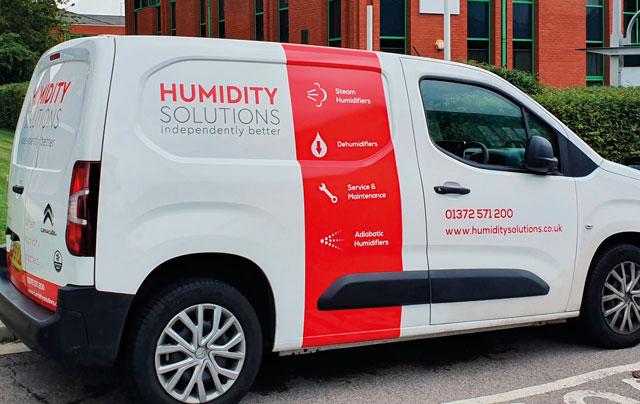
As summer draws to a close, now is the time to do some general checks on humidity control equipment to ensure it is in good working order and any spare parts are in stock. For most environments, controlling relative humidity within 40-60% will improve both mechanical and human performance and wellbeing.
By setting up a Planned Maintenance contract, factory or facilities managers can have peace of mind that equipment will be regularly serviced and maintained, ensuring consistent performance and pre-empting breakdowns due to out of date or faulty parts. Providing stable and consistent conditions for modern manufacturing production systems, human comfort and staff wellbeing, means that production speeds are maximised and downtime minimised, helping you deliver increased productivity and profit.
Of particular focus are the potentially harmful hygiene implications from build-up of bacteria if equipment is not regularly serviced and maintained, and which is also likely to lead to increased costs down the line when having to work reactively to correct faults or outbreaks.
Planned Maintenance is a cost-effective way of keeping equipment working at its optimum throughout its life, reducing workload and worry for site managers.
www.humiditysolutions.co.uk | 01372 571200