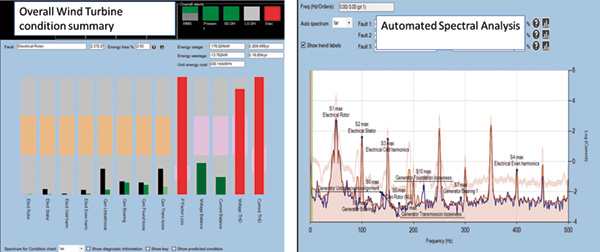
The problem solving skills and capabilities developed by industries that are routinely subject to new challenges can be applied just as well to meeting the challenges of climate change, says Faraday Predictive Operations Director Geoff Walker.
The problem solving skills and capabilities developed by industries that are routinely subject to new challenges can be applied just as well to meeting the challenges of climate change, says Faraday Predictive Operations Director Geoff Walker.
The move to Net Zero Carbon brings some new challenges, which require new solutions. Every day, conventional industries are accustomed to facing and dealing with challenges, and the problem-solving skills and capabilities developed can be applied equally to the new challenges of climate change.
In addition, some of the new technology being deployed in the Wind and Nuclear industries can be applied in conventional industries and bring additional opportunities to benefit in your own patch.
So what will Net Zero mean for my industry – and what can I do as an individual?
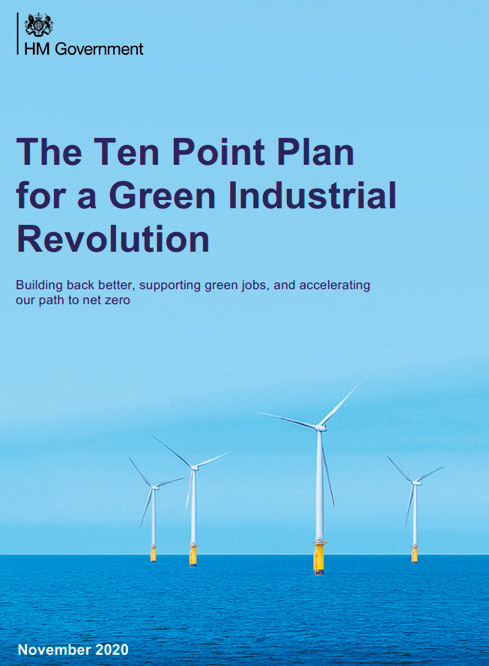
The UK Government’s “Ten Point Plan for a Green Industrial Revolution” emphasises the importance of Wind Power, and new Nuclear power, including Small Modular Reactors, as well as the use of Green Hydrogen.
These new technologies are already developing apace, creating development opportunities in many areas, not least of which are optimising Operations and Maintenance to maximise the benefits from these new green investments.
Faraday Predictive have been applying their advanced technology for Condition Monitoring, Energy Monitoring and Energy Waste Reduction in both Nuclear and Wind. The challenges of these new environments has led to enhancements of their systems, that can now be applied back into conventional industries.
Faraday Predictive systems monitor the condition of the entire machine in one go, covering motor, transmission and driven equipment, and spanning electrical, mechanical and operational faults all from one simple connection into the electrical supply to the motor, inside the motor starter cabinet.
Sophisticated algorithms analyse subtle changes in the relationship between voltage and current which indicate around 40 different specific faults, including bearing problems, unbalance, misalignment, rubbing, loose foundations, as well as electrical power quality problems. Predictions of machine condition are provided up to three months ahead. Alerts, diagnoses and advice can be viewed on local PC screens or any web-enabled device.
The technology can be thought of as a form of Vibration Monitoring that uses the mainly torsional signals that affect the motor current. But unlike conventional Vibration Monitoring, because Faraday Predictive systems measure voltage and current, they also measure energy consumption and automatically calculate how much each machine is costing you to run each year.
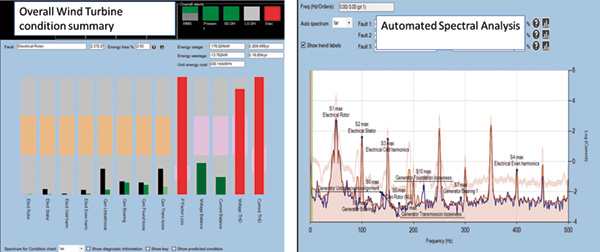
And even more interestingly in our striving towards net Zero, they identify the amount of energy being wasted by machine faults, allowing you to cost-justify precision maintenance to eliminate the fault.
Faraday Predictive systems have proven to be effective in areas where other techniques such as conventional Vibration Monitoring have struggled. In Wind Turbines, the varying strength of the wind and the resulting variability of speed and vibration signals can make it difficult to get meaningful results.
The Faraday Predictive system has been tuned to work well in this challenging environment, giving good quality results – with outputs like those seen in the diagrams here, showing an overall condition summary, and a detailed spectral analysis. And a major advantage of this sort of system in a wind turbine is that the installation can be done on the outgoing cables, connecting at the base of the tower, with no need to ascend to the top of the tower to fit sensors, with all the Working at Height restrictions that would bring.
One single system provides information on the condition and efficiency across the entire machine – including turbine, gearbox, generator and power converter. Additional sensors can provide information on pitch and yaw systems.
Since being refined in these challenging environments, this same technology is also available for monitoring your own factory machinery – pumps, fans, compressors etc. So you can see how much energy your machines are using, and more significantly, how much they are wasting, and what you can do to reduce the level of waste, while also enjoying the benefits of predictive maintenance. Now that sounds like a simple step we can all take to help the future of the planet.
www.faradaypredictive.com | info@faradaypredictive.com |
t: 0333 772 0748