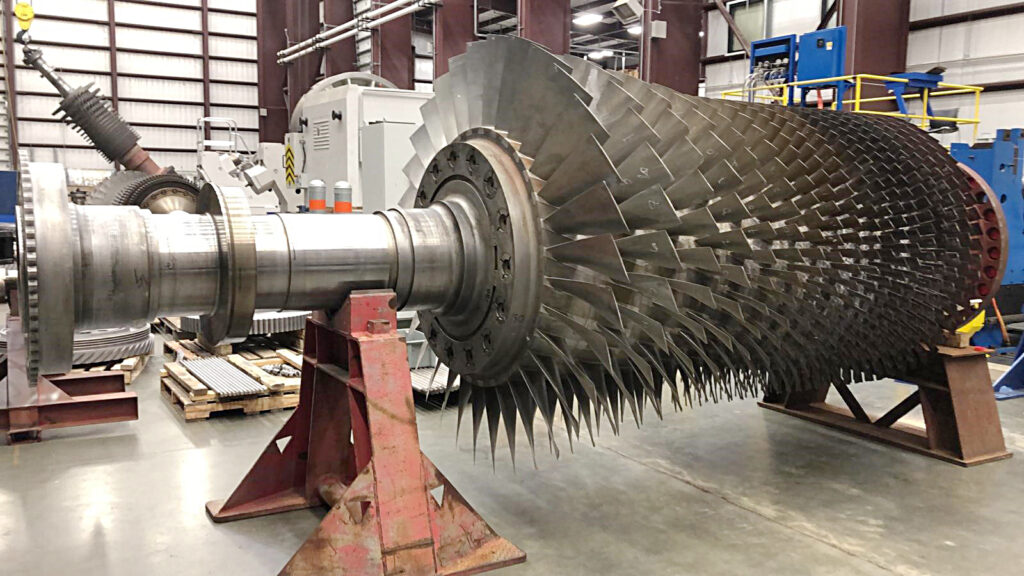
Planning ahead and maintaining spare parts are important aspects of operating gas-fired power plants. The turbines are expected to create electrical energy around-the-clock, so downtime needs to be minimized. For one plant in Mexico, an unexpected turbine crash required a quick solution, and the spare rotor was also awaiting repair. Fortunately, Sulzer delivered an innovative solution inside 45 days to get the plant running again.
National power grids rely on a load base of power stations with peaking units being brought online during times of maximum demand. One power plant in Mexico operates two GE 7FA units, rated at 128 MW each, and is contracted to deliver power to the grid 24/7. As part of its planned maintenance activities a spare rotor, which had a damaged turbine section, was due to be refurbished.
Initial inspections
As a specialist repair provider for gas turbines, Sulzer had been called in to inspect the spare rotor and provide a quote for its repair. While this was in progress, one of the operational turbines suffered a failure and was taken offline. At this point, attention turned from the spare rotor to the in-service component, with the aim of repairing it as quickly possible.
Sulzer visited the customer and carried out a visual inspection of the failed rotor and found that it had damage to the compressor section, but the turbine section appeared to be in good order. At the same time, the project for repairing the gas turbine was put out to tender, with four companies, including the original equipment manufacturer (OEM), taking part.
It is one of the facts of government ownership that all work such as this has to be tendered, which inevitably adds to the overall amount of downtime. In this case any increased delays would put greater pressure on the remaining power plants while causing lost revenue to the tune of around USD 8 million per month.
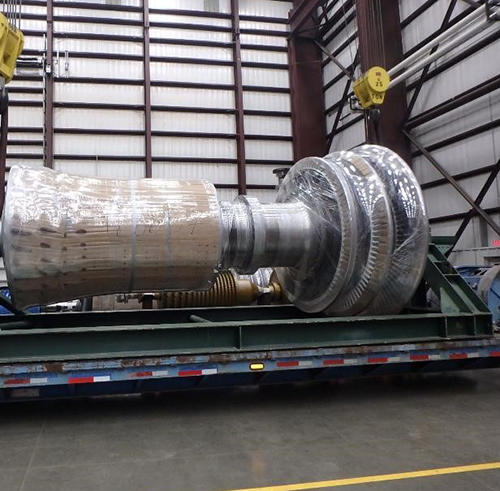
Innovative solution
Sulzer’s solution for a fast and effective repair was to combine the two sections in good condition from each of the customer’s rotors, creating a new rotor for the turbine. The company was able to offer a very competitive project because of its stock-holding of spare parts and in-house expertise, both of which would keep the repair time to a minimum.
