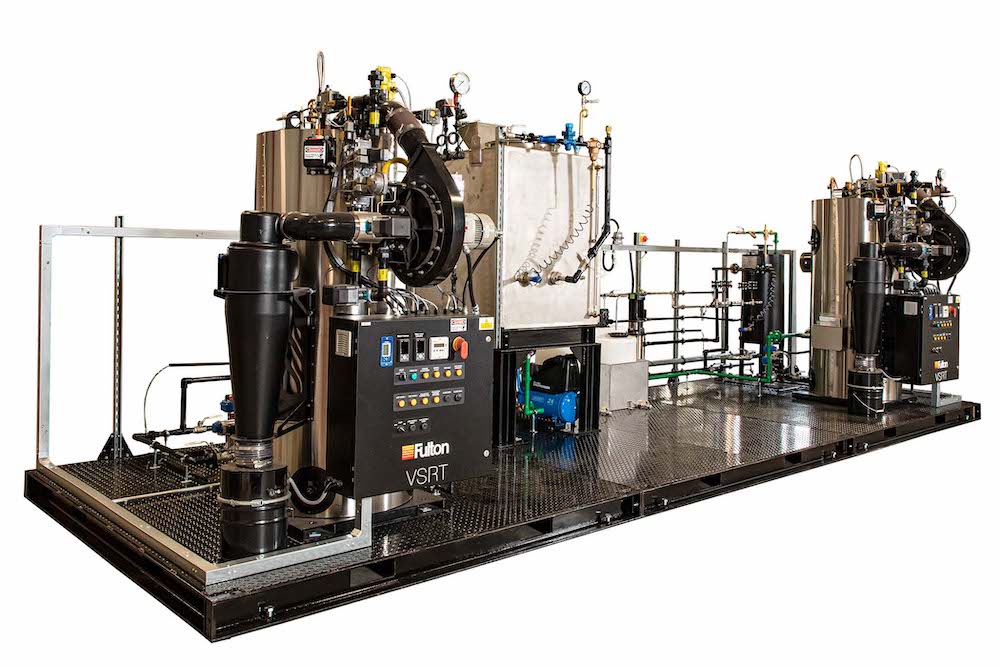
With the withdrawal of fuel duty due in April, many businesses operating steam boilers have been considering the alternatives to red diesel / fuel oil.
A point of interest that Fulton has noted recently is that some fuel suppliers have acknowledged that a high percentage of light oil fuels tested on site (approximately 80% of samples) are contaminated in one form or another. Contaminants in fuel can include particulate matter and water that can affect the flow of oil and cause waxing and corrosion, which can lead to boiler lockout, incomplete combustion and/or wear on components and corrosion of fittings and pipework, all of which affects a boiler’s efficiency.
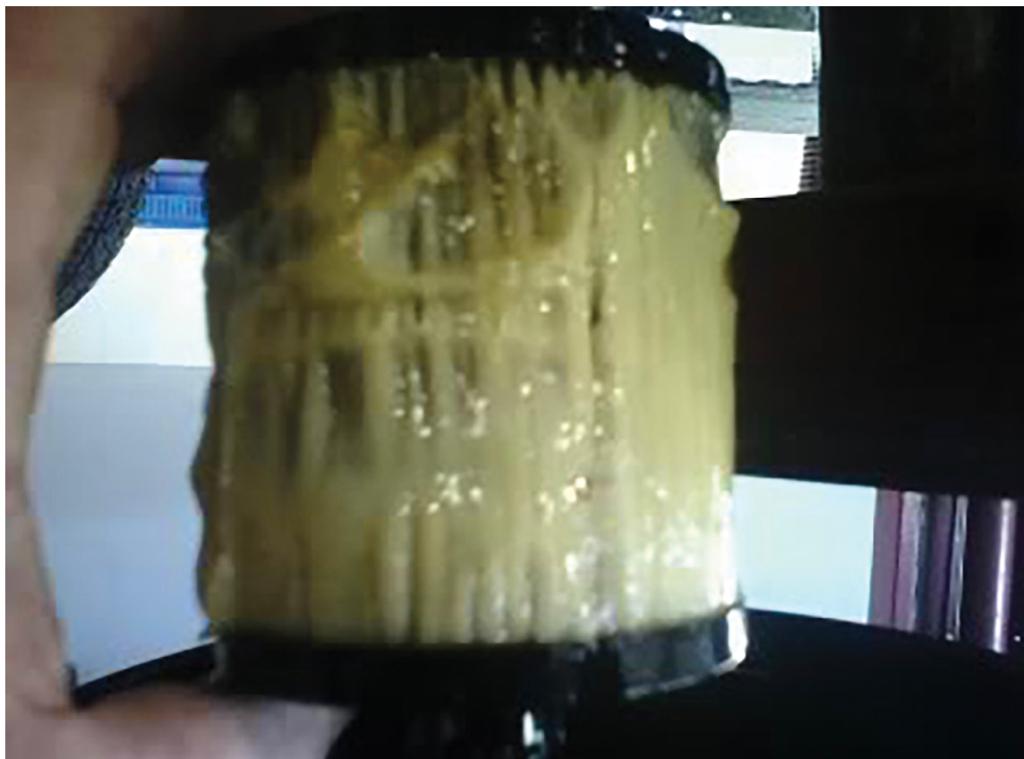
This is why with the company’s current range of steam boilers, including the award-winning VSRT, liquid petroleum or natural gases are considered the optimum and most stable and efficient methods of firing a steam boiler because they avoid the use of potentially contaminated fuel oils, or the requirement for costly fuel polishing to remove moisture and debris from contaminated oil installations.
However, it is understood that moving from oil to liquid gas can be cost and even geographically prohibitive, so steps should be taken to ensure that fuel oils remain stable. These include regular checks for moisture and particulate matter in the fuel and tanks; and ensuring the steam boiler itself is regularly maintained and serviced according to manufacturer’s guidelines, which should include valve inspections and oil filter changes.
For those where cost and geography do not pose an issue, moving to a cleaner fuel (such as liquid gas from Flogas) and one that is easier to manage does come with huge benefits to businesses operating steam boilers. For example, following a site survey and steam load distribution analysis by Fulton and Weishaupt at a brewery in the South West of England in 2020, the two companies identified opportunities to reduce carbon emissions at the site and save money on fuel by upgrading the burner on a Fulton RBC2500 horizontal steam boiler that was installed in 2007.

The boiler was originally fitted with a high/low, conventional control box oil-fired burner, which was achieving a turndown ratio of less than 2:1. Partnering with Weishaupt, a micro-modulating LPG burner with integrated digital burner management system – air and gas servo motors accurate to within 0.1° – was specified and installed, with Fulton also specifying optional burner motor variable speed drive to reduce electrical power consumption and oxygen trim to maximise combustion efficiency. Additionally, with NOx levels reduced as a result of the upgrade, the RBC2500 is now also fully MCPD compliant.
Commenting for Fulton, Leigh Bryan says: “The result of the partnership between Fulton and Weishaupt, with Flogas also involved as the liquid gas supplier, is an upgraded steam boiler with turndown improved to at least 7:1 which, combined with the added burner options, is predicted to save the brewery in excess of 20% in fuel consumption alone. Impressive reductions in carbon emissions by changing to a cleaner, lower-carbon fuel like liquid gas will also be achieved and add to the efficiency savings.
“The cost savings predicted for the upgrade project at the brewery are expected to deliver a payback period of less than 12 months and will go a long way in assisting the company’s impressive Road to Net Zero efforts.”
www.fulton.co.uk | sales@fulton.co.uk | t: 0117 972 3322