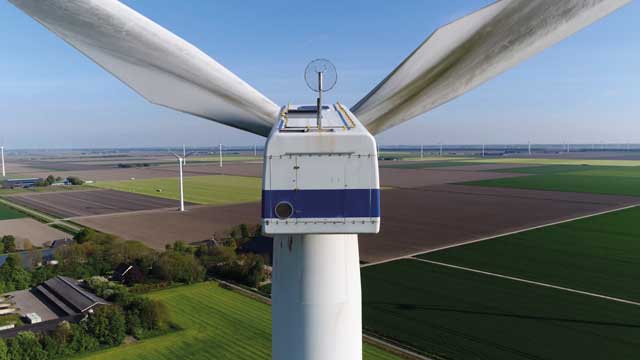
Awareness of the government’s net zero target and how industry should respond remains at a low level. The M&E Editorial Advisory Board discussed how levels of engagement could be raised. David Fowler reports
The government has committed the UK to cutting emissions by 78% from 1990 levels by 2035 on the way to net zero by 2050. The start of the 26th UN Climate Change Conference, COP26, in Glasgow is less than three months away.
The prospect of trying to reduce emissions while they are still struggling with the disruption of Covid-19 is daunting for many firms, especially smaller manufacturers. Recently Make UK highlighted examples of companies that had achieved “incredible” results, often in quite simple ways (M&E, May/June). But, said chief operating officer Ben Fletcher, the biggest challenge was to get across the urgency of acting now.
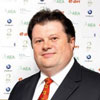
‘I would say that for 90-95% of SMEs energy efficiency is not on their agenda, to the extent that most didn’t even know what they were spending on electricity.’
Graham Cooper,
Systems Excellence
The M&E Editorial Advisory Board discussed this question at its most recent meeting, in particular focusing on levels of awareness of the net zero target in the maintenance and engineering community, as well as examples of progress and best practice.
Graham Cooper, founder and principal consultant of Systems Excellence, was formerly operations director for an Agfa plant in Leeds, and led a worldwide project to spread sustainable practices. He said: “In Agfa, we were highly aware of the net zero goal, but we used to host best practice visits to our site of SMEs, and I would say that for 90-95% of SMEs energy efficiency is not on their agenda, to the extent that most didn’t even know what they were spending on electricity, let alone have a target. They considered it a fixed cost. Bigger companies generally will have more of a grip on it, but I think for smaller companies, it doesn’t appear on their radar.”
Georgia Smart, UK Atomic Energy Authority asset management leader, said: “I think that large organisations are certainly aware, but I don’t think it’s trickled down to where it can have an impact.” Companies’ boards might talk about net zero, and produce glossy documents on sustainability, but little was being done to raise awareness among people on the front line.
John Saysell, MCP Consulting Group director of technical training, referred to a list published in February by Carbon Index of companies which had set a target to achieve net zero by a given date. But, apart from exceptions such as AstraZeneca, Lucozade Ribena Suntory, Nestle and Spirax-Sarco, there were few examples on the list of blue-chip manufacturing firms.
DAK Consulting director Dennis McCarthy said that was his experience too, with a few notable exceptions. He mentioned an engineer at Arla Foods, “who was absolutely keen on the amount of power a particular pump was using and had done lots of experimentation in his spare time”. And an associate had worked in Brazil with organisations focused on driving environmental improvement. “But I think there’s potential there for engagement on the front line that isn’t used,” he concluded.
In general positive examples of companies making progress appeared thin on the ground.
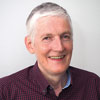
‘There is a direct correlation between energy use and OEE.’
Dennis McCarthy,
DAK Consulting
Mr Cooper said: “There’s a passive improvement going on because there’s more and more renewables going into the grid, so if people were tracking their CO2 emissions they would see a downward trend without doing anything. But there’s still a residual amount that needs doing.” He added that one “excellent” example was Crystal Doors in Rochdale, whose owner and managing director Richard Hagan was “an evangelist” for the environment. The company is on course to be carbon neutral by next year, and it has won numerous awards for sustainable manufacturing including a Queen’s Award for Enterprise: Sustainable Development last year. “We’ve got to make heroes of people like that, to get other people to recognise it,” said Mr Cooper.
Mr McCarthy made the point that there is “a direct correlation between energy use and OEE”. At a plant in Belgium, GE had given the maintenance manager responsibility for energy costs, and by improving maintenance, energy use had been reduced. BP in the North Sea had found that “just by setting equipment up correctly it used less power”.
