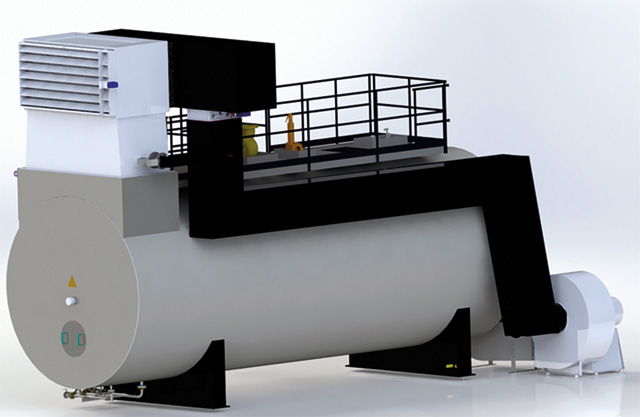
Etienne Fourie, Technical Sales Manager at Babcock Wanson, looks at the latest combustion technology designed to limit its environmental impact and accommodate new fuel types.
In all walks of life, doing things more efficiently while limiting the environmental impact of our activities has become a key focus. When it comes to manufacturing and process heating, great strides have been made, often driven by regulatory requirements.
NOx Reduction: Catch 22?
Virtually all forms of manufacturing require a heat process, provided by a burner and a boiler. However, industrial burners generate two types of unwanted by-products: CO2 and harmful pollutants in the form of methane, sulphur and nitrogen oxides (NOx).
Limiting NOx in burners is straightforward: you increase the amount of air. However, this decreases efficiency. To improve efficiency, you preheat the combustion air, but this increases the flame temperature and the production of NOx. It seems to be something of a catch 22 situation.
At Babcock Wanson, a new approach has been taken that is based around a flue gas recirculation (FGR) system. Gas recirculation is very well known, but Babcock Wanson’s unique approach is to inject it back into the boiler.
Two innovative solutions have emerged from this work to date. The R-Eco solution is a combustion air preheater that recovers heat from the combustion fumes and uses an FGR system. This technology increases both the overall efficiency of the boiler up to 98%, and significantly reduces the formation of NOx emissions in the flue gas.
It is the ideal solution when condensate returns are high and do not allow the use of conventional economisers to recover heat from the flue gas. R-Eco is compatible with installations that run on natural gas, with a flue gas inlet temperature above 130°C, and an outlet temperature of around 100°C.
The second solution is the Good Loop concept. Good Loop extracts the flue gases at the boiler outlet before re-injecting the recycled gases directly into the furnace, upstream of the refractory block, thanks to an additional dedicated fan.
This directly reduces NOx emissions from natural gas boilers by 20-30 mg/Nm3, which is firmly at the forefront of innovation in this area. Babcock Wanson’s Optimo 2 burner, for example, designed for medium size firetube steam boilers ranging from 2 to 4t/h, has emission rates in standard form that are less than 100mg/Nm3 NOx throughout the firing range when burning natural gas.
The Good Loop unique technology is not only being used in new Babcock Wanson systems, but can also be applied to an existing burner and improve its performance without any design changes.
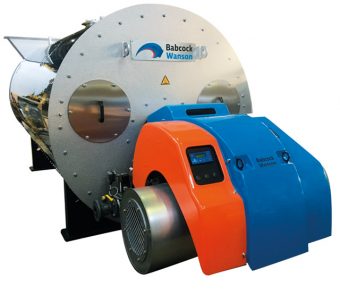
Alternative Fuels: the options
The other key development in industrial heat processing concerns substituting fossil fuels with alternative energies.
One of the major stumbling blocks in replacing fossil fuels with more sustainable alternatives is the infrastructure to deliver them. In the case of biomethane, the existing distribution networks and equipment can be utilised. Standard biogas, on the other hand, requires adaptations and quality control (moisture content, existence of hydrogen sulphide).
When it comes to hydrogen, however, its technical characteristics are quite different from those of natural gas, so its distribution and combustion require substantial infrastructure and equipment adaptations.
Looking at the emissions for these different fuel types, biogas and biomethane fuelled combustion produces the same emissions as that of natural gas. The combustion of hydrogen no longer produces CO2 but simply water vapour, so scores big points when it comes to emissions.
Where the reverse is currently true, is when it comes to production methods. Biogas and biomethane can be produced by methanisation of organic waste matter. Meanwhile hydrogen production is mainly the result of polluting petrochemical processes. ‘Green’ hydrogen, produced using processes that use electricity from renewable sources, isn’t currently widely available.
However, in anticipation of use of emerging alternative fuels, many manufacturers are now producing burners that have been designed to operate with one or more of these new types of fuel.
www.babcock-wanson.com | info@babcock-wanson.com | t: 020 89537111