The mechanical and electrical behaviour of machines are intimately connected. MBVI systems can provide new insights into how equipment is behaving, indicating some of the hidden stresses, says Faraday Predictive operations director Geoff Walker
Phase unbalance might sound like an unexciting, nerdy measurement of electrical power supply quality of little interest to anyone except for trainspotting electrical engineers. But in fact phase unbalance is important to maintenance engineers for several reasons.
It can cause significant additional mechanical stresses on shafts and transmissions as a result of the torsional oscillations created; it can shorten the life of your motors as a result of higher heat generation inside the motor; and it can itself be caused by certain mechanical aspects of the machine that create oscillations in torque at particular frequencies.
So what should you do about it?
Causes of phase unbalance
Phase unbalance means the three phases of a three-phase supply are not all of equal magnitude – for example here one phase (red) is larger than the other two:
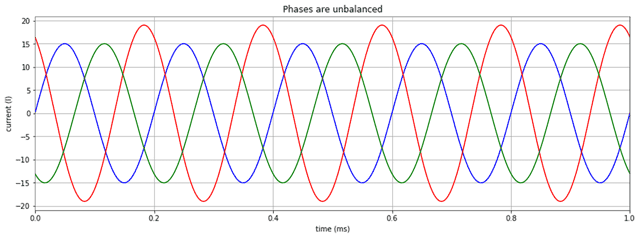
Phase unbalance can occur either on the voltage or on the current – or most likely, on both.
Voltage unbalance is generally caused by the electrical supply to the machine rather than by the individual machine itself.
Current unbalance can be caused either by a voltage unbalance or by a problem with the wiring to the motor, a fault in the motor, or the behaviour of the driven machine.
Unequal resistances in the cabling to the motor can result in lower current in one phase. Typically the problem arises in dodgy or loose connectors. Thermal imaging cameras can often help identify this sort of problem rapidly.
Mechanical behaviour that puts a higher torsional load on the machine in the same place on each rotation of the shaft – such as rubbing of a warped brake disc or elliptical brake drum, or rubbing of a bent or eccentric shaft – can also cause current imbalance. Because higher load results in a higher current, rubbing at the same point in each revolution will cause a higher current at the corresponding point in the stator windings.
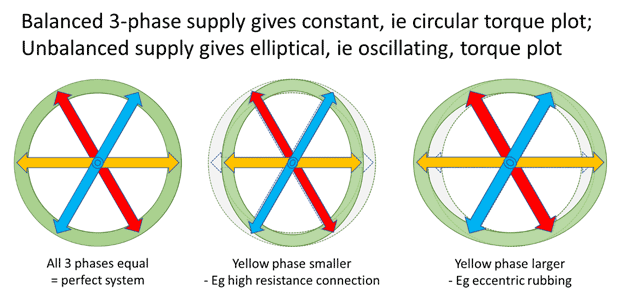
Effect of phase unbalance
Current unbalance leads to heating of the stator windings, as a higher current is required to provide the same overall torque. Typically 1% voltage unbalance causes 5% current unbalance, which leads to a 10ÅãC temperature rise, which in turn halves the life of the motor windings.
Current unbalance leads to oscillating torque output from the motor – which places additional loads on shafts, couplings and shear-pins.
The first diagram below represents a polar plot of the strength of the magnetic fi eld (which controls the torque of the motor) in a three-phase motor. When all three phases are equal, the result is a magnetic fi eld of constant strength rotating at constant speed.
If one of the phases is weaker, for example because of high resistance in the supply to that phase, the magnetic field created by that phase will be weaker than the other two, causing an elliptical torque plot (middle picture). The torque increases and decreases twice per cycle, putting an oscillating torque load on the shaft, coupling, transmission and driven machine, which can lead to fatigue failures of components such as shear pins.
The process can also work the other way – a load that creates an oscillating torque once per revolution will result in greater current being drawn by the phase associated with the location of the increased load (see right-hand diagram). So current unbalance can be a diagnostic tool to detect problems including eccentric or elliptical brake drums, or rubbing of eccentric or bent shafts.
As explained in previous articles (M&E, March/April and Jul/Aug 2020), model-based voltage and current systems (MBVI) use a mathematical model of the relationship between current and voltage to identify distortions on the current waveform. This means that in addition to detecting overall electrical features like current unbalance, they can also detect a wide range of more subtle mechanical problems including unbalance, misalignment, bearing problems, rubbing, loose belt drives and so on, as well as identifying excessive energy consumption and waste.
For more details see:
www.faradaypredictive.com/technical-education/diagnostic-outputs/465-phase-unbalance-and-rubbing/
info@faradaypredictive.com | Phone +44 333 772 0748