Framework agreements can minimise repair times and extend the life of vital assets, as this case at a power station demonstrates, says Tom Freestone, head of customer support services at Sulzer.
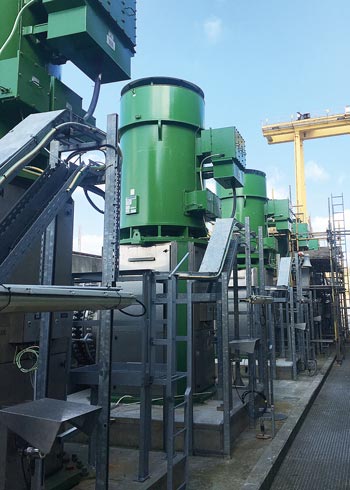
Meeting industrial and domestic demand for electricity requires careful management of the assets used. Coordinating generating capacity with maintenance requirements is a delicate balancing act, with the aim of minimising downtime.
The power generation industry understands the advantages of high-quality workmanship in prolonging asset performance and increasing reliability. One of the procedures used to minimise delays and optimise maintenance tasks is the framework agreement. This establishes a shortlist of suppliers that have shown they meet the required standards for workmanship and health and safety, as well as management procedures and cost efficiency.
At the same time, a scale of costs can be agreed between the two parties, giving the customer an accurate understanding of the costs involved in a wide variety of projects. The approved supplier can then be asked to quote for maintenance projects in the knowledge that it has already met the necessary criteria. This can reduce the time to repair important assets and maintains the high standards of the generating plant.
This approach can also optimise the process when it is necessary to remove large assets, such as pumps and motors, from service and overhaul them as part of a preventive maintenance strategy. Sulzer has been involved in such projects with several power generating sites throughout the UK and has a number of framework agreements which are managed by the service centre closest to the customers’ sites.
High voltage pump motor overhaul
As the initial point of contact, the local service centre coordinates all the assets and personnel required to complete the project through the service centre network. A good example was the recent overhaul of two high-voltage motors, one from a cooling water pump and the other from a boiler feed pump.
Both motors were disconnected and removed from service by engineers from the Avonmouth service centre, close to the power station. The refurbishment work was completed by the Southampton service centre, with additional expertise provided by engineers in Birmingham, where the motors were finally tested before being returned to the customer.
The boiler feed pump motor had a history of high partial discharge readings in the windings and action was required to manage the situation and extend the useful life of the windings. This would allow the power plant to plan for a complete rewind at a later date and improve the reliability of the motor until that time arrived.
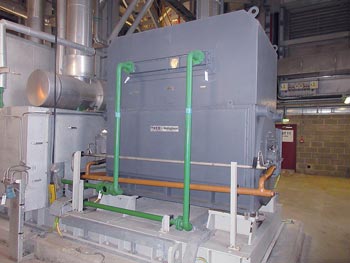
to extend its service life
Extending service life
Sulzer suggested reconfiguring the windings by breaking the star point and connecting the original supply leads to create a new star point. This would extend the service life of the stator winding by taking the in-rush current away from the phase coils, reducing the stress on the windings and allowing the operator to start planning for a complete rewind in the future.
After the new windings had been reinsulated and varnished, the motor was reassembled with new bearings and seals before the remainder of the testing was completed. Both motors were shipped to the power station and reinstalled by Sulzer’s field technicians before being commissioned.
The framework agreement with the customer was a great advantage because all the terms and conditions had already been agreed. This saved time and provided assurances of the quality and the procedures used to complete the project.
With any work that Sulzer carries out, customers are invited to visit the service centre to review progress or see first-hand any unforeseen developments uncovered during an inspection. Through continuous communication, customers receive an efficient and cost-effective solution.
The final result from this project was very positive. Downtime has been minimised and plans are in place to make further improvements during the next planned outage.