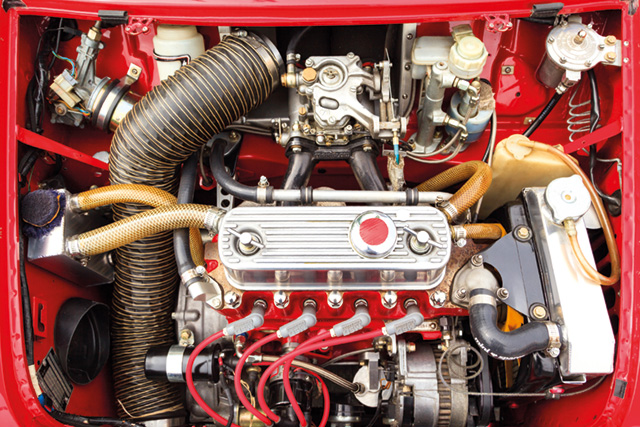
ABSTRACT
UK PLC is facing an unprecedented engineering skills shortage at a time when improvements to manufacturing productivity are vitally important following Brexit and the war in Ukraine. This article examines how businesses can safely introduce basic maintenance skills into the operator workforce using the structures of Total Productive Maintenance, Autonomous Maintenance and Operator Asset Care. It also quantifies some of the benefits that can be achieved and lists some of the tasks that companies have successfully transferred to operators. By introducing operators to basic maintenance, skilled technicians can focus on higher level activities as can their supervisors and managers. It is crucial to develop technical operator skills in a structure like TPM, AM or OAC to ensure that the skills are retained, work is appropriate to the level of the individual and is sustained over months and years.
Introduction
In my late teenage years, I really loved cars and car maintenance. Encouraged by my dad, I had a succession of old bangers, mainly Minis and Vauxhall Vivas.
Back in the 80s there was no limit to what I was prepared to take on: New clutch, new brake shoes and pads, bleeding brakes and swapping engines. Don’t even get me started on the sound systems.
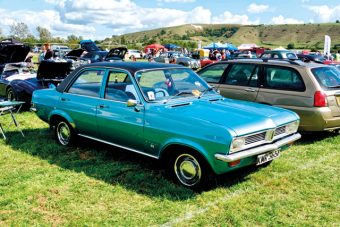
I’d worked really hard on one car, respraying it Bachelor Blue. It went nicely with the black vinyl roof. Then my dad, much to my horror, told me I needed to give it to my sister who was at university. Caroline needed to take great care of this Vauxhall Viva. I taught her all of the basics such as oil, water and brake fluid checks. Tyre pressures etc. This noise means you need to do such and such.
Caroline was the driver, not the mechanic, but the car spent less time off the road because she could spot the early warning signs and drop it back at the family home for me or my dad to fix it.
The factory floor is no different. Operators spend days by their machine. They know how it should sound, feel and smell. Many more serious stoppages have been averted because the operator has told the technician about a fluid leak or strange noise. Companies can save many millions of pounds if operators are engaged and carry out routine, low risk maintenance tasks like Cleaning, Inspection, Lubrication and Tightening (CILT). Other tasks might include replacing filters and aligning sensors.
So, I hear you ask, does every factory involve the operators in first line maintenance? Not according to MCP’s AMIS assessment1. 80% have no operator involvement in maintenance. 45% have no formal maintenance training programme.
Many engineering managers have real worries about the age profile of their maintenance workforce and reliance on external contractors. 19.5%2 of engineers currently working in the UK are due to retire by 2026, leaving a skills, knowledge and experience gap.
Greater operator involvement in high frequency-low risk maintenance tasks can free up valuable maintenance resource time as can training operators to operate their machines more effectively. In some factories, maintenance technicians spend a large proportion of their day hand-holding operators.
If we look at the graphic below, we can see the contribution of operation, design and maintenance towards operational excellence. We can see that optimising operations has the biggest impact.
Some factories have experienced accidents through staff not having the correct skills and knowledge to carry out tasks competently*.
In my recent experience, in separate incidents, staff have lost sight in one eye, have broken teeth and lost use of a hand. In addition to damaged staff, I have recently witnessed the lid of a £50,000 centrifuge being tightened by being clubbed by a baseball bat sized stainless steel bar. The mechanical damage to the centrifuge was significant. A simple redesign of the tooling to give more leverage would take away this need for violent physical assault.
*Definition of competence: Complete the task safely, in a reasonable length of time and to the right standard.
As employers we have a moral obligation to ensure that our staff are competent to carry out the tasks we want them to do.
