SICK has launched its next-generation distance sensor – the OD2000 – promising high-precision reliability and ‘plug and play’ configuration in a product suited to multiple applications in factory automation and intralogistics.
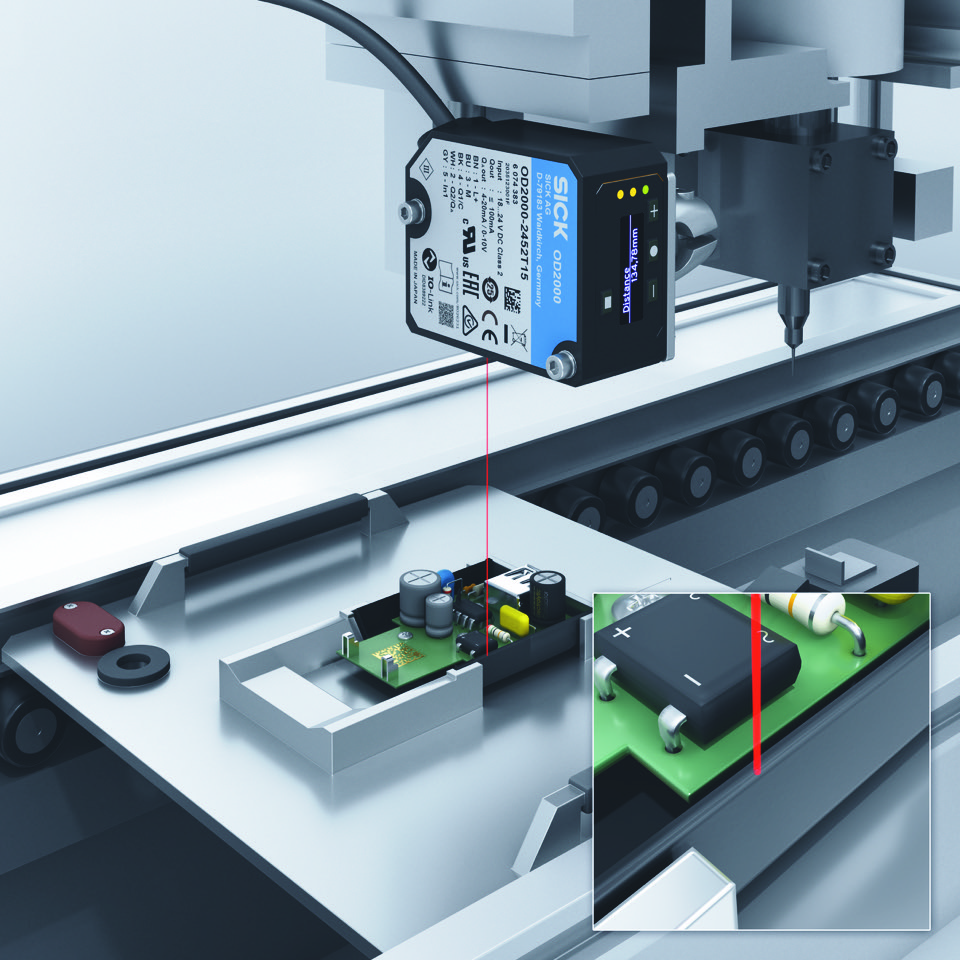
The stand-alone and compact device is suitable for wide-ranging positioning and quality control tasks in automated production and assembly, including robotics. With IO-Link as standard, it is said to offer highly-versatile machine integration possibilities, while also providing for diagnostics and condition monitoring.
The OD2000 features a large measuring range up to 1,200mm, as well as a measuring frequency of up to 7.5 kHz, enabling it to carry out demanding, high-speed measurement regardless of surface, diameter, thickness or width. Using its high-precision triangulation measurement principle, the sensor achieves high repeatability and linearity and can detect the smallest differences in height.
“With the OD2000, SICK has introduced a brand new displacement measurement family that can be relied on by production teams to assure precision performance and consistent process quality, whatever the application,” says David Hannaby, SICK’s UK Product Manager for Presence Detection.
“The universal concept will help to minimise inventories and ensure efficient ordering and delivery. The OD2000 is mounted in an instant and set up is completed in next to no time. Machine builders will particularly welcome the OD2000’s integration flexibility and communications versatility.”
An on-sensor OLED display makes parameterisation and adjustment quick and easy, according to SICK. Using IO-Link to access existing data also makes it easy to replace a sensor, should this be necessary, reducing machine downtime and preventing incorrect settings.
In addition, smart point-to-point communication for Industry 4.0 integrations is enabled via the IO-Link interface, which also means the signal transmission and power supply can use a single cable. With IO-Link, the OD2000 can output process and diagnostic data for condition monitoring and predictive maintenance.