Although the provisional schedules for the repair provided by each company were similar, they were all based on the assumption that the two rotors were the same. However, the customer either didn’t know or failed to identify the exact type of 7FA turbine they were operating. As the design has been modified by the manufacturer, the .04 (4th iteration of the 7FA) rotor is the latest, and was operating in the turbine, while the spare was a .03.
The two models are interchangeable, with the major difference being the design of the turbine blades. With the exception of the OEM and Sulzer, the revelation that the crashed rotor was a .04 would have almost certainly made the project undeliverable for the remaining companies. However, even for the OEM, the prescribed delivery time was too tight, and the company withdrew from the final round of submissions.
Minimizing downtime
Once both rotors arrived in Houston, the turbine sections were disassembled. All the blade hardware was different between the rotors, confirming the initial findings. This made it necessary to install .04 hardware on the rebuilt rotor. Fortunately, the Houston Service Center is involved with such a volume of gas turbine repairs, that it holds a complete set of hardware in stock. Furthermore, it has the facilities required to de-stack each rotor and reassemble them when the repairs were complete.
An in-depth examination of the good compressor section found some of the blades did not pass inspection, so it had to be disassembled. 30 blades had to be replaced, while the remainder were hand-dressed so that they were operational. Once complete the compressor section was reassembled.
The refurbished turbine and compressor sections were coupled together and the bearing journals were replaced. On the turbine section the bearing journal is a sleeve, common to both .03 and .04 machines, and another part that Sulzer held in stock. A new component was installed and the complete rotor was packaged in the shipping frame and transported back to the power plant. In all the repair took just 45 days to complete, including the time to ship the rotor back to the customer.
Logistics solutions
Just the logistics of shipping these rotors, which measure 329 inches (8.3 meters) long and weigh 114’240 lbs (51.8 tonnes) including the shipping skid, is a complex task. Sulzer’s international logistics department managed the whole process including all the paperwork required to cross the international border and deliver the turbine with minimal delay. It also arranged for all the necessary shipping frames to ensure both turbines could be moved and transported safely.
Omar Diaz, Sales Manager for Sulzer, comments: “Sulzer was the only maintenance provider to offer the solution of using both rotors to create one operational component. With time of such importance in a project like this, being able to turn round the refurbishment of the rotor in just 45 days was beyond the expectations of the customer when the original crashed.”
Additional support
Although Sulzer delivered the project on time, the turbine still needed to be installed and commissioned. The local company that had been contracted by the operator for these tasks encountered some difficulties. The operator then returned to Sulzer for additional assistance with the support ring on the casing and the oil seals on the bearing, both of which had been damaged during the original failure.
For the support ring, Sulzer was able to leverage its extensive design and manufacturing facilities to deliver the new part in just 17 days. The time for the OEM to manufacture the new oil seals would have been a minimum of 17 weeks, but Sulzer was able to deliver the same parts in just three weeks.
Omar Diaz concludes: “With downtime incurring significant losses for the operator, speed was of the essence, and the additional task of manufacturing new seals and support ring was given to Sulzer. Considering the lost revenue attributed to downtime, projects such as this carry considerable penalty clauses for late delivery, so repairers need to have confidence in delivering on the timeframes they promise.”
The customer understood that Sulzer could deliver the complex repair project with a minimum of downtime and this is the reason why they asked for additional support with the remaining parts. These have been completed, shipped to the plant and installed. Following all the work delivered by Sulzer, the power plant is now back up and running. Repairs to the damaged rotor parts are under consideration.
For more information on Sulzer, visit www.sulzer.com