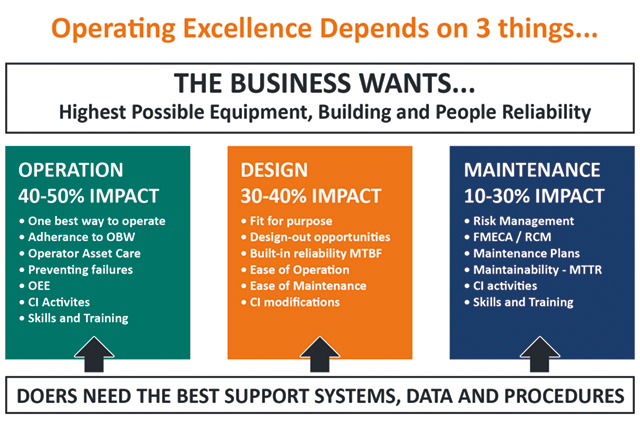
We need to train staff offline and assess their underpinning knowledge. Then we need to have a structure of coaches and assessors in place to deliver on-job training and then sign them off as being competent to do selected tasks in the workplace. And then robust records need to be kept. There may also need to be an expiration date on the assessed task. Typical tasks that we have trained operators, in a food environment to carry out in factories include:
• Clean and align photoelectric cells
• Clean and align other sensors
• Lubricate and clean excess oil/grease from all parts of line
• Check and top up oil levels in gearboxes
• Check chains and sprockets on drives
• Empty and clean vacuum bag
• Re-align/adjust timing on scroll star wheel
• Replace damaged grippers
• Clear jams
• Adjust torque heads
• Changeover of product and size
• Clean printing heads on printers
• Change inks and solvents on printers
• Assist engineers on overhauls on all equipment
• Carry out cleaning and wash through
• Break down and refit pipe runs as required
• Set up and adjust glue and labelling system
• Set up feeder scrolls
• Replace shear pin
• Replace belts
• Re-set and adjust selected components
• Adjust cut off sealer sleeve
• Check shear pins on pallet lifter
• Reset timing on selected equipment when required
• Check, remove, clean and replace air system separators/filters
• Check bearings in selected equipment and replace if necessary
• Strip down, inspect and replace impeller in mono pump
• Replace rollers on conveyors
• Replace conveyor links
• Service/change sealer bar on shrink wrap
• Change materials, shear pins and other wear items on shrink wrap
• Clean and service ink jet printer
• Maintain / service selected change parts
• Maintain/service gripper cylinder
What is the process for delivering operators who can carry out these maintenance activities?
• Identify tasks you want the operators to do
• Select accreditation process and partner
• Train trainers and assessors
• Develop Standard Operating Procedures for operator tasks
• Deliver generic mechanical maintenance skills training
• Assess practical skills through competence assessments
• Assess theoretical knowledge through written tests
• Award certificate and celebrate
• Support operators to carry out identified tasks with on-job coaching and assessment
• Periodic visits from MCP assessor
• Build portfolio
• Sign off portfolio
• Celebrate
What does the generic mechanical maintenance skills training look like?
• Isolation procedures
• Small hand tools (fasteners and fixings)
• Measuring tools
• Production of sheet steel component using hacksaw and file
• Use of drilling machine to produce holes
• Tapping threads
• Lubrication
• Levers and linkages
• Springs and Cams
• Belt drives (Vee belt and synchronous belts)
• Chain drives and Conveyors
• Basic fault finding
• Sensors and seals
• The basic theory of pneumatics
• Basic pneumatic components
• The effect of changing the flow rate and pressure on circuits
• Pressure and flow regulators
• Compressibility of fluids
• Similarities and differences between pneumatics and hydraulics
• Basic fault finding
• Different types of valves and methods of operation
• Valve components
• Valve identification and practical inspection
• Inspection and changing of seals on a like for like basis
What are the benefits of technical operator training?
• Motivation and development of staff
• Improved staff retention
• Formal targeted training with direction and focussed on business need
• Encouragement of teamwork through coach and assessor (maintenance) communicating more with production department
• Refocussed training budget
• SOPs and training packages are written around business need
• Safe job; Timely job; Right first-time job
• Improved productivity as downtime is reduced due to increased skills base
• Cross cover of skills in event of absenteeism, sickness etc.
