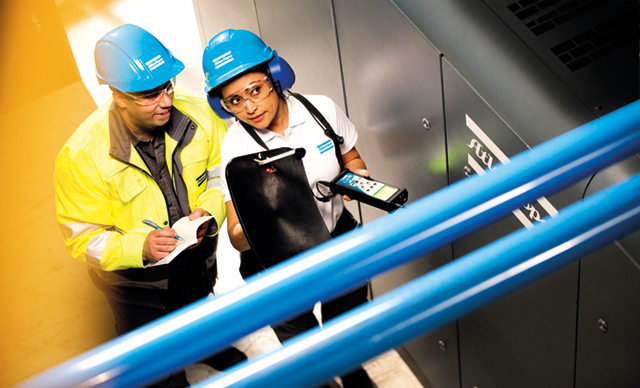
Paul Clark, Business Line Manager, CTS Sales, Atlas Copco, explains how compressed air systems health checks and energy audits carried out in an industrial environment can reduce costs, improve environmental performance, and help deliver energy efficiency improvements, and how these gains can be sustained with planned preventative maintenance.
Compressed air systems account for 10% of all energy used in global industry, and of that, between 10 and 30% is wasted on leaks; even a 3mm leak could cost around £2000 a year with a loss equivalent to 16 tonnes of CO2 emissions. Any optimisation of compressed air systems impacts performance and efficiency significantly, lowering fuel bills and reducing carbon footprints.
Optimising compressed air systems
It follows that plant managers need to ensure that a compressed air system is operating to its full potential. That means identifying and eliminating air leaks, optimising performance, and reducing energy consumption to drive down costs.
The simple and most effective means of achieving these goals is to carry out a health check and energy audit – assessments that can be performed quickly and accurately with zero disruption to the users’ production operations.
One important aspect of these checks is identifying and eliminating air leaks caused by issues such as corrosion, poor pipe connections, or bad seals – problems that can add up to a significant amount of wasted energy over time.
Today’s advanced technology employs ultrasonic leak detection equipment which operates without interrupting plant production. It reaches compressor system areas that are hard to access and locates all air leaks. Furthermore, the latest state-of-the-art acoustic imaging cameras can help detect leaks in compressed air systems up to ten times faster than traditional methods, a procedure followed by a supporting written report that can provide more details on leak locations, photographic evidence of holes, leak severity in litres/ minute, energy costs, positions, and costs to repair.
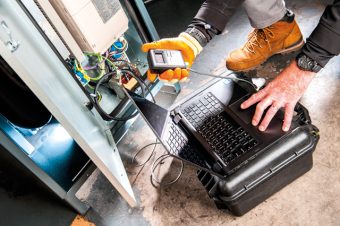
Health checks and energy audits
With the technology in place to provide fast, accurate, and cost effective leak detection, leading compressor technology specialists, such as Atlas Copco Compressors, have developed three levels of health checks and energy audits for compressed air installation:
Level 1 – Free visual inspection and energy potential calculations (EPC): A visual assessment covering information such as compressor room environment, determining any air quality issues, and a visual inspection of all compressed air equipment on-site, including appropriate capacity, ISO compliance, unproductive running, and pressure levels.
This procedure provides a summary of equipment health and outlines running equipment improvements, as well as wasteful practices or non-conformance with ISO standards.
EPC calculations can also be carried out, focussing on the power usage of the compressors, load v. unload hours, and average leak assessment. This calculation identifies whether there is a requirement for a Level 2 assessment and provides an indication of the tangible savings that it would bring.
Level 2 – Energy assessment and recommendations through data logging: A real-world assessment based upon the findings of data logging equipment fitted to each compressor. The devices record and then map the energy consumed over a full week period and show the actual running hours and calculated air usage.
Engineer specialists can then calculate a realistic energy savings potential, make simulations, and provide recommendations to achieve optimal energy efficiency.
Level 3 – Full audit to ISO 11011:2013 standard: This provides a premium assessment of a range of parameters, such as flow testing, air leak detection, air quality testing, measurement and analysis of pressure and dewpoint throughout the wider system, from compressor room to production processes.
Included in the audit are reporting and discussions of the most suitable methods to reduce energy costs and CO2 emissions.
Preventive Maintenance
Maintaining the health, energy efficiency and potential performance levels of compressor systems revealed by these checks and audits requires the oversight and guarantee that only planned, regular system maintenance solutions can ensure.
That is why leading equipment suppliers tailor their service plans to best fit user needs. These options can range from fixed priced service and preventive maintenance programmes to total responsibility packages for complete compressor care – all to keep production processes running, keep costs under control, and protect capital plant investment.
www.atlascopco.com | compressorsGB.web@atlascopco.com | t: 0800 181085