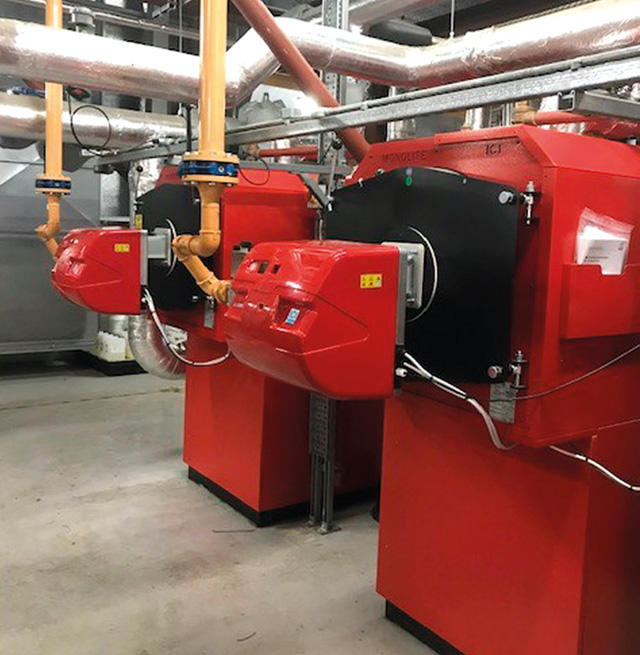
Part of the solution to improving air quality is to reduce emissions of nitrous oxides from combustion plant. Paul Sharp, C&I Sales & Marketing Director of Riello Burners, considers two technologies that are making a real difference.
For some years now burner manufacturers have been refining their designs to deliver improved performance and meet increasingly stringent environmental regulations. One area that has received a lot of attention is reducing nitrous oxides (NOx) and there are two very effective technologies now on the market for industrial and commercial installations.
These are pressure jet burners using flue gas recirculation (FGR) and premix burner technology – both providing effective NOx reduction when used in the most appropriate application. The differences between these relate to how the gas and combustion air are mixed at the point of ignition.
As the name suggests, in premix burners the air fuel mixture is created upstream of the combustion head, whereas with FGR the gas and air are mixed at the point of ignition on the end of the combustion head. The latter is probably the most familiar arrangement to readers, but the premix design is proving popular in certain applications.
Premix benefits
Premix packaged burners, currently available in outputs from 5kW to 3MW, offer a number of benefits – including low emission levels to ensure compliance with current and anticipated legislative requirements. Even on large burners up to 3MW, we have seen NOx emissions of lower than 30 mg/kWh – and some independently witnessed site tests even down to less than 20 mg/kWh.
Premix burners also support high turndown ratios up to 8:1 on specific applications to ensure optimum performance at varying heat loads. This makes premix burners ideal for a host of applications from condensing boilers through to the process sector including spray booths and industrial ovens amongst others.
Another benefit is reduced noise levels – potentially 30% lower can be achieved compared to other forms of combustion technology. Variable speed drive motor technology can also be utilised to provide additional noise reductions and electrical cost savings at lower heat outputs. Advantages of a reduction in flame noise further reduce the noise levels experienced at the flue exhaust.
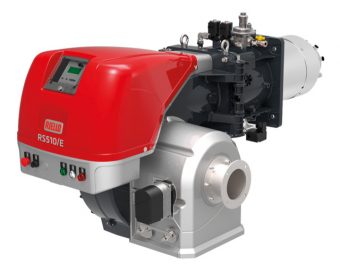
In terms of control, premix burners can operate with a range of options, from progressive two-stage operation to fully modulating via 0-10V or 4-20 mA. Full electronic control is also available, which offers operational display and diagnostic features at a glance.
FGR benefits
Flue gas recirculation (FGR) is a proven method for reducing NOx levels but historically has not been widely used in the UK as it requires additional controls. However, with tighter NOx regulations it is proving to be a very effective way to meet these stricter requirements and FGR burners are now available with outputs from 500kW to 32MW, to provide ultra-low NOx emissions as low as <40mg/kWh.
The principle of FGR is that a percentage of flue gases are piped back into the burner air supply system to reduce the flame temperature. The recirculated flue gases are relatively cool and inert, and with the inhibiting presence of CO2 they reduce peak flame temperatures.
FGR burners need to be used in conjunction with electronic cam control of both the combustion air/fuel ratio via separate servomotors and a further separate servomotor to control the flow of the re-circulated flue gas. The use of FGR with electronic cam control helps to deliver significant improvements in energy efficiency as well as reductions in NOx emissions – an important consideration as fuel costs continue to rise.
Summary
As with any technology, the correct application is crucial to a successful outcome. Periodic maintenance is also essential for the good operation, safety, yield and duration of the burner.
Both of the technologies described here have a lot to offer, the key is to pick the right one. To that end, it pays to work with a supplier that has the technical expertise to advise on the best solution.
www.rielloburners.co.uk | info.riellouk@carrier.com | t: +44 (0) 1480 432144