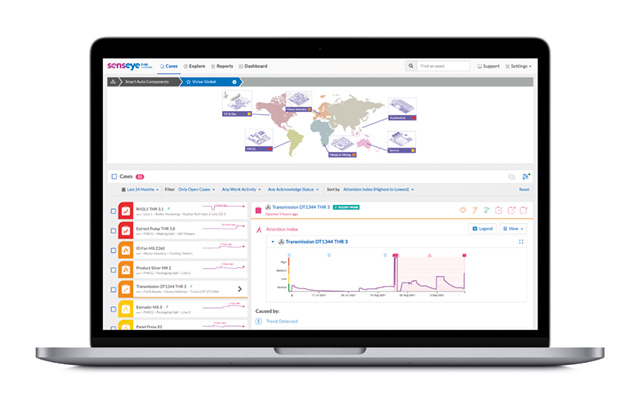
Unplanned downtime to machinery is currently costing large manufacturing and industrial organisations close to 50% more than it did two years ago due to spiralling inflation and production lines running at higher capacity, a new report has revealed.
Research by predictive maintenance software provider Senseye – which was acquired by Siemens earlier this year – found signs that firms are getting better at minimising the number of unplanned downtime incidents in their facilities.
Despite this, the cost of downtime has soared with a lost hour now setting manufacturers back $39,000 in Fast Moving Consumer Goods facilities, almost $500,000 in oil and gas and over $2 million in the automotive sector.
Businesses’ losses to downtime are also rising sharply, the report indicates; Senseye estimates that the annual cost of production stoppages for an average large plant in the sectors surveyed stands at $129 million – up 65% in just the last two years.
“It’s clear from our findings that downtime is getting more costly – much more costly,” said Senseye’s chief technology officer and co-founder Robert Russell. “This is a drag on profits that businesses can no longer afford to ignore.”
But more positively, he added: “Digitisation and predictive maintenance efforts are starting to have a significant impact, and most manufacturers have successfully reduced the number of incidents affecting production.”
There was a 23% reduction in production line failures in 2021-22 compared to a previous report in 2019-20 according to the report. In addition, major manufacturers now experience 20 monthly unplanned downtime incidents per facility, on average, which is six fewer than two years ago.
This is said to be partly attributable to increased adoption of predictive maintenance strategies and Industry 4.0 technologies. However an average large plant still loses 25 hours a month to these incidents, which is more than a full day’s production.