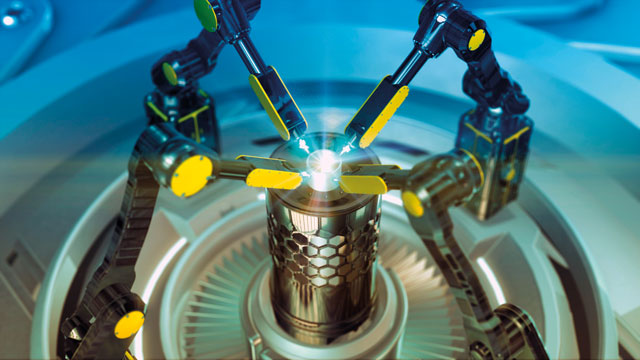
ABSTRACT
As the volume of data generation is increasing at an exponential pace, factories today are struggling to make real use of the incredibly important insights hidden in data. With the arrival of 5G, hybrid cloud and powerful asset management solutions, now that became simpler. IBM is working in the UK’s prestigious ‘5G Factories of the Future’ project to define the new paradigm for how the future factories will operate, how connected assets will improve operational agility and make the supply chain smarter. This article explains top five use cases that are core deliverables of the project, technology behind those and how these will transform the manufacturing industry in the future.
Introduction
Efficiency, productivity, and sustainability are vital considerations in the manufacturing industry. And, as we look to the Factory of the Future, manufacturers are integrating new technologies, including the Internet of things (IoT), cloud computing and analytics, and AI and machine learning into their production facilities and throughout their operations.
These changes will revolutionize the way that companies manufacture, improve, and distribute their products.
Consider for a moment the amount of data on a single factory floor – from the sensors that track heat and occupancy to the cameras collecting visual data and monitoring workplace safety.
Then, expand that across a larger organisation with several different kinds of facilities and the demand for data processing grows exponentially and the artificial intelligence (AI) models needed to sort through this data get significantly more complex. With extra data sorting comes the issue of time: an AI model that can tell you a month from now that employees are crowding in a passageway isn’t particularly useful.
Today, different technologies are being used to solve these issues, such as Edge Computing for making decisions on the manufacturing floor, connectivity technologies such as 4G, or existing plant networking technologies.
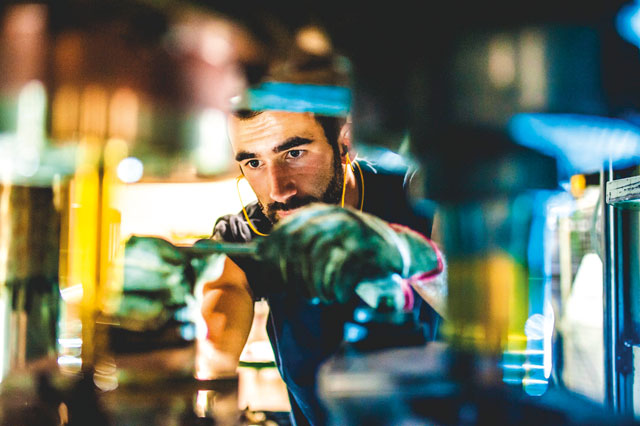
However, they can often be cumbersome to retrofit into a factory and can be challenged by IT departments or security teams. Additionally, many companies today also struggle to justify investments in Industry 4.0 technologies and find business cases hard to develop.
So unsurprisingly, another approach that is gaining a lot of attention is 5G. Much has already been written about how 5G will help, how it will transform manufacturing, increase efficiency and productivity.
5G may still feel a long way off but it does offer something different by providing increased bandwidth, increased connectivity in terms of the numbers of devices, reduced latency, and in-built security. In addition, it offers the possibility of deploying a private network – which in a manufacturing facility eases the implementation headaches associated with retrofitting a physical network.
Reduced latency will allow real-time remote control of manufacturing systems while increased bandwidth will allow line side support through augmented and virtual reality devices. In short, the potential of Industry 4.0 for a ‘smart shop floor’ at scale starts to become a reality.
