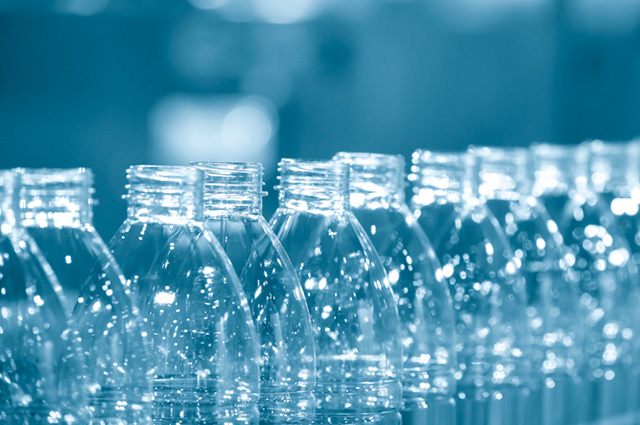
Replacement of linear guides on blow moulding machines used to produce plastic bottles has helped one plant operator to dramatically reduce production downtime, writes NSK Europe’s UK Sales Engineer Richard Robson.
Among many factors closely associated with serving the food and beverage industry is the need for high uptime. This metric is truly put to the test in an environment where production lines must meet high throughput demands and plants face running at elevated speeds, with little margin for failure in order to meet customer orders. Line stoppages are potentially disastrous in this highly competitive sector, where only the fittest and leanest survive.
With these thoughts in mind, all machine components are subject to scrutiny as engineers seek to build reliability into every production system. Sometimes, however, there is a need to revisit a machine design retrospectively, perhaps after a series of unexpected failures.
A recent case in point centres on a manufacturer of polyethylene terephthalate (PET) bottles, which frequently found itself replacing the linear guides on its blow moulding machines. Linear guides use bearings to guide the movement of heavy loads. Such an issue can deliver a significant hit to profitability as plastic bottles are commodity items with notoriously low margins. Any problems during production can lead to complete profit erosion.
As an associated issue, plastic blow moulding faces ever increasing challenges for the production of more sustainable plastic containers. Machine makers must therefore implement the most efficient motion control technologies. Any failure in this regard can leave plants with an unwanted and often costly headache.
Dissatisfied with the expensive inconvenience of the failed linear guides on its machines, the plant invited NSK to investigate. Analysis of the failed guides identified the cause to be end cap damage, which was occurring due to a combination of short stroke movements, short cycle times, frequent start/stop operation and increased friction force during start-up.
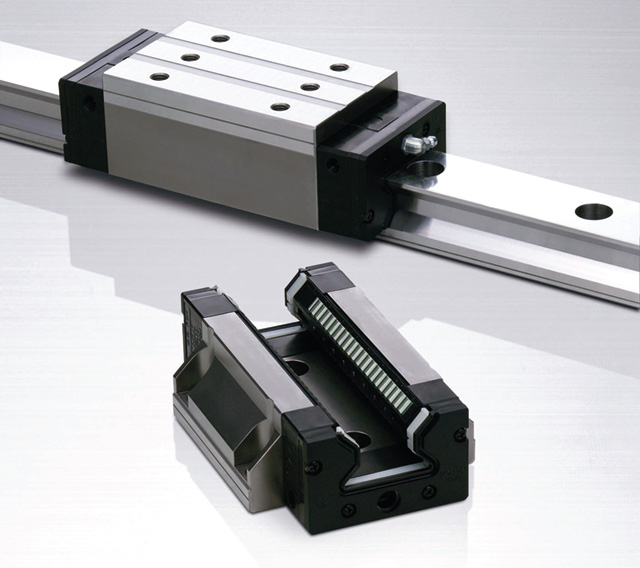
Given this application profile and the damage that was taking place, NSK recommended that the plastics processor install its robust and reliable RA series roller guides. These guides offer, among other things, high load-carrying capacity and motion accuracy, extreme rigidity and long service life under conditions of short cycle rates and high loads. In addition RA roller guides – with interchangeable rails and slides – provide set preload and accuracy for custom combinations.
Another principal design feature of the RA series is its spacers, which perform a restraining function between each of the rollers. These spacers reduce roller skew and ensure smooth running, as well as lower friction force during start-up.
The PET bottle manufacturing plant followed the recommendation and, on a trial basis, equipped one of its blow moulding machines with RA series roller guides. This machine ran for more than a year without any problems or breakdowns, reducing production downtime costs to zero. In fact, NSK’s cost savings analysis showed that the retrofit of this one machine alone resulted in a saving of €59,500, thanks to reductions in maintenance, spare parts and downtime.
In light of this positive outcome, the PET bottle manufacturer had no hesitation in upgrading its other blow moulding machines.
As this example demonstrates, components such as linear guides should be adapted to the relevant machines and production processes in order to ensure trouble-free operation. Continuous high speed production alongside stringent quality requirements call for system components that plants can rely on to meet these demands, while simultaneously facilitating cost effective manufacturing operations and excellent safety levels.
RA series roller guides represent the culmination of NSK’s experience in roller bearings and linear guide technologies. Their optimised designs take advantage of the company’s expertise to achieve smooth motion, super-high load capacity, rigidity and motion accuracy. With the capacity to handle a variety of applications, RA roller guides help support higher machine performance.
As well as the company’s extensive product range developed specifically for food and beverage industry applications, engineering support plays a vital role. Here, NSK can work together with plants to analyse possible weak points in production, measure and monitor efficiency, and where necessary propose alternative solutions.