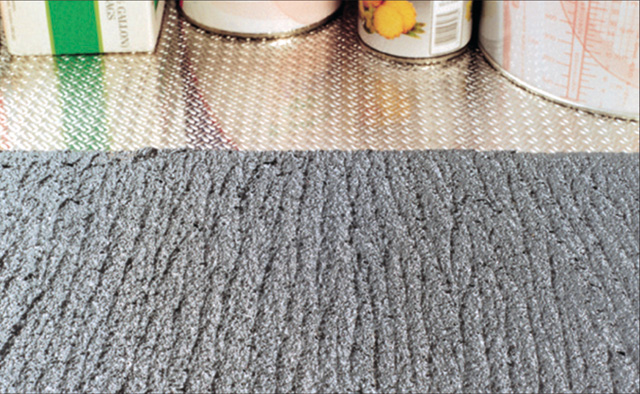
Bob Orme, Senior Technology Specialist at Henkel, explains the application of anti-slip coatings to help prevent slips, trips and falls.
Workforce injuries resulting from slips and falls are one of the leading, longstanding causes of unplanned workplace absence. The latest statistics from the Health and Safety Executive (HSE) make for a sobering read. Of the annual 492,000+ non-fatal injury reports it received in Great Britain, 33% cited slips, trips and falls – on the same surface level – as the cause. This translated into millions of lost working days in one year.
The application of anti-slip coatings to risk areas not only makes sound sense from a health and safety perspective but also from an operational and cost efficiency standpoint too. Coatings are available with a range of characteristics that create a durable anti-slip finish for people and vehicles, ranging from light to heavy traffic.
LOCTITE® is a brand with notable benefits in this field. Products in the range outlast and outperform typical sand-inpaint systems and tapes and are proven to be the strongest, most aggressive anti-slip methods available. Applications include ramps, walkways, stairs, changing rooms, machine shops, assembly areas, warehouse floors and loading docks.
They are suitable for use on concrete, asphalt, wood, ceramic, fibreglass and metal surfaces with applications across industry, commerce and in the public service, utilities and transport sectors.
Choice of solutions
LOCTITE anti-slip coatings based on epoxy adhesive technology are designed to provide tough, long lasting, anti-skid surfaces that are easy to clean, resistant to chemicals and available with fire resistant qualities when cured. Complementing these products are water-based acrylic anti-slip coatings that are resistant to chips and scuffs and are impact and UV resistant, making them suitable for both indoor and outdoor applications.
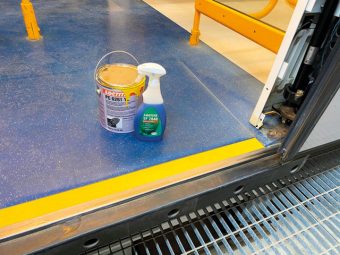
Application is simple and quick. Ensure the surface is grease, oil and contaminant-free, and apply masking tape to mark the area. The product is then applied using a paint roller or trowel and hard roller; the tape is removed to leave clean, straight edges.
As the choice includes a solvent-free formulation, the technology can also benefit odour sensitive environments such as food processing facilities, hospitals and other confined areas.
This solvent-free anti-slip coating is LOCTITE PC 6315, a two part, black, epoxy that is fire retardant when cured and resistant to most acids, alkalis, solvents, grease, oil, salt water, detergents, alcohol, petrol, jet fuels and hydraulic acids. It is typically used to create a textured and extremely durable surface that can also withstand heavy vehicular traffic, such as forklifts, AMRs and of course, personnel.
Any demanding and heavily used industrial area, including those found in factories, loading/unloading areas, mining and even in the oil and gas industries, can be addressed with this hard-wearing material. It can be used to replace other less effective anti-slip materials (such as rubber strips) on surfaces that include concrete, wood and metal.
Another popular option is LOCTITE PC 6261, a single-part epoxy that is quick and easy to apply, extremely durable and designed for application in areas of high pedestrian footfall or light rolling traffic. It is also fire retardant when cured and resists petrol, oil, acids, alkalis and aliphatic solvents. Application is by roller for a ridged profile or it can be sprayed for a uniform finish.
As LOCTITE PC 6261 is available in yellow and grey, it meets the requirements for high visibility strips that can be repainted without removal or rework such as that required with anti-slip tape, for example.
A tram operator making that replacement has enhanced passenger safety and saved maintenance time. Its success has led to the coating being considered for use on the company’s bus fleet and other areas with high footfall.
www.henkel-adhesives.co.uk | t: +44 (0)1442 278000