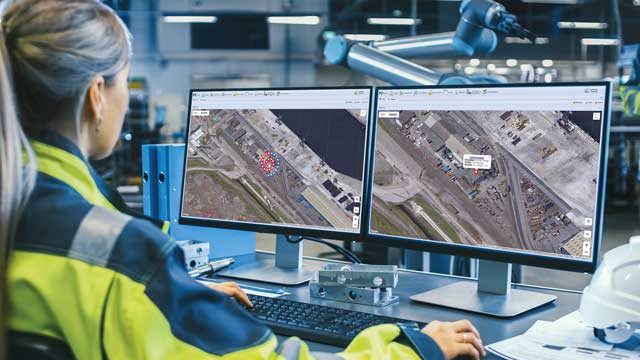
Computerised Maintenance Software Systems (CMMS) have been around for over 40 years, having evolved from a need to reduce equipment failure rates. Adrian Whyte, Operations Director of asset and maintenance management software specialist PEMAC, explains how the efficacy of each deployment and its benefits can vary.
Most CMMS projects focus on getting the preventative maintenance element up and running first. Identifying the equipment to be maintained, the intervals and the key value-added tasks that need to be performed to reduce equipment failures. The biggest mistake here is assuming that time-based maintenance is the correct approach. It is clearly the easiest method to use, but its efficacy is questionable, especially when you factor back in the varying demands put on equipment. Usage based maintenance is a much more effective strategy. Connecting a meter to your routine maintenance check allows the equipment usage to trigger a maintenance check, saving resource time, expensive spares, and productive capacity. Proving this, however, is a challenge.
One way to start this evaluation is to capture the unplanned work generated in the system and start generating a metric such as Mean Time Between Failure (MTBF) for the asset. By comparing this figure to the current maintenance interval against a machine, overmaintained and undermaintained interventions can be identified. It’s essentially a very simple way to create a feedback loop or learning outcome in your system.
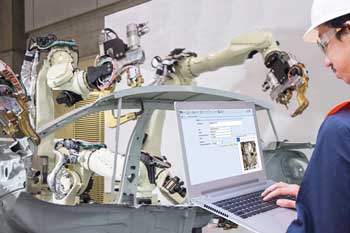
Once this is done, engineering can then decide how to capture those meter readings from the equipment. It can be done manually as part of a visual inspection route and captured on your maintenance app. Alternatively the meter data can be captured remotely through an interface. These interfaces have become much more commonplace and are often mentioned in conjunction with Industry 4.0 or the Internet of Things (IOT) initiatives. In software terms, if your CMMS includes an Application Program Interface (API) or more correctly a Published API, these interfaces become easier and hence cheaper. It’s a very small step then to start integrating critical and non-critical alarms into the CMMS, providing real-time data on machine performance and reducing the gap between reporting a problem and engineering reacting.
Over carrying of engineering spares is another common problem. This occurs most often when equipment failures are not fully captured in the CMMS. Without usage data for spare parts, it is nearly impossible to calculate demand and hence the appropriate stock levels. The alternative approach is to then carry large quantities of every conceivable spare but this is inefficient and expensive.
To maintain control of the spare part holding, the first step is to ensure that all unplanned work is recorded on the CMMS. When a spare part is issued to the asset, engineering can then calculate demand, getting a better understanding of the total cost of ownership (TCO) for the asset and reset reorder levels. This is the first step, but you are still left with an expensive problem, an investment trade off, carrying the spare and incurring the cost now versus taking a chance that you can get the spare quickly if required. Various strategies have been tried to help reduce lead times from consignment stock through to spares hubs.
One innovation is to use 3D scanning technology to create a virtual store, scanning certain spare parts and then making spares locally.
One of our clients started scanning shafts using a 3D scanner and then linking the scanned image to the appropriate spare in our PEMAC Assets system. When the spare is required, the drawing is issued to a local company via PEMAC. The turnaround time was lowered and the costs were on average a third of the Original Equipment Manufacturer (OEM) cost. In the first year the company achieved a return on investment of 850%.” To extend the benefit further the company started specifying the material to be used. This doubled the life of the spare, extending the maintenance interval and reducing costs further.
Software is one of those rare products. After you buy it, it continues to change. That change comes from interacting with people and organisations, solving problems and learning. It’s that shared learning that you really buy when you make your investment and then realising it becomes your key challenge.
07480 181 787 | sales@pemac.com