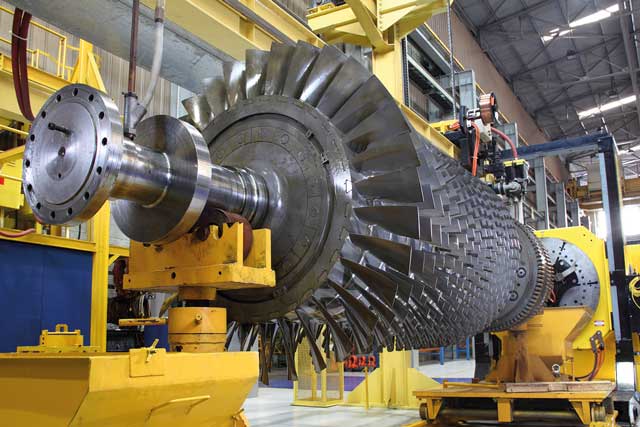
Daniel Walsh, Director of Product Management and Technical Sales Support at Spectro Scientific, outlines reasons why point of care oil analysis testing is proving increasingly effective at boosting reliability and generating cost savings.
In a recent reliability survey, between 60 to 70% of industrial facilities employ oil analysis as an important component of their reliability programs. Oil analysis gives a snapshot of machinery health, preventing unnecessary oil changes and predicting equipment failures before they happen. Most organizations draw oil analysis samples and ship them off-site to be analyzed in a laboratory. The results are sent back anywhere from days to weeks depending on location and industry.
Point of care oil analysis (today’s on-site oil analysis) has grown rapidly in popularity as leading industrial companies in several sectors have invested in these tools and software solutions to bring oil analysis in-house and are now reaping the benefits.
Here are five reasons why organizations across the world are investing in point of care solutions:
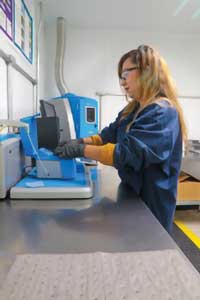
REASON #1 Rapid Analysis
Point of care solutions provide the maintenance team with Lab quality data right at the point of sampling and in no more than 15 minutes, rather than waiting for the results from the off-site lab. Remedial actions can be performed during routine servicing, or scheduled for later, thus increasing efficiency.
REASON #2 Lower Maintenance Costs
Point of care solutions have resulted in ROI payback in as little as six months.
Changing to a condition-based oil change has immediate effects like extending oil drains, reducing or eliminating outside laboratory testing and flags the early onset of machinery failure before it becomes critical. Also, monitoring incoming oil deliveries for cleanliness and type reduces risk to equipment.
REASON #3 Simplicity Breeds Confidence
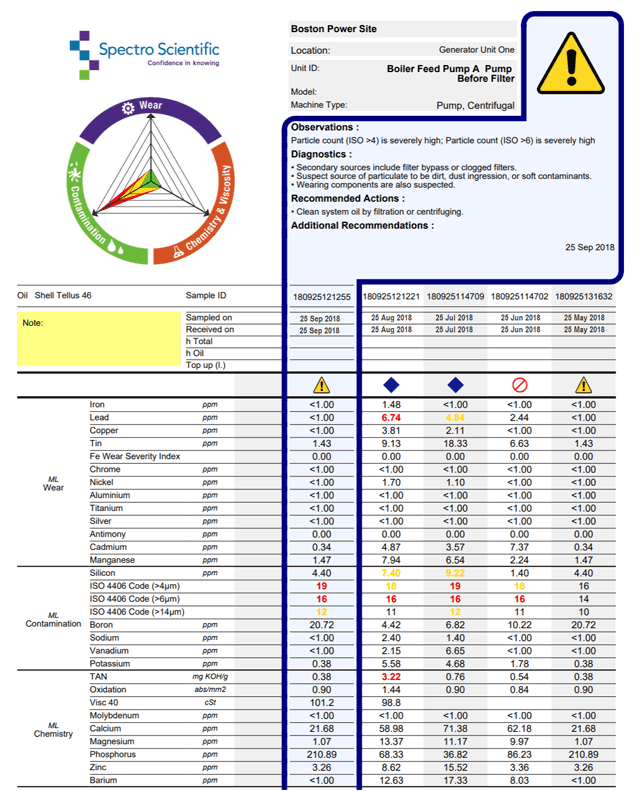
Major advances in instrumentation have resulted in easy-to-operate instruments, which means data can be generated by the maintenance team in the course of their daily tasks. The new generation of systems have software that not only provides accurate data, but also generates a single, easy to interpret report complete with diagnostics and remedial action recommendations.