• Nationally recognised qualifications where appropriate; skills are validated
• Training records meet and exceed those required by HSE etc
Apprenticeships
We have developed an apprenticeship delivery model for the Engineering Operative in maintenance. It is a 12-to-18-month programme with no prior entry requirements. There would be classroom delivery of the qualification against the following knowledge units:
Mandatory Unit
• 001 Engineering environmental awareness
Optional Units
• 002 Engineering techniques
• 014 Engineering maintenance safety practices
• 015 Engineering maintenance techniques
• 016 Engineering maintenance planning
• 018 Fitting & Assembly techniques
• 038 Business Improvement Techniques
Skills units are as follows:
Mandatory Units
• 001 Complying with statutory regulations and organisational safety requirements
• 002 Working efficiently and effectively in advanced manufacturing and engineering
• 003 Using and Interpreting engineering data and documentation
Optional Units (examples)
• 005 Maintaining Mechanical Devices and Equipment
• 084 Handing over and confirming completion of maintenance or installation activities
• 086 Carrying out maintenance activities on mechanical equipment
• 087 Carrying out scheduled maintenance on mechanical equipment
Other approaches
Instead of training operators to do maintenance tasks, some companies have taken a different approach and put skilled technicians on the production line. When there is a problem or planned maintenance then the technician carries out these tasks. The remainder of the time the skilled technician is a member of the production team. This approach generally works well for a number of years. The technician either gets bored and leaves or becomes de-skilled and needs re-training.
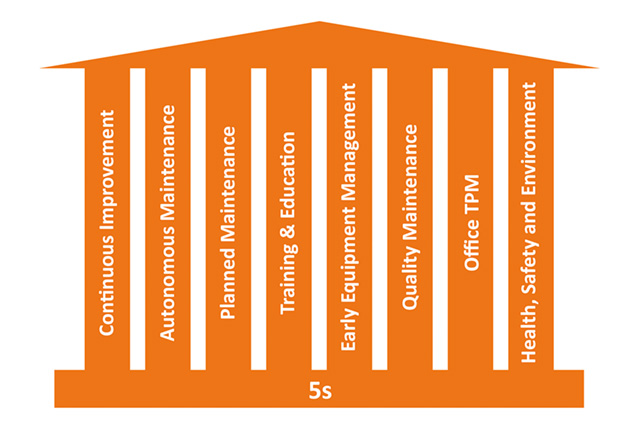
Ensuring the investment pays dividends
To embed technical operator training in the culture of a company we need a strategic approach like Total Productive Maintenance (TPM), Autonomous Maintenance (AM) part of TPM), Operator Asset Care or a focused operator apprenticeship scheme.
Total Productive Maintenance
TPM was originally developed in Japan. It strives to achieve a continuous production cycle without any breakdowns by maintaining and improving the production and quality systems. Engaging all departments in planning, production, quality and maintenance are the main aims. TPM affects all departments.
It may lead to major organisational realignment. There will be a large investment in training, factory floor resources and support staff; it is a huge challenge. It is at least a five-year journey. It can become a high-level topdown programme. Many companies decide that this elephant is too big to eat. Others choose to work with a consultancy to guide them through this process.
Autonomous Maintenance
Autonomous Maintenance is a pillar of TPM. An operator trained in AM will practice:
• Efficient machine operation
• Initial inspection and cleaning
• Removal of cause of contamination and improvement of access
• Inspection and monitoring of machine performance
• Standardisation of visual maintenance
• Continuous improvement
Incorporating Continuous Improvement into the programme
Following a technical operator programme, be it linked to an apprenticeship programme or otherwise, the factory floor-based teams become more autonomous with less supervision. Operations and maintenance share continuous improvement, asset care and maintenance activities.
Through the work of improvement teams, maintenance activity moves from reactive through preventive bringing stability to the manufacturing process.
The responsibility for manufacturing output or OEE* is shared between production and maintenance.
*A great measure of manufacturing output is OEE or Overall Equipment Effectiveness. OEE is calculated by multiplying Availability, Performance and Quality. OEE encompasses all losses, resulting in a measure of truly productive manufacturing time. It is the gold standard.
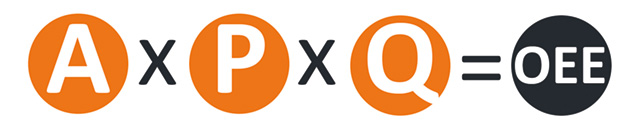
It is the best metric for identifying losses, improving the productivity of the equipment and quantifying performance.
Availability takes into account unplanned and planned stoppages. Performance includes slow cycle times and short stops. Quality addresses defects.
An OEE score of 100% means 100% quality parts produced, in the fastest possible time with no stoppages.
Operator Asset Care
MCP is also working with companies to make better use of their operators’ abilities without the onerous, all-pervading constraints of TPM or AM.
What is Operator Asset Care?
• An essential part of the ‘world class’ approach to maximising the effectiveness of operational assets and processes within the company
• A joint venture between production and maintenance which offers a structured approach to achieving and sustaining World Class Operating Performance
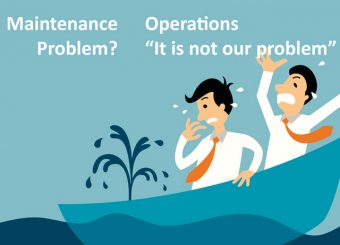
OAC facilitates effective utilisation of the operators’ latent capabilities, time and work habits to improve asset condition and reliability. It equips operators with the knowledge and understanding to participate in asset care activities to deliver sustainable improvements in equipment reliability.
