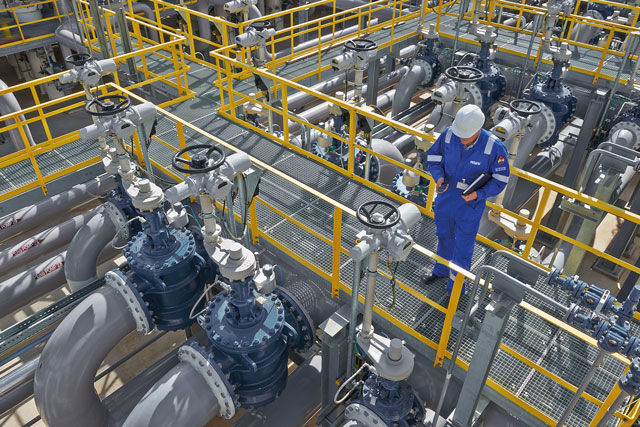
Data collected from intelligent actuators can provide the key to effective maintenance of flow control equipment, says Mike Devrell, Rotork site services programme manager.
Flow control is at the heart of numerous industries, markets and applications. It plays a key role in allowing manufacturing processes (including oil, gas, water, power, chemical, industrial and process control applications) to operate. Effective flow control can improve efficiency and yield, reduce emissions, minimise environmental impact and assure safety for these industries.
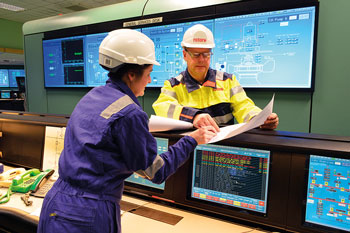
The control of fluids in a safe, reliable and efficient manner requires specialist equipment, including valve actuators to move and control valves. Actuators can be pneumatically, hydraulically or electrically powered. On receiving a control signal, an actuator operates a valve and allows the controlled flow of a liquid, gas or powder. Automation of this kind allows for a high degree of reliability, repeatability, accuracy and efficiency, while always operating in a safe manner.
Actuators and related flow control products are key assets that require maintenance programmes to make sure that they are always available. Valves and actuators are relied on to operate smoothly day in, day out. They must be able to work in harsh environmental and operating conditions, with extreme temperatures, excess vibration and other factors which may affect their ability to operate at peak efficiency.
A comprehensive maintenance programme allows them to operate at optimum performance. If actuators and other flow control equipment fail, become obsolete or are not running properly, the implications can include poor plant or process performance, impaired product quality, reduced yields, monetary loss and reputational damage.
Monitoring and analytics
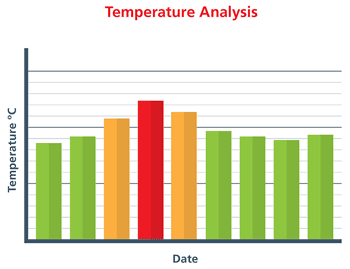
A maintenance strategy using advanced analytics, condition monitoring and anomaly detection can provide vital insights that allow planning and undertaking maintenance to be optimised, so required work can be identified and targeted at the appropriate assets at the right time.
Intelligent Asset Management from Rotork is a cloud-based asset management system for intelligent actuators and the equipment they operate. It collects information from the datalogs held in intelligent actuators, providing easy and accurate reporting and monitoring of the condition of actuators and valves. Collection of data from the field can be undertaken by the customer or by Rotork, depending on budget and preference.
Data such as torque, temperature, vibration and event log information is analysed directly from the field. Information is presented through summary views and colour-coded maps that simplify complex analytics into easy to understand visuals.
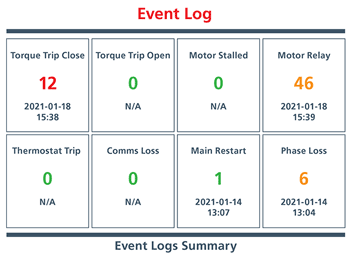
Intelligent Asset Management removes the need to manually review data, saving time and reducing the likelihood of missing problems, while early detection of anomalies can save expensive repairs. The system is web-based and easy to access, detecting anomalies and providing easy, accurate reporting and monitoring of the condition of valves, and allowing active maintenance. Additionally, a set cost from the service provider keeps budgets at a guaranteed and manageable level.
An effective strategy
An effective maintenance strategy for flow control assets should deliver the appropriate level of maintenance based on risks evaluated from knowledge of an asset’s criticality and condition, while also considering advances in technology, obsolescence and changing operating environments. A system like Intelligent Asset Management, using real-life data from actuators, enables timely maintenance that reduces failures in flow control, improving safety, quality, performance, yields, and reputation for each plant or site that uses it.
information@rotork.com | www.rotork.com | +44 1225 733200