CAPEX available for a new system, or if the compressor is needed for short durations, such as to fill a seasonal peak demand, special projects or other temporary situations. Rental costs are typically predictable.
Further, rental partners will typically take responsibility for maintaining the system.
High efficiency
For an air compressor that will be used regularly, purchasing is generally the optimal choice. For companies with available CAPEX, there has rarely been a better time to buy an air compressor than now. In the UK, a super deduction tax break enables businesses to reduce their corporation tax liability by 130% of the value of any investment they make in compressed air systems.
In addition, energy efficiency is baked into the designs of most modern compressors. The latest systems can be fitted with heat recovery systems. A large amount of the energy taken in by a compressor is converted to heat and diverted away via a cooling medium. Using a recovery system, this heat is not lost and can be put to use in another way, such as for heating domestic or circuit water, or for process support. Indeed, such systems can recover up to 94% of the heat that the compressor generates, saving manufacturers potentially tens of thousands of pounds a year.
The use of intelligent control systems, meanwhile, can reduce energy consumption significantly. Remote monitoring systems can also be supplied with these compressors, meaning firms can avoid downtime with managed maintenance and servicing.
As we have seen, air compressors can be energy-intensive to operate. No matter your budget, there are steps that you can take to help rectify this issue, saving you money and boosting your bottom line.
uk.boge.com | uk@boge.com | t: 0800 318104