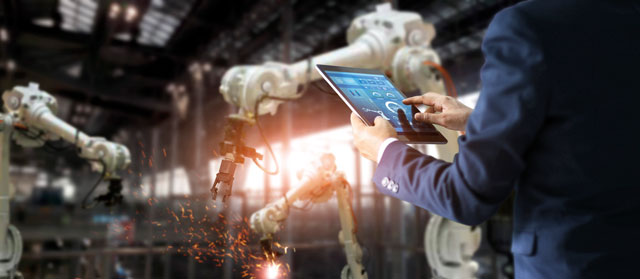
To help test how 5G can help in manufacturing, IBM is working with several partners to develop 5G testbeds across the world to help prove practical use cases and ease its adoption. One such example, here in the UK, is the 5G Factory of the Future programme, an open access two-year project aiming to demystify 5G for the manufacturing sector and work towards developing the smart factory of the future.
5G Factory of the Future
The project is primarily based at the University of Sheffield Advanced Manufacturing Research Centre’s new site in Samlesbury; with a significant additional footprint in both BAE Wharton and AMRC’s site in Sheffield.
It brings together industrial and academic leaders from the manufacturing and telecommunications sectors to establish a 5G manufacturing testbed. It is the largest of all the investments made by the UK Government Department of Culture, Media, and Sport as part of its £200m 5G Testbed and Trials programme.
5G Factory of the Future is being led by AMRC North West and includes BAE Systems; IBM; telecoms and private 5G network provider, aql; along with Burnley-based MTT, an SME developer of digitalisation technologies for machine tools; and the Lancashire-based data-driven logistics specialist, Miralis. Digital Catapult is the technical authority lead and is coordinating 5G integration, working closely with aql and use-case developers, and developing the ecosystem of partners required to deliver end-to-end industrial 5G solutions.
Use cases designed to deliver
There are five key use cases that will be investigated in the programme:
• Real-time Monitoring and Adaptive Closed- Loop Control (RTM)
• Digital Twin Track and Trace (DTT)
• Factory Ecosystem Monitoring (FEM)
• Chain of Custody System (CCS)
• Distributed and Shared Hybrid Reality Spaces (HRS)
The first that we are looking at is real-time process monitoring and control. By using the ultra-low latency of the 5G network we can start to process even more information from factory floor operations into remote AI models (both in a separate on-premise facility and on cloud) to improve process precision and predictive maintenance solutions.
One of the key aims here is to demonstrate a 15-25% reduction in the number of defects, amount of waste generated and machine downtime arising from improved process precision and predictive maintenance strategies and error reduction.
The second use case is focused on digital twins – the virtual representation of a physical asset. We’re investigating how they can be used for tracking the performance and health of manufacturing assets given the increased number of sensors we can connect over a 5G network.
We’re aiming to see 15-20% machine utilisation improvement (reduction in idle time, improved scheduling) and general improvements in factory efficiency. They can arise from data-driven decision-making, real-time asset location, efficient machine scheduling, asset performance optimisation or improved predictive maintenance.
The next use case will examine how environmental information such as temperate, humidity, vibration and energy can be combined with real-time asset data to improve machine utilisation, and a reduction in both energy usage and maintenance time.
The fourth use case looks at how we track assets across different manufacturing and production sites through the supply chain. This aims to increase asset visibility to improve schedule accuracy and generate a 30% decrease in lost or damaged assets. Again, 5G enables us to connect a lot of sensors and ingest in real-time, something that is difficult to achieve currently.
The final use case is focused on augmented and virtual reality technologies and uses the ultra-low latency, high bandwidth capabilities in 5G to enable mixed realities across multiple sites. For example, if an engineer is in one site can he collaborate across another site to provide support for maintenance or training. This could see a reduction in downtime on the plant floor.
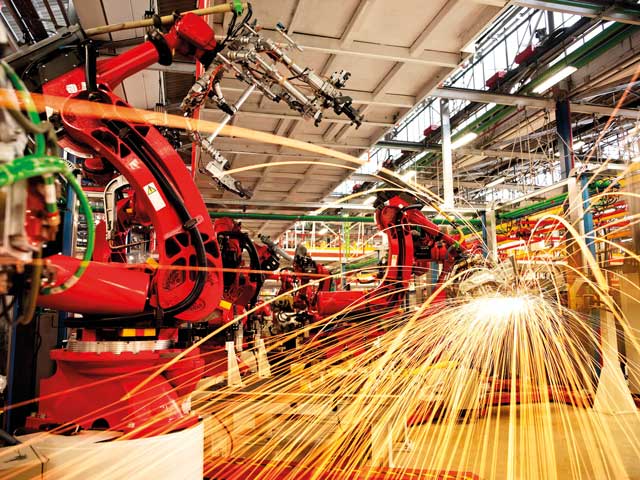
The role of technology
The programme uses an IBM IT backbone which is deployed both on-premise at each of the sites and with an identical environment deployed on IBM Cloud to facilitate data aggregation.
