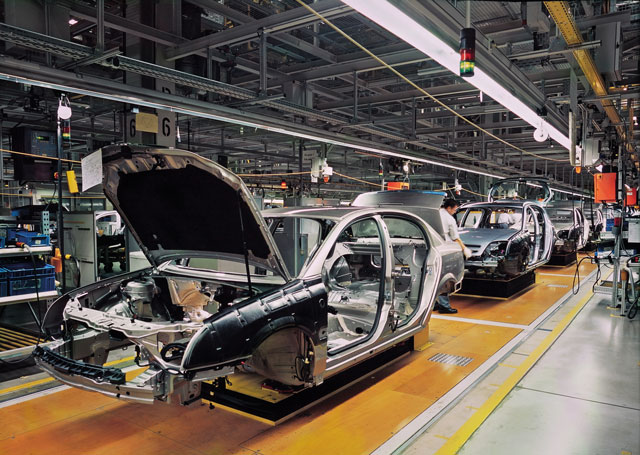
With the varying demands of metalforming applications, it is important to select the right fluid for the job. Cagri Canga, UK & Ireland industrial sales manager, and Songul Facey, metalworking fluids technical sales manager at Total UK, explain the key considerations.
There are many types of metalforming, including complex processes such as sheet metal stamping, wire drawing, fine blanking and punching, hydroforming, rolling, hot or coldforming, and deep drawing. Because of the varying characteristics of these applications, there are many factors to be considered in selecting the right fluid.
Fluid selection depends on many considerations, including forming difficulties, the subsequent processes and their application, water quality, the type of forming metal, pre-and post-operation needs, customer preference, and equipment type. First, it is necessary to understand the duties of lubricants. Metalforming lubricants provide the same basic functions as metal-removal fluids, including lubrication, cooling, scrap-metal removal, and corrosion protection.
Lubricity is one of the significant properties because the metalforming fluid must reduce friction and act as a barrier to minimise contact between the die and the workpiece. This means the fluid needs to be formulated with fatty oils or ester-based lubricity additives, and, in some cases, extreme and anti-wear pressure agents.
Another specific requirement is corrosion protection, particularly following the metalforming application as parts may need to be kept in storage for up to six months. This means that the fluid may require a corrosion inhibitor.
Some of the other requirements are:
• The oil fi lm should be homogeneous and should not cause dry friction by tearing at high pressures
• It should wet the material surface well
• It should be easily cleaned after the operation and not cause chemical reactions on the tool and material
• It must be stable and should not lose its lubrication capability at operating temperature
• It should be compatible with subsequent processes such as welding or coating
• It should not contain materials that are harmful to living creatures and the environment.
Lubricants should prevent contact between the tool and workpiece, prevent cold welding, reduce friction, and remove heat. The goal is that tools, dies, and other metalforming components will produce the maximum numbers of end-product parts, with minimum maintenance due to degradation from excessive heat and wear.
Metalforming lubricants are generally categorised into two main types, straight and water-based lubricants, and are classified by the base oil such as mineral, semi-synthetic or synthetic. Pure oils fall into two groups: volatile, which are solvent-based, and neat.
In the formulation of both types, there are corrosion inhibitors, performance additives such as polar agents, and anti-wear additives, and as well as extreme pressure (EP) additives depending on the severity of the operations. Water-based fluids also have emulsifiers to mix the lubricant with water, and de-foamers to prevent the formation of foam.
To give a simple comparison between the two technologies, switching from straight oils to a water-based product can provide a cost-effective solution that is more environmentally friendly and allows for easier cleaning. And in many cases the presses can run faster because of the cooling properties of water. However, in some severe operations, the performance of water-based lubricants might not be sufficient, particularly in applications such as deep drawing, where the use of very hard metals in increasing.
In those applications EP additives, such as chlorinated paraffin, are inevitably required. In such cases, the issue is not only lubricity or the ability to draw the materials, but also health and safety compliance, and degreasing. Among considerable research and development activities at Total, replacing chlorinated paraffin in severe draw applications is a continuing project.
Total’s metalforming lubricants are developed to exceed all the requirements highlighted above. The range is designed to keep machinery and tools performing bending, shaping, stamping, and stretching operations correctly lubricated and functioning effectively, allowing the fabrication of excellent-quality products while keeping operations are as efficient and low maintenance as possible.
Total Martol is a comprehensive range of high-performance metalforming fluids.
Features include exceptional anti-wear properties, reducing the frequency of tool changes, and low volatility. The product is transparent, for better machining conditions, and resistant to oxidisation, improving the service lives of products and tools.
A non-stain formula makes sure products and tools look their best, and there is low or no odour. Adhesion is excellent on all types of metallic surfaces. Less carbonaceous matter and residues means less cleaning, while limited degreasing time helps to improve productivity.
The product of constant R&D, each fluid has been formulated with input from Total’s industry partners to overcome the problems encountered by metalforming manufacturers and their machinery, to cover an extensive range of operations and applications.