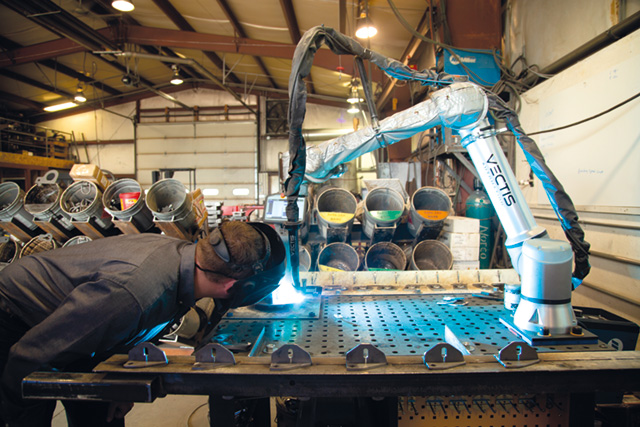
Adoption of collaborative robots could unlock fresh productivity gains for manufacturers, while demanding little in the way of maintenance, says Mark Gray, Country Manager UK & Ireland, Universal Robots.
Since the industrial revolution, we have witnessed numerous technological advancements that have transformed the world. Now, we are in the fourth phase of the industrial revolution, or Industry 4.0, which is led by the evolution of robotics, automation and the internet of things (IoT).
Industries and organisations are slowly beginning to understand the role of automation in boosting productivity, but despite this, uptake to adopt these emerging technologies has been sluggish. In the UK figures show that robot installations are below the world average and 94% of UK manufacturers believe the industry has fallen behind due to a lack of digital investment.
As the demands of each industry are increasing at an unparalleled pace, utilising collaborative robots, so-called ‘cobots’, could be the answer to solving some of these challenges. But how can cobots help in the drive towards greater automation in the UK and what are the main benefits?
Paving the way for automation
Cobots perform a similar range of tasks to industrial robots but are smaller and easier to deploy. Although they cannot match traditional industrial robots in terms of payload, they have a much smaller footprint and are more adaptable.
Many small and medium sized businesses (SMEs), believe automation is out of their reach as they can’t afford large, complex robots that also do not fit within their limited floor space.
Cobots are changing the game for these organisations, providing a more cost-effective and simple way to introduce automation into their workflows. Since close to 99% of businesses are SMEs in the UK, this could open up the door to automation for over 5.6 million organisations.
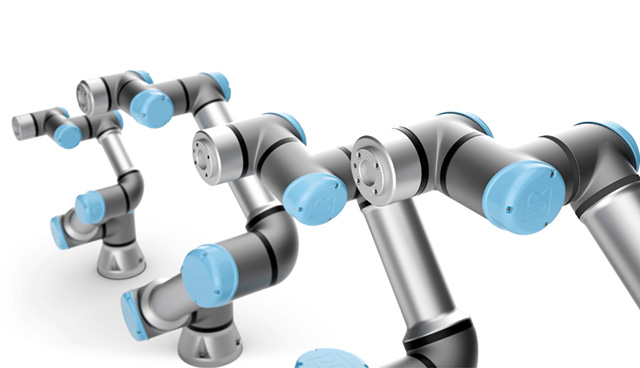
Opening up new opportunities for employees
Cobots predominantly carry out the dirty, dull and dangerous tasks once performed by humans. By automating these menial factory tasks, employees will be able to dedicate their time to more stimulating and fulfilling roles in relation to designing, building and programming the cobots.
Increasing automation will lead to skill shifts in the future workforce, with a rising demand in technology roles such as robotic engineers and programmers. These changes will open the doors to workers everywhere to either deepen their existing skill sets or acquire new ones.
Eliminating downtime with a low maintenance solution
One of the less-known benefits of collaborative robots is their nearly maintenance-free operation and long-term reliability. Not only are they easy to maintain, but they are also easy to programme. This is even the case in the toughest environments that would put human workers to the test.
The best way to maintain cobots is through preventative maintenance. This involves performing certain system checks at predetermined intervals such as operation hours of the cobots.
The preventative maintenance can reduce unexpected breakdowns or the need for costly repairs further down the line. Components can also be evaluated for general wear and tear, offering the chance for replacements to be sorted in advance, which can prevent major issues.
Many of these machines can be programmed to run automatic systems checks and can accurately diagnose potential issues, providing smart factory managers with alerts to resolve issues before they cause operational downtime.
On top of this, cobot companies also have processes in place to support care and maintenance of the machines for customers. Any tactic that can reduce downtime in manufacturing will in turn increase productivity. Essentially, if downtime is less frequent, the business will have a higher productivity level over time.
Powering the future of smart manufacturing
Spurred on by the global pandemic and Brexit, organisations are beginning to realise that dabbling in technology adoption will not be enough to survive a turbulent market. By leveraging the combined power of humans and machines, cobots will play a huge role in smart factories and will lead to significant improvements in quality and productivity levels.
With the global smart manufacturing market forecast to reach $620 billion by 2026, it is vital for businesses to continue to invest in new technologies to transform the factory floor if they are to boost productivity and plug the labour skills gap the industry is facing.
www.universal-robots.com/get-started | mar@universal-robots.com