A variety of other IBM technologies are deployed which allow us to integrate the IT systems and sensors together and consume the data on a platform where we can organise and analyse it in a variety of ways – and which allows engineers and specialists across the consortium to collaborate on the use cases.
IBM Maximo Application Suite is at the centre of monitoring, managing, and maintaining the factory assets. It provides transparent visibility of assets across their lifecycles. There are numerous indicators that can signal slow and steady deterioration of asset health long before the often-invisible asset performance impacts production continuity or product quality.
A powerful asset management tool is thereby extremely important to translate the data driven predictive analytics into actionable work items.
Maximo’s ISO 14224 aligned process automation capability does that translation. It helps automatically generate executable work orders with corrective maintenance tasks, required spares, and suggests recommended safety gears.
Such automation on top of the predictive capabilities helps factory managers take the most optimised decisions to improve operational efficiency, reduce cost and enhance health, safety, and environmental compliance. Not only that, but advance visibility of the maintenance needs helps also plan for the required production stoppage by choosing the right operating windows when the impact is minimum.
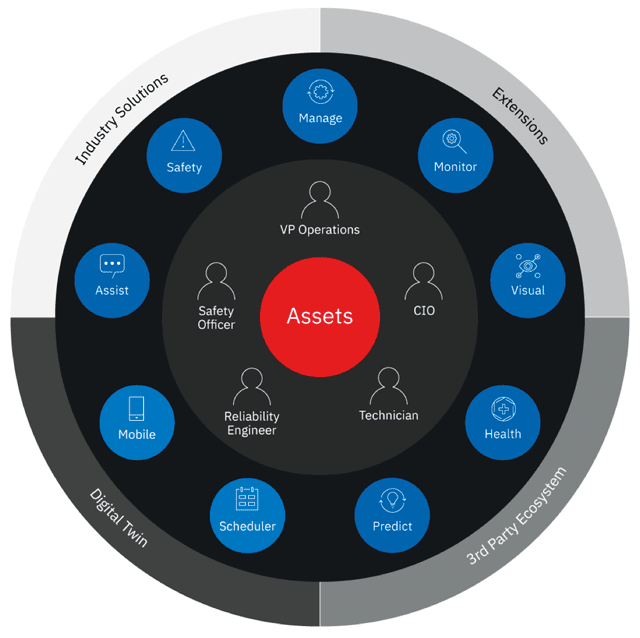
One example being the Maximo Application Suite which is used to manage the remote assets and explore how Visual Inspection can operate over a 5G network.
While AI technologies such as visual inspection are not necessarily new in manufacturing, 5G can change the way we approach it. Cameras arrayed throughout a factory floor could gather image data which a model uses to scan for problems, so that inspectors spend more time going where they’re needed.
In industries like apparel manufacturing, visual inspection can be used for such precise tasks as spotting flaws in stitching or fabric. In automotive manufacturing, it can spot paint chips, part defects, or even safety flaws.
In all these scenarios, 5G would provide access to more images, in higher resolution and as such it could help reduce overall costs, both by preventing defective products from getting to market and streamlining the processes for maintenance and repairs of critical equipment.
However, as sensor and camera deployments grow in scale and sophistication, a key challenge is identifying ways to combine all the visual and sensor data in a way that makes sense and can be analysed. A large manufacturer might have millions of inputs at a given moment.
Without tools that are powerful enough to help humans analyse it, all that data easily becomes overwhelming, meaning the potential insights within that data are ignored or worse, misunderstood.
So, while collecting the data is one important aspect, the project is looking at how to maximise the value of that data, particularly in how manufacturers can make real-time remote-control decisions. To do that, we’re using IBM Cloud Pak for Data.
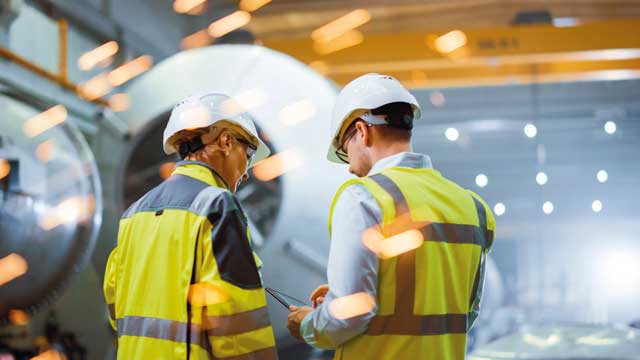
The Hybrid Cloud Advantage
While AI and Internet of Things (IoT) are two of the key building blocks and are integral to large-scale industrial automation, to achieve this at scale requires a third building block: Hybrid Cloud.
