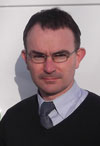
Anaerobic digestion processes provide a stiff test for pumps and their maintenance regimes, says Paul Davies, key account manager at pump and mixer manufacturer, Landia
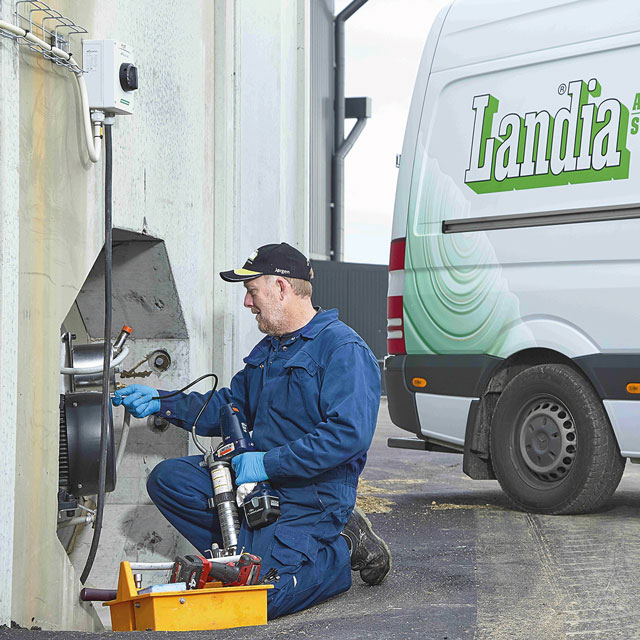
The incident in December at a water recycling centre, which cost the lives of four people, has sadly highlighted the need for increased vigilance. While investigations into the exact cause of the explosion in a sludge digester continue, there is no doubt that as more companies invest in waste-to-energy as they work towards carbon net zero targets, maintenance regimes will form a crucial part of safety standards. This is true of the water industry, which is capturing methane gas from wastewater sludge to create green energy, as well as for waste management companies producing the gas from food waste and farmers from crops and manure.
To bring about those important and lucrative gas yields and then optimise them, the digester (tank) mixing system is crucial. This is no job for a standard pump because it has to deal with wastewater solids or similarly problematic solids in the other types of anaerobic digestion (AD) feedstocks. A sturdy chopper pump is best suited to reduce particle sizes and accelerate the digestion process.
In the rush to embrace biogas/anaerobic digestion in the past decade or so, many raced to buy systems that they now regret – simply because of choosing equipment that has wearing parts inside the digester. This then takes a monumental task just to service it, requiring draining down the tank with the resultant interruption of continuous gas generation.
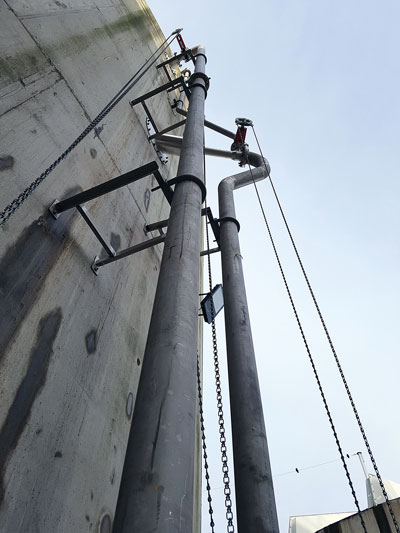
Producing biogas from sludge, food waste, crops or manure is not something that can easily be switched off and then back on.
Any AD operator with mixing/ pumping equipment outside the tank will immediately tell you how much easier it is: you can see it, you can hear it, you can check for vibration. A simple walk-by inspection can include checking on a pump that has a sight glass, which allows you to see conditions in the oil reservoir.
Nobody wants a pump down; in biogas/ AD in particular, the urgent need to keep feeding the digester – often to fulfil an energy contract with the National Grid – creates some very heavy stresses on maintenance engineers.
The chopper pump is best mounted away from the gas zone, so there’s no need for breathing apparatus, which is essential for servicing or retrieving a broken mixer inside a digester or inspecting equipment such as pressure vacuum relief valves.
And if designed correctly, everything is at ground level, so there are no harnesses, barriers or stairways. Eliminating working at height is much more effective from a maintenance point of view, as well as providing greatly improved health and safety.
An easily-accessible pump will always prove far more economical in the biogas/AD sector because, tackling harsh solids, it will inevitably require attention. The grit content of a water industry digester can be phenomenal; food waste plants have to contend with endless packaging materials – all at a very low pH – and pumps in farm-based biogas tanks have to cope with straw, stones and anything that people consider reasonable to throw into a feedstock.
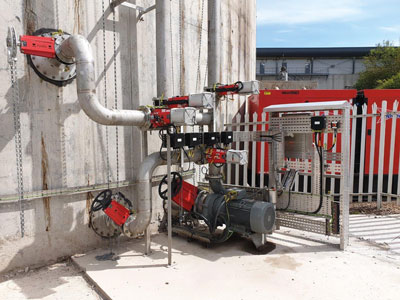
Landis manufactures its chopper pump (which the company invented in 1950) so that it allows front-end and wearing parts to be changed using nothing more complicated than an Allen key. Seals may take a little longer, but again, it’s advantageous to use a pump that requires only standard tools.
Finally, you should select a chopper pump for biogas/AD applications that doesn’t rely on the actual blade to act as the chopping mechanism. Otherwise you’ll need to continually reset the blade. This has to be tensioned to a tight tolerance against the casing so that it has something to chop against, or the pump blocks.
Far better to specify a chopper pump that has been designed with an external knife system in which the “cutters” (and impeller) can be changed in around 15 minutes.
Quicker and much safer options are readily available for biogas/AD plants, which are easy to retrofit without having to drain down the digester. The industry owes it to its workforce to reduce the risks.
Landia 01948 661 200
pd@landia.co.uk | www.landia.co.uk