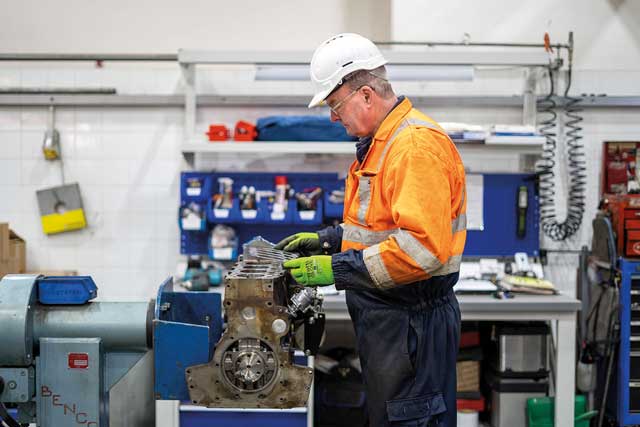
Keith Brown, Technical Manager at DiPerk Power Solutions, explores some of the challenges when producing Stage V-compliant machinery, and how businesses can streamline their journey to compliance.
The introduction of Stage V emissions legislation was designed to tighten restrictions on non-road engines and equipment, lowering limits on particulate matter (PM) emissions for equipment ranging from 0 to 560 Kw (engines up to 19 Kw have used in-cylinder technology to meet their emissions limits). Stage V was introduced for engine ratings below 56 Kw and above 130 Kw in 2019 and for 56 Kw in 2020 — 130 Kw engine ratings also became subject to this legislation. OEMs were given until June 2021 to place transition engines — engines built before the Stage V introduction — onto the market.
The move from Stage IV to Stage V poses a real challenge because OEMs must now select an engine fitted with a diesel particulate filter (DPF) as well as a diesel oxidation catalyst (DOC) and a selective catalytic reduction (SCR) cannister (>56 Kw). This addition has in many instances increased the overall footprint of the engine assembly. Although manufacturers were granted extra time to prepare, many are still looking for guidance on redesigning their equipment, so they can continue to sell their products in the European market.
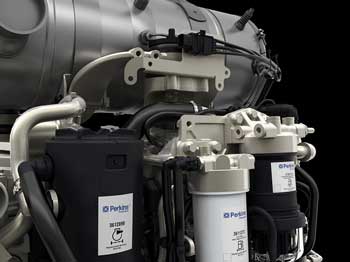
Adapting to aftertreatment
The key to Stage V compliance is integrating the engine and aftertreatment technology to equipment, be it a pump, genset, or combine harvester. In the electric power market, manufacturers of constant speed mobile generators will now have aftertreatment devices including selective catalytic reduction (SCR), diesel particulate filters (DPFs) and NOx reduction systems (NRS). The choice of aftertreatment combination is determined by the engine’s power rating: an engine rated 19-56 kVA will typically utilise a DOC and a DPF, but once the rating exceeds 56 kVA, SCR will also be needed to reduce NOx levels to Stage V requirements.
OEMs may need to redesign the engine and aftertreatment housing to accommodate aftertreatment devices. These can be mounted on or off engine, but this added space claim volume may require the manufacturer to modify an enclosure so it can be fitted correctly with the required air flow and clearances.
Getting started with Stage V
Stage V has introduced various new design considerations for OEMs. The first step to Stage V compliance is obtaining a model of the equipment’s engine and the necessary aftertreatment device(s) from the engine supplier. Using a CAD model, manufacturers can identify the space constraints caused by the integration of additional hardware. At this stage, the manufacturer can also establish if there are any clashes with the existing design caused by the electricals, exhaust or any other engine interface.
Engines with SCR technology may require a more powerful electronic control module (ECM) to drive the aftertreatment’s monitoring and controlling devices. SCR uses AdBlue to reduce NOx emissions — converting NOx into nitrogen and water vapour. The ECM controls the AdBlue pump, which primes the AdBlue dosing system and purges it back into the tank when the engine is turned off. Electrical power to the ECM is maintained until the process is complete, otherwise it can lead to crystallisation of the AdBlue within the system. OEMs can solve this issue by installing a permanent battery connection to the ECM — this requirement will be outlined in the engine manufacturer’s installation documentation.
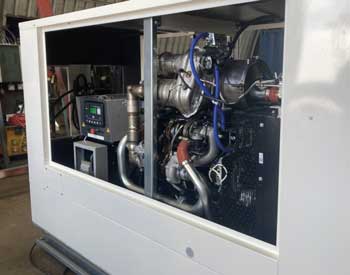
Larger engines fitted with an SCR system use NOx sensors to measure the difference in NOx levels between the engine outlet and SCR outlet. Some engines are designed for NOx sensors to be easily incorporated, although the manufacturer may need to find an off-engine location to house the electronic NOx sensor controllers.
By engaging with the engine supplier early on, OEMs can get a clear understanding of their machine’s design limitations and how their engine choice will affect emissions. A registered dealer will already have several years of experience working with different Stage V technologies and can also recommend the correct engine rating and emissions technology best suited to the application. Such collaboration will be key for helping industrial equipment OEMs as they prepare on their Stage V journey.
t: 0800 0730 424 | engines@diperk.co.uk | www.diperk.com