Ms Smart said: “Part of it is to be able to measure your what your energy use is so you can demonstrate if you’re using a lot and then put some targets against it.” But net zero needed to become part of the business culture in the same way as safety.
“We need to make it an energy culture, where people know and feel engaged in the whole thing. At the moment people see it as a lofty ideal,” she said. Employees needed to be given some sort of incentive or recognition for bringing forward suggestions of how to save energy.
Mr Saysell said that in electrical maintenance more companies were expressing interest in power factor and how they could reduce it in order to cut overall electricity consumption, or the efficiency savings made possible by changing from using a motor direct online and adding an inverter, soft start or other more efficient method of drive. Mr Cooper thought there was a wider issue concerning electric motors, which are estimated to account for 60 to 80% of industrial energy use. “People don’t understand how much of it is waste. So many motors out in the field now (a) are old and inefficient but (b) they’re oversized.”
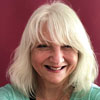
‘I think one aspect of net zero is to stop looking at it in terms of a money cost and look at what is the cost in environmental or energy terms.’
Georgia Smart,
UK Atomic Energy Authority
Traditionally a designer might calculate that a 20kW motor was adequate for a particular application, but might specify a 25kW item to be on the safe side. The design might then be reviewed by someone more senior, who might increase it to 30kW.
“You end up with a twice-sized motor, running at 50% load so it’ll be running at about 80% efficiency. If you right-sized that and put in the latest IE4 high efficiency motor, you’d probably pay back in energy savings in under 12 months,” he said.
Mr Saysell argued that benchmarking tools used by industry to assess performance, and standards such as ISO 55000 for asset management, were all based on optimising costs, such as the overall cost per tonne of production or OEE. These had a bearing on environmental impact but were not directly related to it.
Ms Smart said that for the next update of the standard, the committee was seeking to address this point, “to recognise that it’s not just money cost, and to talk about sustainability, not just environmental sustainability but all the UN sustainability goals.” It would be useful to have environmental measures not related to monetary cost.
“The argument is always that sustainability, or whatever, makes good business sense, but the truth is we run away with trying to turn everything into a physical cost, and sometimes that forces the cost of something else out.
“I think one aspect of net zero is to stop looking at it in terms of a money cost and look at what is the cost in environmental or energy terms.” It would then be possible to consider the two types of indicators side by side and come to a more balanced assessment.
Mr Cooper said that the standard on energy consumption, ISO 50001, is based on reducing energy consumption, not cost. He had used the standard as a vehicle to help replicate energy saving measures from the Leeds plant in Agfa plants worldwide. Senior management issued a directive that all plants must be accredited to the standard. “That enabled me to get the local people on the ground interested in energy, because from on high they had ‘you must get 50001’, and the only way you get 50001 is knowing where all your energy goes.” He suspected that the same standard might be used by the government as a means to push more companies towards net zero.
Mr McCarthy asked if there was a role for training. “What should be done at the front line level to raise awareness of what’s possible and maybe focus specifically on the importance of future environmental costs, rather than purely the lowest cost in the short term? How difficult would it be to tweak front line engineering training to incorporate the idea of net zero as being a desirable target?”
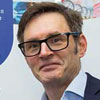
‘The idea of Net Zero has got to be driven up from the shop floor and down from management.’
John Saysell,
MCP Consulting Group
Mr Saysell said he could see two possibilities for incorporating net zero – in reliability courses alongside concepts such as mean time between failures, or in electrical courses where you might be teaching technicians about power factor and the use of inverters, over specification and so on.
“But with the maintenance technicians I’m not sure how much influence they’d have on specifying the equipment to start with. I don’t know whether you’d be at too low a level with the technicians – whether the training would need to target the engineering managers and more senior people, those doing the reliability aspects.” He concluded: “I think it’s multifaceted – it’s got to be driven up from the shop floor and down from management.”
Summarising, Mr McCarthy said it seemed that there was a lack of understanding or awareness of the net zero goal – there may be talk about it at senior level in larger companies, but for smaller businesses, something that needed to be done to raise awareness. Recognising and publicising role models – for example in industry magazines such as M&E – would be one way to help achieve this.
There was a need to change attitudes and develop a ‘sustainability culture’, and incorporate the concepts in existing training courses could play a role in this.
And there was a need for benchmarking measures or diagnostics for measuring carbon footprint and environmental effects which were not based purely on monetary cost.
As Make UK pointed out, immediate action is needed if the 2035 target is to be met. And, as this discussion concluded, there remains much to do.