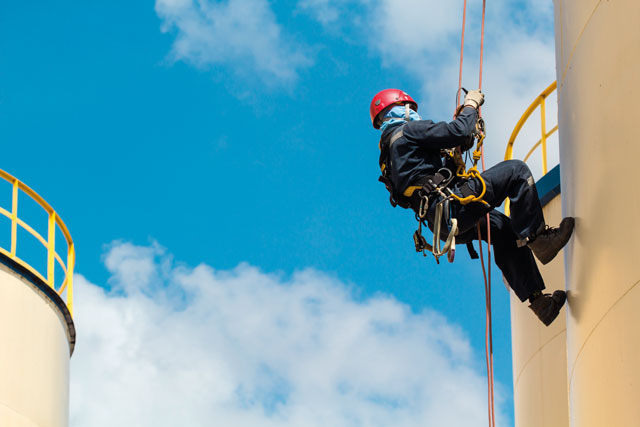
Penny Hydraulics’ Health and Safety Officer, Compliance Manager Peter Hill, looks at some of the most important actions businesses can do to keep workers safe when operating at height.
Working at height is an everyday occurrence for workers across a host of industries, but understanding how to keep team members safe requires the guidance of a health and safety expert.
Lifting equipment manufacturer, Penny Hydraulics, produces specialist products to support working at height for the end user, and they know more than most how important it is to put a health and safety figurehead in place to ensure regulations are followed by all team members on a day-to-day basis.
Employing a Health and Safety Officer in the workplace can cut down accidents by as much as 50%, and by having a staff member dedicated to this role, incidents are less likely to occur and employees can seek advice when taking on jobs with risk attached to them.
1. Get accredited
Penny Hydraulics appointed a Compliance Manager to ensure the company was operating in accordance with the latest requirements and this led to the International Occupational Health and Safety standard ISO 45001 being awarded. Businesses will benefit from seeking to gain accreditation and learning how they can improve, which is only of benefit to their team’s safety and their industry reputation.
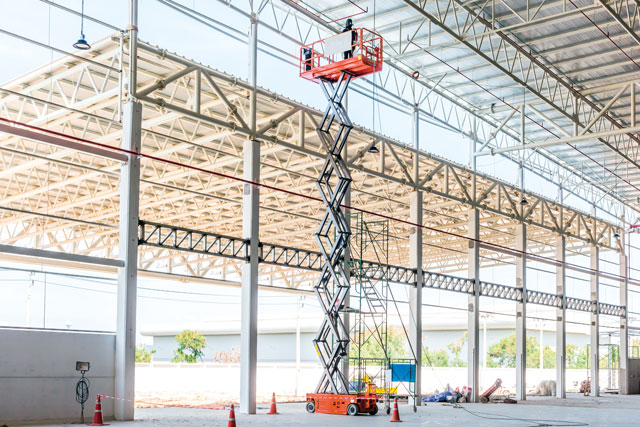
2. Regularly maintain equipment
It goes without saying that regular maintenance of equipment will improve its longevity and performance, which will keep trained team members safe when using it. If businesses are unsure on how to maintain their equipment, they should refer to any user manuals or seek advice from the manufacturer directly and even ask for refresher training if required.
It’s worth noting that if you have any doubts over the integrity of a piece of equipment – even just the smallest hunch – don’t take any risks and seek advice immediately. Penny Hydraulics offers support on the products it sells to customers and you should ensure the equipment you purchase comes with an extra layer of aftercare.
3. Offer continual training
The Work at Height Regulations 2005 was put in place to ‘prevent death and injury caused by a fall from height’ and team members should be regularly reminded of their roles and responsibilities in the workplace.
It is important that new and existing team members receive regular training, so they don’t take risks and know when to ask for help to ensure safety in the workplace. The same applies for onboarding new equipment – everybody working on it should be well versed on how it works and be supervised until they are ready to operate it alone.
4. Provide personal protective equipment (PPE)
Employees should be able to access good quality PPE – such as face coverings, goggles, gloves and footwear – to help them do their job safely. Personal protective equipment should be regularly reviewed and, if necessary, replaced, to ensure it continues to offer the best level of protection possible.
It’s crucial that all clothing is compatible with each other and doesn’t obstruct its function. For instance, workwear should be comfortable and not snag on any harnesses or connectors when working at height.
5. Keep a detailed incidents log
Although businesses would rather have no incidents to report on, recording and learning from them is a good way to prevent any further harm to employees. A detailed incidents log should explain who and what was affected in any given incident so either training or repairs can be administered to ensure workers are safe in the future.
The contents of this article are the personal views of Penny Hydraulics.
Always seek professional advice.