Model-based system engineering can be used to augment continuous vibration monitoring by predicting how equipment will react in unusual operating conditions. Dr Balaje Thumati, head of technology at HBK Reliasoft and Dr Frédéric Kihm, product manager at HBK Analytics and Signal Processing, explain.
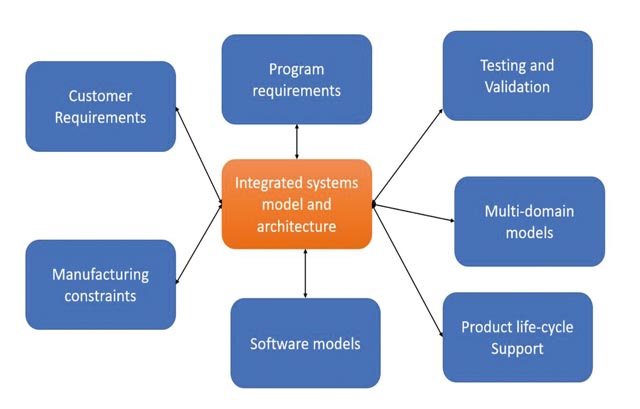
Recent unexpected weather conditions in parts of the US subjected energy and utilities operators to extreme load demands which could not be satisfied by existing energy generation and distribution systems. In some cases, renewable energy sources such as wind power farms experienced extremely cold temperatures, which resulted in rotating components seizing up.
Wind turbines are instrumented with continuous monitoring systems to aid smooth operations. This may include sensors such as accelerometers, tachometers, displacement probes, and so on. The sensors measure various operating characteristics of the turbine, which assist engineers and technicians in evaluating its operating performance, determining its condition, and scheduling maintenance. However, the instrumentation set-up does not capture changes in the operating environment until their onset, which in most cases is too late. A model-based system engineering (MBSE) framework could help to study equipment performance under a range of operating conditions.
MBSE is a system engineering methodology that helps to streamline various engineering processes, from requirement analysis and system modelling, analysis, verification, and validation through to various phases of the product life cycle.One of the most important elements of MBSE is the use of a multi-domain model for equipment operations and support. In general, a multi-domain model combines elements of different disciplines such as mechanical, electronic, electrical, hydraulic, and others.
For example, in wind turbines, models could simulate power generation by controlling the nacelle and blade pitch angle, which would change depending on operating conditions. Because of the integrated nature of the model, a potential anomaly in operation could be detected and handled under a risk mitigation plan.
Vibration monitoring of rotating equipment such as wind turbines is an important measure to determine the equipment’s condition. In this new approach, by entering real-time vibration data into an MBSE model, one can perform a comprehensive analysis of the equipment to generate expected performance. For example, domain-specific models can simulate operating characteristics for normal weather conditions, which could be compared with actual vibration data to detect potential failures. When operating conditions change unfavourably, the model could predict failure in rotating equipment before an accelerometer records changes.
An overview of integration across domains in an MBSE framework is shown in Fig. 1. All elements of the product life cycle are created and stored as digital artefacts. In Fig. 2, a representative multi-domain model is presented.
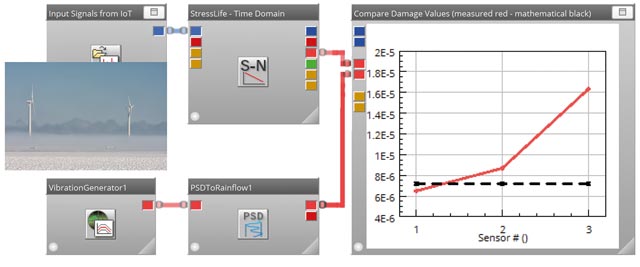
Vibration data is collected from rotating equipment, which is processed and compared against a mathematical model to detect deviations in performance and predict potential failures. In this case, the fatigue life of the rotating component is calculated using both the measured vibration data and a mathematical model. A comparison of both the outputs is tracked over time to detect potential failures. The mathematical model allows simulation of various operating environments and the more effective prediction of anomalies, which might not have been possible with vibration monitoring alone.
Since an MBSE framework could digitally store several artefacts such as system architecture, parts information, drawings, cost, and technical specifications, decision-makers would have more information available to draw conclusions. In summary, the ability to simulate and evaluate various operating conditions is one of the biggest benefits of an MBSE framework and could significantly augment traditional vibration monitoring systems.
HBK provides a complete portfolio of offerings that unite the physical world of sensors, testing and measurement with the digital world of simulation, modelling software and analysis to help engineers deliver durable and reliable products and avoid the cost of unexpected failures. Its Engineering Solutions team provides consulting services in the areas of big data analysis, system simulation, and model-based systems engineering.
Further information on analytics from HBK: www.ncode.com/products/ncode-streameddata-analytics
info@hbmprenscia.com