Nick Barrett, Editor
nick@maintenanceandengineering.com
@MaintOnLine
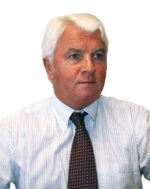
Digital transformation and Industry 4.0 technologies are helping manufacturers to unlock significant productivity gains, leveraging data to boost efficiency and, when it comes to maintenance, predict and deal with problems before they force unplanned downtime.
However the adoption of modern, connected technology has also opened the door to new risks by leaving valuable data and equipment vulnerable to ransomware attacks and other cyber security threats.
Manufacturing as a sector appears to be a particular target and one where danger is on the rise. The latest research from IBM indicates that it was the most attacked industry in 2021 – having overtaken financial services for this title – while 61% of cyber incidents at operational technology (OT) connected organisations were in manufacturing.
“Threat actors understand the critical role manufacturing and energy play in global supply chains and are seeking to disrupt these organisations because of the ripple effect it can have across multiple industries and the pressure these multiplying effects create for victims to pay a ransom,” the firm’s Security X-Force Threat Intelligence Index report points out.
The report also highlights that ransomware criminals find manufacturing to be an attractive target due to the industry’s low tolerance for downtime. Cyber attacks on the sector could involve anything from data theft through ‘phishing’ to the disruption of control systems that allow facilities to operate, which may even result in complete factory shutdowns.
In other words, the stakes could not be much higher for a productivity-focused business.
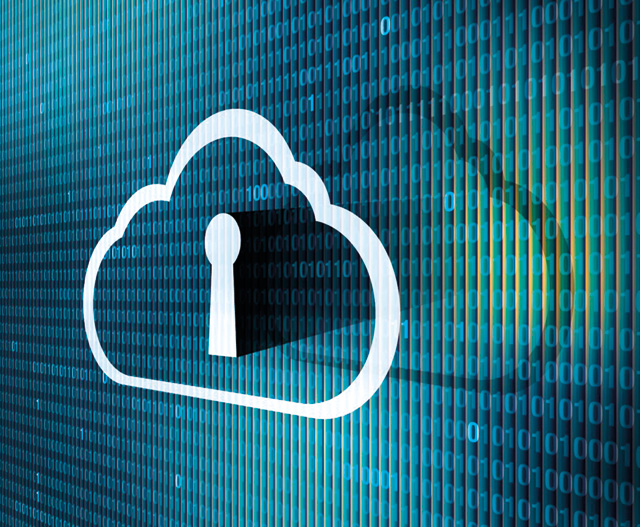
In light of the risks, it is surprising that further studies from Siemens indicate that less emphasis is typically placed on protecting critical OT infrastructure against cyber risks as opposed to IT systems. The two need to be jointly responsible for keeping connected factories secure, it says.
Research by Deloitte backs this up and says companies should look beyond traditional IT tools to assess and address risk in the OT manufacturing environment. It also finds that around a quarter of firms do not perform annual cyber risk assessments and many manufacturers seem unprepared to deal with the potential threats.
It is clear then that the issue needs to be taken more seriously; there is no use in companies investing in smart factory initiatives if losses due to cyber crime end up outweighing the productivity gains originally intended.
But what can be done to increase the chances of successfully fending off an attack? Developing new digital skills and fostering a strong culture around security will be important as part of a broader strategy to minimise risk. Investment in security tools also has a role to play and it was positive to read recently about trials of a prototype cyber security technology which are being organised by the Digital Catapult.
Ten companies, many of which operate within the Internet of Things sphere, will test out the system known as Morello which has redesigned the architecture of a computer’s central processing unit. This could help stop around two thirds of hacks, cyber attacks and data breaches, it is estimated.
Developments of this kind will hopefully help to keep manufacturers safe from cyber threats. But it should be borne in mind that as security systems become more sophisticated, so too will the techniques used by criminals to bypass them. Continuous evolution will be critical for companies to stay one step ahead.
Improving pipe inspections with automated robots MTC
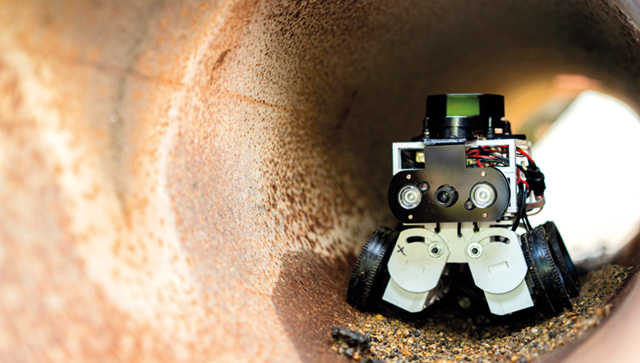
Inspection of pipes and tubes used in the manufacturing and process industries – as well as those carrying water, gas and telecoms utilities – is a challenging and comprehensive task for maintenance engineers. But inspected they must be, for problems such as corrosion and leakages, and this process could be about to become easier through advances in robotics.
In May, the Manufacturing Technology Centre unveiled a small autonomous robot capable of navigating itself untethered in the confined surroundings of a pipe network, undertaking inspection work as it goes. Nicknamed ‘Ratty the Robot’, the machine features a laser based navigation module which reduces the need for a human operator.
Although primarily intended to help utilities companies achieve cost and efficiency savings, it is easy to see how the robot could benefit a range of sectors including by patrolling pipework in a. factory setting, reducing failure rates and flagging up potential problems. A further advantage is around the potential to reduce human exposure to hazardous environments such as gas leaks.
And, as the MTC’s advanced robotics research engineer Dr Mahesh Dissanayake says, “with technology advancing all the time the next exciting step could be a robot which not only inspects pipework, but is capable of carrying out repairs remotely without having to dig up roads”.
He adds: “The transferable technical know-how will also allow the MTC to support the automation of other activities in hazardous or difficult environments.”
To date, the robot has successfully undergone simulated trials at a test facility in Yorkshire, and while the next steps are unclear, the prospect of being able to deploy a fleet of self navigating robots which can identify and repair problems with utilities and other pipe networks will undoubtedly be an exciting one for maintenance engineers.