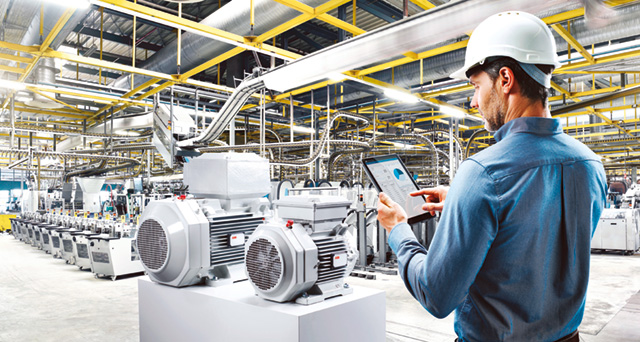
New developments in the field of smart sensors can reveal what your motors really get up to when you’re not looking. Michael Roebuck, Motion Digital Lead, ABB explores how this is helping to usher in a new era of easy and cost-effective predictive and condition-based maintenance for motors and motor-driven equipment.
In years gone by, the most reliable way of finding out about the condition, performance and maintenance needs of an electric motor was to manually inspect it. However in recent times, motors have begun to plug into the digital revolution.
Smart sensors have now come into their own as an effective way of improving efficiency and system resilience, for a minimal upfront cost. Modern smart sensor devices for motors and powertrain equipment can be attached directly to the chassis of the motor, and are typically no larger than a deck of playing cards.
Once installed, the sensors can measure parameters such as motor temperature, vibration, noise, energy consumption and bearing index. Crucially, they provide unprecedented insight into the performance and condition of a motor that would otherwise require manual inspection of the asset using specialist equipment.
Smart sensors open up vast possibilities for predictive maintenance. It in effect turns motors, which were traditionally “dumb” devices, into cloud-connected smart assets that can provide feedback in near real-time on efficiency, performance and maintenance requirements at a given time.
Rather than providing only a snapshot of a motor’s condition at a given point in time, smart sensors generate continuous data. This can then be analysed in the cloud to provide trend analysis over days, weeks, months or even years, from a single motor up to a whole fleet.
Latent issues can be flagged up and investigated long before they turn into faults, while enabling minimum downtime when it comes to repairing or replacing motor equipment. Efficiency can also be monitored; for instance if a motor is oversized for its application, this will show up in the data, allowing steps to be taken to downsize and subsequently reduce energy costs. This also aids with fault diagnosis, as the vast data set can be used to analyse persistent issues and the underlying causes of them.
Maintenance efforts and spend can be concentrated on where they are needed, i.e. sooner on hardworking assets that are prone to quicker wear, and later on assets that have an easier life.
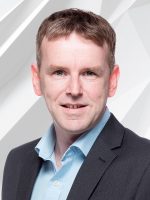
‘The more you can measure, the more you know, and the more you know, the more you can optimise.’
Michael Roebuck
ABB
Where previously a motor would require manual inspection to determine its condition, now it can be accessed at almost any time, from almost any location. Alerts can be set up when certain set points are reached to ensure that maintenance is timely, while trend data can be used to determine the optimal time to repair, replace or upgrade.
In other words, if you know that your motor is likely to need replacing in six months, you can engage your motor supplier early on. This can help to ensure that a replacement is ready and waiting precisely when it is required, meaning minimal downtime and costs. Against a backdrop of global logistics disruption, knowing six months in advance that a motor is reaching the end of its life can help to mitigate against long delivery times.
The more you can measure, the more you know, and the more you know, the more you can optimise. While the variable speed drive (VSD) can offer some diagnostic functions, and provide alerts in the event of motor failures, they do not provide a complete picture from across the powertrain of condition and performance while in operation. This is particularly the case with direct online motors which have no means of continuous monitoring.
Smart sensors, and the digital platforms and algorithms that turn the generated raw data into real insight, are helping to unleash a new era of predictive maintenance for industrial motor equipment.
https://new.abb.com/service/motion/data-and-advisoryservices/condition-monitoring-for-rotating-equipment | graeme.cain@gb.abb.com | t: 07764 472 432