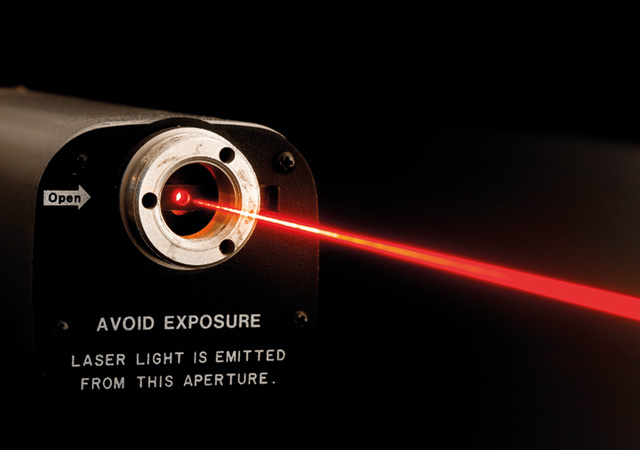
Laser safety demands a holistic approach to the safe design, use and implementation of laser technology to minimise the risk of accidental exposure to laser radiation, says TLM Laser Director Andy Toms, who outlines the various laser types, classifications, and standards.
One thing that everyone is generally aware of is that laser light is hazardous. The extent of any potential danger is directly influenced by the type and power of the laser. Laser power varies from just a few watts for simple marking applications right through to lasers which have kW levels of power and are used to cut or weld steel components.
Lasers also use different wavelengths to allow them to process the many different materials they encounter within a manufacturing environment.
The greatest potential danger comes from lasers with moderate to high power levels as they are capable of burning the retina of the eye and perhaps even skin. Lasers are therefore classified by power and wavelength to provide a greater understanding of the measures required to ensure safe operation.
British Standard BS EN 60825-1 sets out the different laser classifications. Class 1 lasers are considered to be safe during normal operation with the levels of risk and potential danger increasing through Class 1M, Class 2, Class 2M, Class 3R, Class 3B up to Class 4 – which is deemed hazardous, even if diffused reflection is viewed without suitable eye protection.
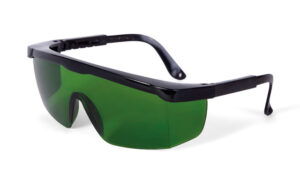
Focus On Safe Operation
The safest option in any instance is to select the lowest class of laser and the lowest power level required for your application. A risk assessment should always be undertaken to review procedures for laser set-up, alignment, normal operation and, of course, how maintenance and repair tasks will be carried out.
Topics for consideration during a risk assessment should include: safety interlocks and key switches, use of laser safety glass in windows, shutters or filters on the laser aperture, personal protective equipment, set up procedures and hazard warning signs.
It is also essential that users select the correct laser safety glasses or goggles for the laser type and wavelength being used. Just as laser sources are classified, laser safety eyewear must also adhere to a range of classifications and certifications. EN207 certification ensures that safety eyewear meets the laser protection requirement of the European Personal Protection Equipment (PPE) Directive.
Specific information, printed on the eyewear, provides a means of identifying that the correct eyewear is being used to protect the user when operating a specific laser machine.
Keeping The Air Clean
A topic which is remarkably often overlooked is that of fume extraction. Lasers generate a variety of toxic fumes and particulates when different substrates are being processed. These contaminates are known within the industry as LGAC’s (Laser Generated Air Contaminates).
LGAC’s of different make-up can react in the extreme within the filtration process. It is essential therefore that users take advice from the laser manufacturer or supplier on the most appropriate extraction system for their specific application.
Bromsgrove based TLM Laser are UK and Ireland distributors for a comprehensive range of laser based technologies and systems including safety eyewear and also laser safety enclosures and chambers. Manufactured on site from modular material, TLM’s enclosures are constructed to confirm to all relevant standards, interlocks and e-stops, etc.
These are generally used for class 4 lasers cleaning or welding operations where the operator is required to be within the room. TLM Laser can also certify the ventilation and extraction within the rooms providing a complete and holistic approach to all aspects of laser processing.
www.tlm-laser.com | sales@tlm-laser.com |
t: +44(0) 01527 959 099