Plant operators looking to drive down emissions are often hit with some very expensive solutions to PCDB compliance, but EOGB Technical Manager Reece Summerfield explains why retrofitting Flue Gas Recirculation can be a relatively low cost, effective solution.
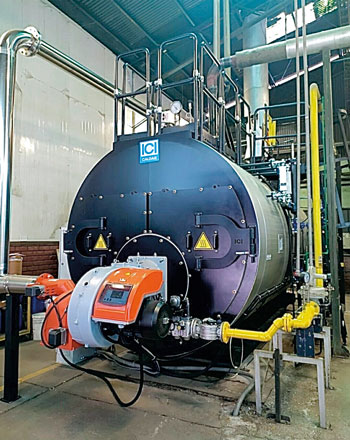
During high temperature combustion, oxygen (O2) and nitrogen (N2) present in the air can combine with each other in several ways, generating nitrogen oxides NOx, responsible for many pollution phenomena, such as acid rain and ground level ozone formation in the lower atmosphere, with known consequences on health.
There are three main reasons for the formation of NOx:
• Thermal NOx – Related to flame temperature
• Prompt NOx – Related to chemical reactions
• NOx due to fuel – Related to the amount of nitrogen in the fuel
When it comes to emissions, the main problem is to maintain the stability of operation, having very low emissions generally involves very accurate management of the combustion, with limited possibility in variation of the parameters that govern it.
So, what’s the most effective way we can reduce NOx within the commercial and industrial sectors?
Flue Gas Recirculation is a technique to recirculate the external combustion products, withdrawing part of the products of combustion from the flue stack and dilute them with combustion air. This technique allows to reduce the flame temperature, reduce the concentration of oxygen and increase the concentration of inerts (N2 and CO2), which in turn will absorb a part of the energy developed during combustion.
Forced draft burners are the simplest method, the fume flow rate adjustment is performed by using a servo-controlled throttle valve, managed by the electronic equipment of the burner which is set upon commissioning.
Several plant solutions can be used for separated burners:
1. External recirculation on the main fan intake with adjustment of fume flow rate through a damper positioned on the recirculation duct.
2. External recirculation through an auxiliary fan with fume release downstream of the main fan and adjustment of fume flow rate through the damper, or through an inverter installed on the auxiliary fan. It is also possible to design the burner combustion head so that fumes are directly released in the combustion chamber.
3. External recirculation through an auxiliary fan with fume release on the burner sleeve and adjustment of fume flow rate through the damper, or through an inverter installed on the auxiliary fan.
What makes this even more feasible is the fact FGR can be retro fitted on existing applications so doesn’t warrant completely new plant equipment. Advice would need to be taken from the burner manufacture on the suitability of the existing burners and site surveys can be provided free of charge.
www.eogb.co.uk | reece.summerfield@eogb.co.uk | t: 01480 477066