Manufacturers have been reluctant to move operational data to the cloud, but at the same time have wanted to exploit the benefits of AI and advanced analytics.
Hybrid Cloud allows manufacturers to do just that, keeping the confidential operational data on premise at the manufacturing site, while sharing fewer sensitive data in a private cloud environment where it can be used to facilitate collaboration across multiple production facilities, help improve AI models, or for advanced reporting.
For this reason, the IT backbone has RedHat OpenShift at its core.
A lesson learnt
One interesting aspect to the project is that it has been worked on primarily during Covid lockdowns. From the initial definition, through the project submission, award and now in delivery, the team have worked remotely throughout.
Bringing together a consortium remotely is not without its challenges but using online tools and an adaptable approach from all the parties, we have been able to collaborate and work effectively and still maintain the project timelines.
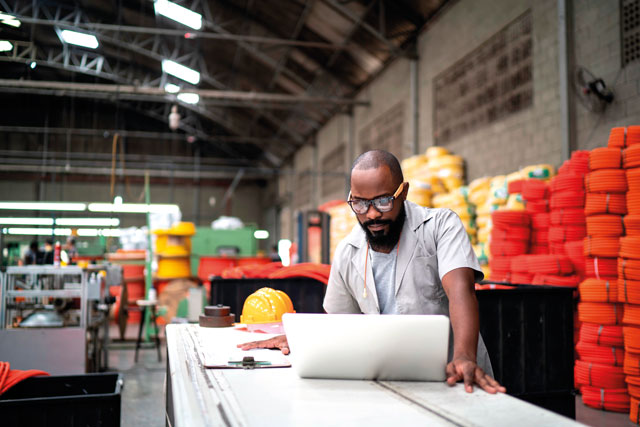
What’s next
With the private 5G network now live, we’re feeding data from the different sites into the platform and beginning to ingest even more – in terms of both quantity and variety of data types – into the platform. This is a key step to enable us to start to benchmark the performance characteristics of the overall solution. The need for industry collaboration has never been clearer, with specialists coming together to demonstrate the benefits of 5G in digital manufacturing.
With the impact of the pandemic and Brexit, combined with often low productivity rates found in the UK manufacturing sector, the need to innovate to remain competitive has never been greater. This programme is a key step in helping us understand how 5G can help play a part in developing a sustainable and smart Industry 4.0 vision in the UK.
Next generation factory assets are also going to be more sophisticated and thereby costlier. They need an AI-enabled enterprise asset management (EAM) solution that is easy to use and provides enterprise scale execution for maintenance, operations, and reliability teams.
IBM’s Maximo Application Suite provides remote asset monitoring, maintenance and reliability applications in a single platform that enables factory owners to increase uptime, improve productivity, reduce maintenance costs, and build more resilient operations.
Application of advanced robotics is increasing in smart factories. Robots are being used to augment human inspectors by spotting defects in areas that are difficult and risky to approach. Inbuilt data analytics capabilities area helping fast transfer of insights to the decision makers to take quick actions.
As the modern factory assets are digitally connected, besides maintaining their physical links, it is now feasible to improve performance of the connected asset system instead of a single asset.
Insights from intelligent, connected assets and untapped data sources are critical to understanding the preventive, predictive and prescriptive actions needed to drive efficiency, reduce operating costs, and consistently meet quality targets.
Increased predictability of asset performance will enhance certainty of production planning. Improved accuracy of the production planning will drive future factories to optimise raw material and MRO materials and services demand and finished product supply to the market more accurately.
As a result, smarter factories of the future will lead huge supply chain efficiency gain in the ecosystem of partners.
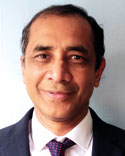
Debajyoti Chakraborty
Associate Partner, IBM Global
Business Services
deb.chakraborty@uk.ibm.com
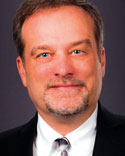
Skip Snyder
Senior Partner and Global
Intelligent Connected
Operations Leader
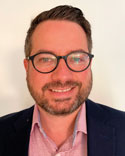
Euan Pirie
Industry Business Development
Technical Leader