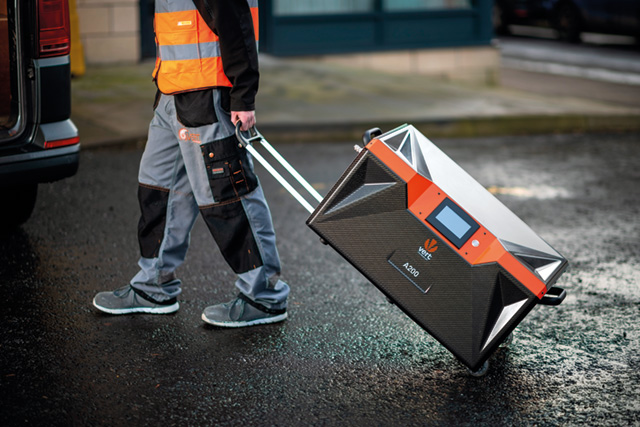
The idea of doing things differently in a post-COVID world could inspire more innovative approaches to areas of a site such as centralised plant utility systems, argues Nicol Low, Chief Operations Officer at Vert Technologies. Here he explores how the use of secondary compressors can deliver a step change in flexibility, efficiency and productivity for owners and operators.
Old orthodoxies about how we work have been challenged since the Covid-19 pandemic hit the world, including in the manufacturing and processing industries where new thinking around the use of previously fixed and static systems has emerged. The provision of utilities such as compressed air – which can be used for cooling, cleaning, and operating necessary pneumatic tools – is a key example of where more innovative approaches can be adopted.
Though this utility is usually supplied through a large, centralised system, more agile working may see employees perform duties out-of-hours. Consequently, either leaving the primary system ‘always on’, or powering up factory-wide installations out of hours, may be inefficient, especially if only one or two machines are being operated. Indeed, this overuse could conceivably lead to system degradation, reducing performance.
Consequently, it is vital that facilities managers put in place a comprehensive maintenance strategy to ensure these crucial units are kept in good working order. This need has been amplified by the pandemic, with compressors left inactive for longer due to COVID more likely to suffer expensive, unplanned disruption.
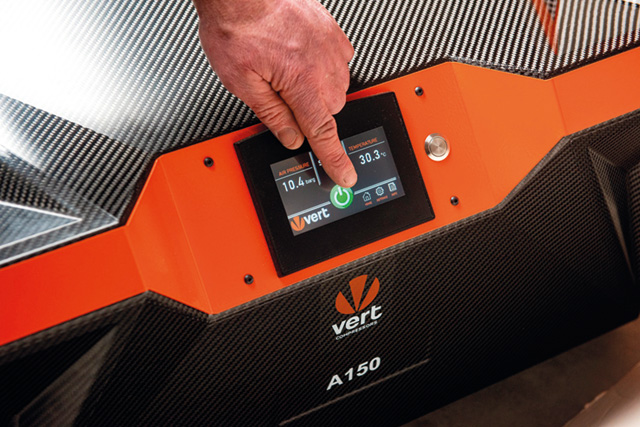
working is required
Secondary compressors
One aspect of this strategy is to use secondary compressor systems to power machinery locally out-of-hours. However, plant operators have traditionally been reluctant to implement secondary compressor systems due to the work required to reconfigure the factory floor.
Portable compressors can offer an alternative way of working, but the duty cycles of the traditional models used have always raised concerns. This specifically refers to the amount of time a portable unit can run at full load before it needs to be switched off, to avoid overheating and to cool down to enable it to compress air again.
For example, during an hour of operation under standard conditions, a compressor which has a duty cycle of 25% would only be able to run for five minutes on full load before needing 15 minutes downtime. However, in an environment such as a manufacturing plant this disruption has often been considered unacceptable.
Worse still, some facilities managers who are unfamiliar with low duty cycle compressors have been known to use them continuously, resulting in premature wear and tear and eventually compressor failure. Not only does this lead to additional costs of replacing the unit, but it places further pressure on the primary system until the portable unit is either fixed or replaced.
CRC technology
One innovation that could solve this performance issue while operating at safe noise levels – another key consideration – is the Conical Rotary Compressor (CRC) technology from Vert Technologies. Consisting of one rotor placed inside the other with both turning in the same direction to compress air as it travels down the conical screw, the CRC can deliver a continuous source of air on a 100% duty cycle.
Crucially, unlike twin screw compressors that lose efficiency when used in sub-3kW systems, the CRC can be scaled down without performance loss into models such as the highly portable Vert A200 compressor, which can be quickly and easily moved around the factory to the point of use. The low noise and vibration from the compressor also ensure those working in close proximity are not disturbed, and workers do not require costly noise protection measures.
In conclusion, to ensure that a plant’s primary compressed air system avoids issues leakages and pressure drops, it is crucial that facility managers include high-performing secondary units as part of an overall maintenance strategy. By prioritising duty cycles and entertaining the possibilities of new technologies beyond traditional units, costly, downtime-related pitfalls can be avoided.
www.vertrotors.com/vert-technologies |
engineering@vertrotors.com | t: +44 (0) 131 664 3600