Safe and suitable storage of hazardous substances and chemicals is essential if you want to avoid fires, leaks or accidents involving spillages. For this reason, it is imperative to adhere to Health and Safety Executive (HSE) guidelines and best practice principles when working with or storing any hazardous chemicals. Injury to personnel and damage to equipment, stock or the environment can be minimised through care and attention, and by following the advice ahead.
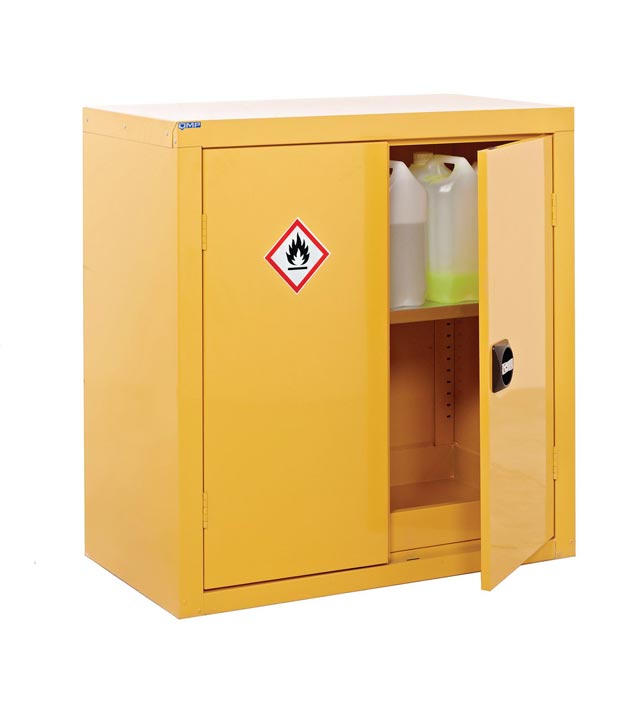
Dedicated cabinets
A great place to start is with a Metal Storage Cupboard or Cabinet that conforms to COSHH (Control of Substances Hazardous to Health) standards. These cabinets are constructed from steel for strength and to thwart any break-in attempts, and they include lipped internal shelves and liquid-tight welded sumps to capture and retain any leaks from containers. Your storage cabinets should also feature locking doors to prevent unauthorised access, along with warning signs on the doors to alert users of the contents.
The classic COSHH chemical cabinet is finished in a yellow powder coat to make it immediately recognisable. Other popular examples can be found in grey or in red to highlight different contents, which should also be marked clearly with warning stickers.
The cabinet should be installed in your premises on a flat surface according to the guidelines below, with unobstructed access to the contents. This ensures that any personnel accessing or storing hazardous chemicals can do so with minimal risk of dropping the substances through overstretching or not being able to get a good grip.
If you are using a mobile hazardous substance cabinet, make sure that you and your personnel are still conscious that the contents are potentially dangerous, and manoeuvre the cabinet with care and attention.
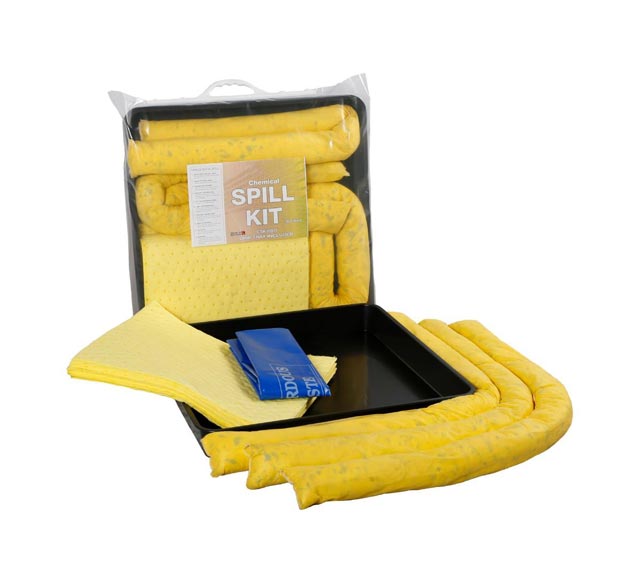
Separate storage
Keeping different chemicals and hazardous substances separate from each other is the cornerstone of good chemical storage. Each storage space should also be optimised by ensuring that access is clear and easy for authorised personnel, and the area is well ventilated with hoods, ducts and vents in place. It should be temperature-controlled and appropriate clean-up and containment equipment such as Chemical Spill Kits must be close at hand.
Moving corrosives and acids from larger, bulk containers and drums to smaller, more manageable containers is best practice and should be done as soon as possible and whilst wearing the appropriate personal protection equipment (PPE), and ensuring that particular care and attention is taken. Drip trays or absorbent matting should be deployed under the transfer area to catch and collect any stray drips or leaks before any damage can escalate.
Regular inspection
In addition to having their own storage space/unit, corrosives and acids should be inspected often for signs of leaks or damage to containers. Ventilation equipment and all hoods, ducts and vents should be kept clear and clean, and checked and maintained regularly.
Tightly sealed chemical containers
All chemical containers should be sealed as tightly as possible, to prevent leaks as well as the build-up of fumes. These containers should also be kept off the floor, but no higher than eye level. Racks used for storage should be firmly secured to the walls and purpose-built drainage and spill barriers should be in place to tackle any spill emergencies.
Temperature control
Chemical containers should always specify the correct temperature range for storage and use, and these minimums and maximums should be closely monitored and adhered to. Storing a pressurised container at too cold a temperature can cause the chemical to freeze and the container to crack, while overheating can cause flammable substances to ignite.
Chemical bunding
Using bunding where chemicals are stored is standard safety practice, and for good reason. Bunds are placed under chemical storage containers, and in the event of a leak or spill act as a protective guard for both the environment and personnel. This kind of safeguard should be inspected every three years at a minimum.
Chemical storage regulations
It is the employer’s responsibility to ensure that chemicals and other hazardous substances are stored in a safe way and to provide training for employees in safe practice and emergency response. This responsibility is outlined in the Control of Substances Hazardous to Health (COSHH) regulations, which also highlight the importance of frequent and thorough risk assessments and stringent control measures.
However, it is also important that employees are familiar with the regulations, or at the very least are trained in best practice behaviours. The HSE provides a checklist for employees to follow, which includes simple checks like keeping ventilation and air supply units turned on and clear of obstructions, handling packages containing dangerous substances with care and attention, checking for signs of wear, tear, decay or damage, making sure to use appropriate manual handling equipment where available (sack dollies, drum lifts, etc.), washing hands frequently, not using solvents on the skin and ensuring any spills or leaks are either quickly escalated to a supervisor or managed/cleaned effectively with any pads or absorbents subsequently disposed of carefully and correctly.
Managing chemical inventory
It is a statutory requirement as well as responsible health and safety practice to monitor and maintain the inventory of chemicals on site. This includes ensuring that all potentially hazardous chemicals are clearly labelled, correctly stored and expiry dates are strictly adhered to. This activity should be done at least annually.
Remember that when it comes to storing chemicals, you can’t be too careful. If you have any doubts about the suitability of your storage practices, follow the HSE guidance or speak to a qualified Health and Safety consultant for more advice.
For further information: www.firstmats.co.uk