Mitsubishi Electric has announced plans to launch a 3D simulation tool which uses ‘digital twins’ to support the design and construction of manufacturing facilities and verify envisioned production operations.
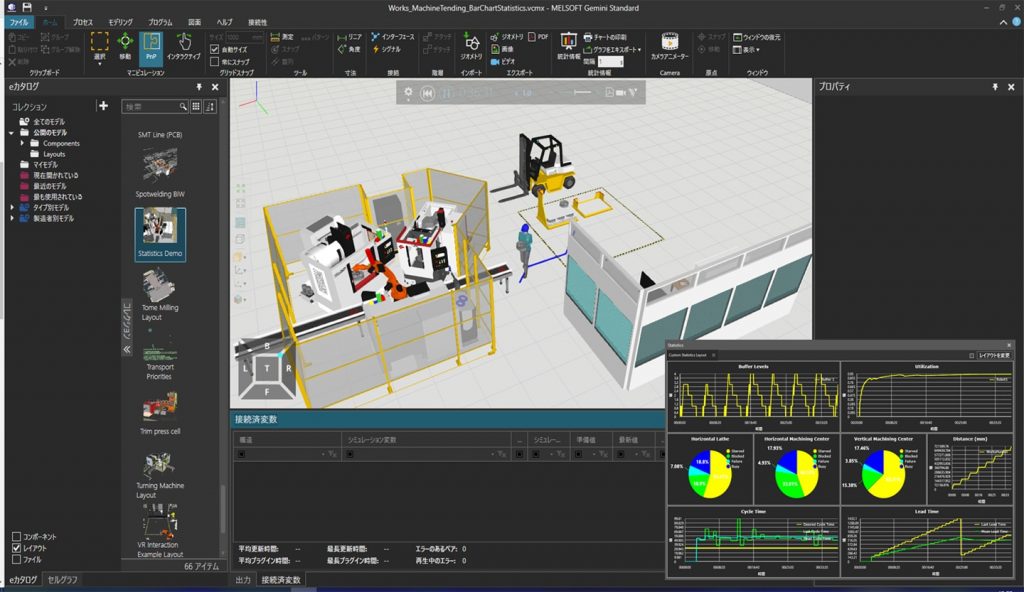
By connecting to a variety of software and factory devices, the MELSOFT Gemini tool will visualise, simulate and help streamline manufacturing work processes ranging from design of production facilities to operation and maintenance.
The product is set to launch on 28 April. Mitsubishi Electric says the Covid pandemic has caused restrictions on human mobility and face to face communication, which has made it difficult for manufacturers to install and maintain production facilities.
Meanwhile, the sector is seeing growing demand for digital transformation. These industry trends have brought the spotlight onto the use of digital space for solving various issues on production sites, it adds.
MELSOFT Gemini promises to help solve these issues and streamline processes by using digital twins to simulate the operation of production facilities before they are installed and become operational in the real world.
The tool connects to MELSOFT simulators, which are available separately as part of the ‘MELSOFT iQ Works’ software package, to simulate the control of devices such as programmable logic controllers (PLCs) and motion controllers (Servos).
During the verification process, facility engineers can check the status of the planned production facility by looking at the PLC sequence program, reviewing displays of operational waveforms and/or video data when an error is found.
Detailed checks for possible operational interference can reduce the need to rework processes as well as helping to improve quality, it is claimed. In the operation and maintenance phases, the causes of abnormal occurrences in the production line can also be determined quickly using visual data, which is provided to line operators through MELSOFT Gemini.
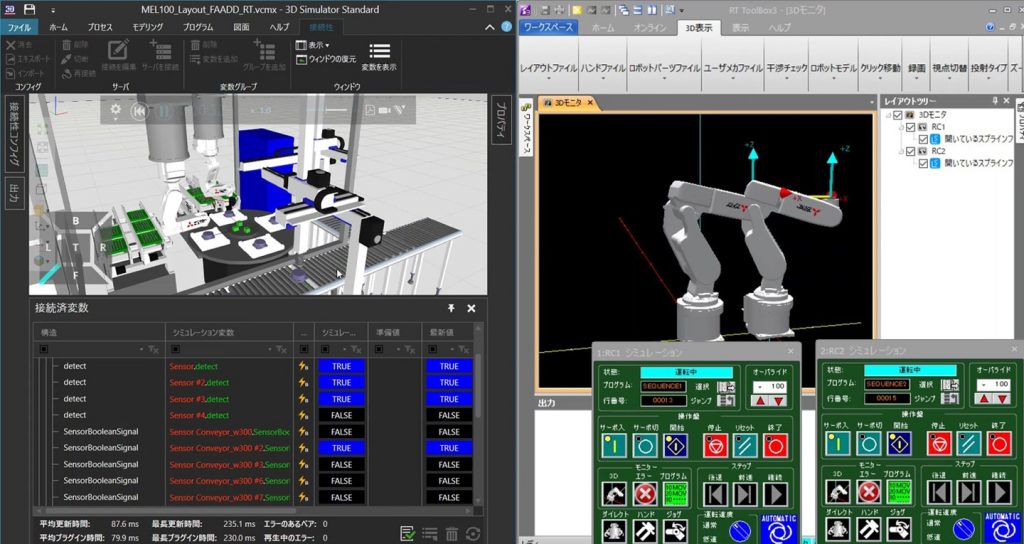
The tool’s supported hardware ‘e-catalog’ features approximately 2,500 types of production equipment, including robots, conveyors, processing machines and more, which can be combined in a simulated 3D production facility. Parameters can be easily set on the 3D screen to adjust the layout of the production line.
In addition, various graphs can be used to visualise and analyse simulation data on different operating rates of production, thereby supporting the design of efficient production lines. Equipment operating status, production task duration, worker wait time and other factors can also be statistically quantified and displayed with graphs to identify different production yields and operating rates, enabling lines to be designed and upgraded with efficiency.