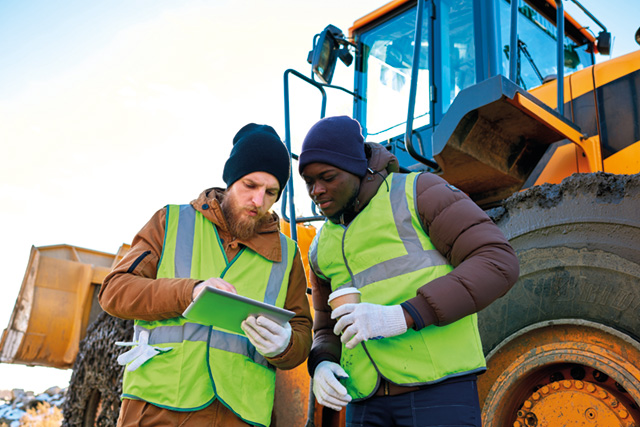
Benefits of investing in worker safety and hazard reduction in manufacturing environments outweigh the potential costs of inaction, writes David Thomas, General Manager of ZoneSafe.
Manufacturing operations are hazardous in nature – heavy machinery, workplace transport and electrical equipment all pose risk to worker safety. The manufacturing industry applies to a range of activities with differing operational practices and unique safety risks but protecting employees from hazards must remain a key priority for any plant manager.
A business’s people are its most valuable asset so it is important to take measures to demonstrate commitment to staff and this is particularly relevant when it comes to health and safety. By investing in safety, employees feel valued and safe at work, which builds a trust relationship ultimately leading to improved levels of productivity and reduced staff turnover.
Unfortunately, the decision to invest in additional safety measures and systems above and beyond mandatory requirements often comes down to cost and perceived return on investment (ROI). Technology and modern safety systems to support safe working practice are often viewed as expensive and unnecessary but it is worth looking further into the benefits of investment and the potential long-term costs when investment is not made.
Benefits of investing in safety include:
• Staff morale – Companies that demonstrate a strong commitment to worker safety see reduced absenteeism and employee turnover. By investing in employee safety, employers send a clear message that people are valued, and the employer is committed to running a fair and ethical business.
• Brand reputation – Having a reputation as a good employer that values its people makes it easier to recruit and maintain the best talent available and reassures customers and clients that the business is trustworthy. Motivated employees who are happy in the workplace are also much more likely to remain loyal and work harder to achieve business goals.
• Reduce accidents – Serious accidents in the workplace cause a ripple effect to the whole workforce and can be catastrophic for company reputation. When risks are efficiently assessed and enhanced systems are put in place, most accidents can be avoided.
• Save money – Making an initial costly investment may seem daunting and difficult to justify, but can save huge sums in the long-term. Well equipped, motivated staff perform better and the financial cost of workplace accidents to a business can be disastrous.
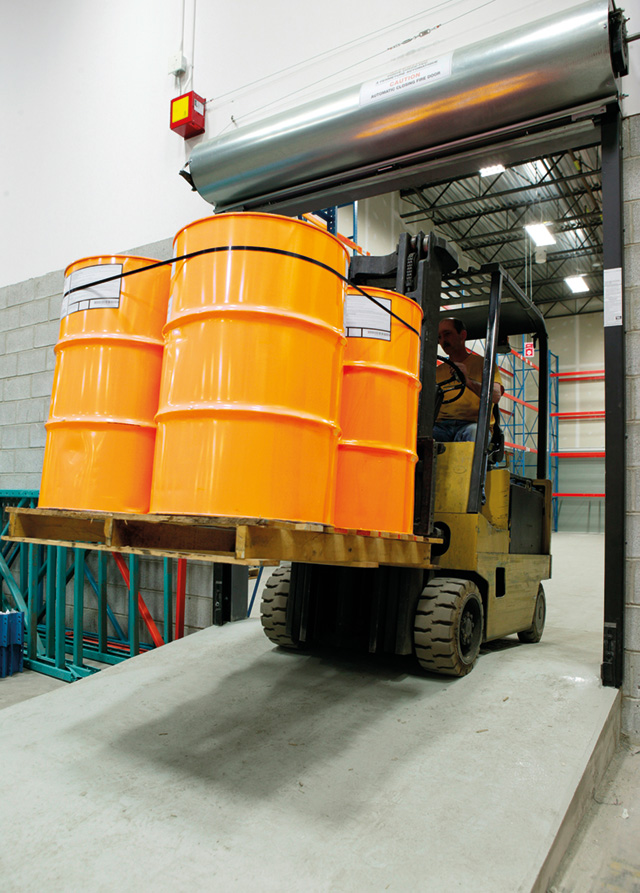
The cost of inaction
It is important to note that the long-term implications of workplace accidents and fatalities can be very destructive to a business. The Health & Safety Executive (HSE) reports that injuries resulting from accidents in the workplace cost Britain an estimated £5.6 billion every year with businesses, individuals and general wider society paying the bill.
Manufacturing HSE data for 2020/21 showed an estimated 57,000 workers sustained an injury at work and the sector has a fatal injury rate around 1.5 times the all-industry rate.
When accidents happen, the knock-on effect impacts morale, productivity, administration, insurance payments and costs time and money in additional recruitment. Reputational damage can take years to repair with some businesses never fully recovering from bad press.
Long legal battles and eye watering fines that can result from accidents at work often continue to drain a company’s finances for years after the event.
In 2021 an interiors company was fined £910,000 following the tragic death of a self-employed lorry driver who was struck by a wheeled shovel loader working nearby. The HSE found that risks had not been sufficiently assessed and safe working measures had not been implemented.
In 2019, a technology firm was fined £1.2 million after an employee sustained head and chest injuries when struck by a milling machine. The HSE investigation found the employer had failed to provide suitable and sufficient information, instruction and training to those undertaking the task.
At a time when many businesses are struggling with rising costs and supply chain issues, additional investment in the latest technology or safety equipment may seem like a ‘nice to have’, but when looking further into the long-term cost of safety incidents, is it really worth the risk?
zonesafe.com | sales@zonesafe.com | t: +44 (0)1202 868000