REASON #4 Better Analytics for Decision Making
It is a fact that freshly sampled oil provides better insight to the equipment health. Retests to corroborate or debunk a possible problem can be performed quickly in-house at little extra cost.
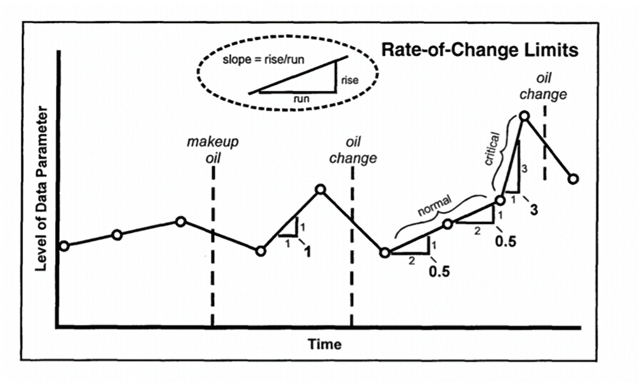
REASON #5 Duplicate Success with Enterprise Tools
Shared software platforms, with the same point of care solutions throughout multiple sites, increase efficiency within an enterprise. Equipment reliability can be viewed at regional, national or even global levels. Problem-solving knowledge from equipment maintainers also can be shared across the enterprise, so people at each site can easily tap into others’ experiences and expertise.
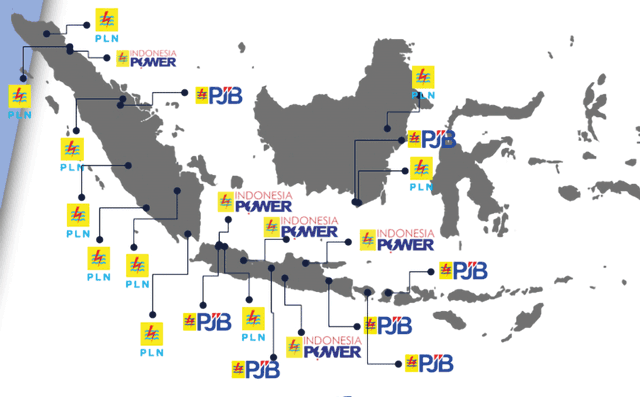
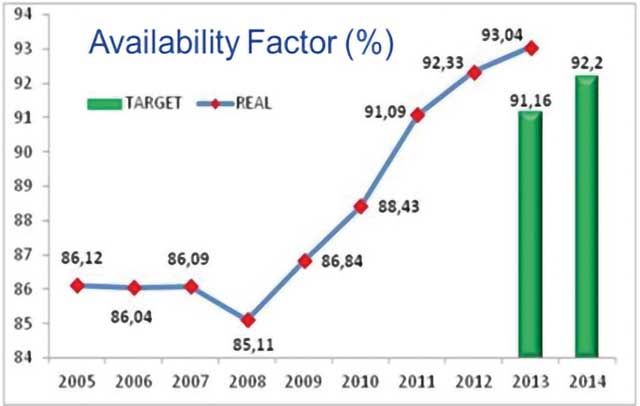
Summary
Oil analysis at various plant locations was once reserved for those who could duplicate off-site laboratories. This model has changed in the last few years. The new miniature, rugged, portable instruments make this process simple and accurate without the need for solvents and dangerous chemicals. Point of care oil analysis is a proven and viable path forward for an organization looking to reduce risk.
AMETEK Spectro Scientific
www.spectrosci.com | sales.spectrosci@ametek.com