Just like AM, process activities and maintenance tasks are integrated. There is shared responsibility for asset condition, reliability and performance.
Unlike TPM and AM, it need not be part of a company-wide change programme. It can be piloted in a discrete area. The learnings can be reviewed before rolling out the programme wider.
When should OAC be applied? It should be applied when customers want to involve their operators in maintenance without the encumbrances of TPM and AM. Although it is limited, it still requires the same wholehearted backing of senior management. It is the scale that is different which makes it more attractive to customers.
An OAC programme requires less investment than TPM or AM. It also reduces risk. At the start of the programme we will take time to understand the culture of the company before the initial training is pitched to sell the concept to the operators and technicians. Towards the end of the initial input we will get the operators and technicians to articulate what the business needs to do to improve. If the main thrust of the improvement activity comes from the operational and maintenance staff, endorsed by MCP and the management of the company then it is much easier to get commitment.
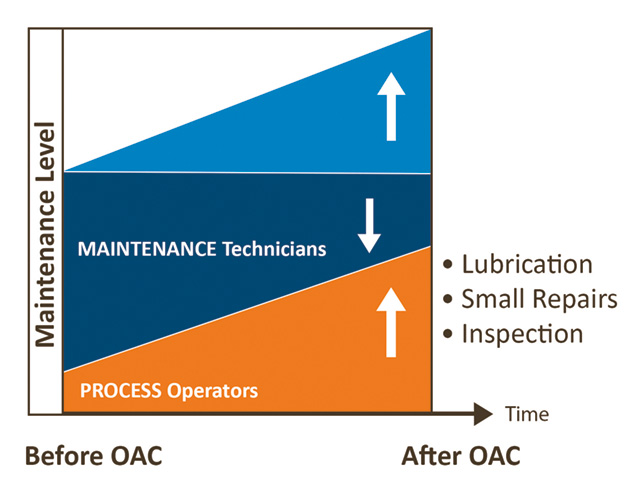
Skills are developed to enable operators to undertake maintenance and process improvement tasks. There is support and a regulatory framework.
A good place to start is a department or line with lots of opportunity for improvement. Plants that have embraced OAC with management backing and investment have seen an increase in quality output within six to eight months. One company achieved an OEE improvement of 10% within this timeframe. Previously that department was not a popular place to work. Now there are lots of applicants for vacancies in that department.
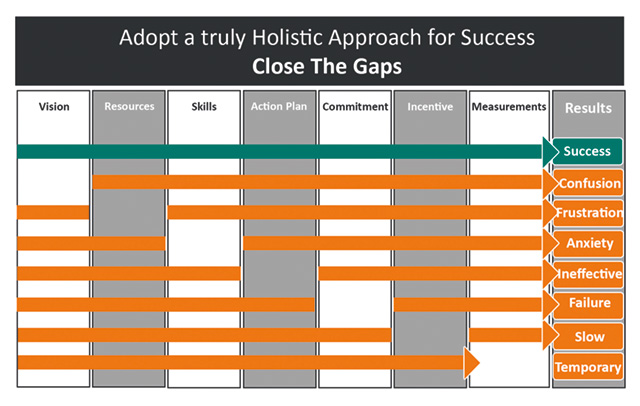
In summary, technical operator training, TPM, OAC or a structured apprenticeship scheme can greatly benefit companies. They are all rewarding journeys for the individuals, shifts, departments and companies. TPM is the longest and most arduous journey. The results can be hugely significant. However, most businesses are not prepared to wait three to five years to see a return on investment. If you want a more pragmatic approach and a quicker return on investment, then OAC is the path for your business. A vision, resources, skills, plan, commitment, incentives and measurements are essential to yield great results, regardless of the approach you choose. The graphic below describes what can happen if any of these elements are missing.
For more information on technical operator training, Operator Asset Care or Total Productive Maintenance please contact John Saysell at MCP: jsaysell@mcpeurope.com
References
[1] AMIS assessment www.theamisjourney.com
[2] 19.5% of engineers currently working in the UK are due to retire by 2026, leaving a skills, knowledge and experience gap. Engineering Today. The Supply and Demand for Engineers in UK, January 2018.
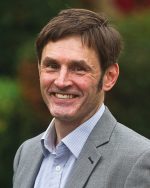
John Saysell
Director of Technical Training,
MCP Consulting Group
jsaysell@mcpeurope.com