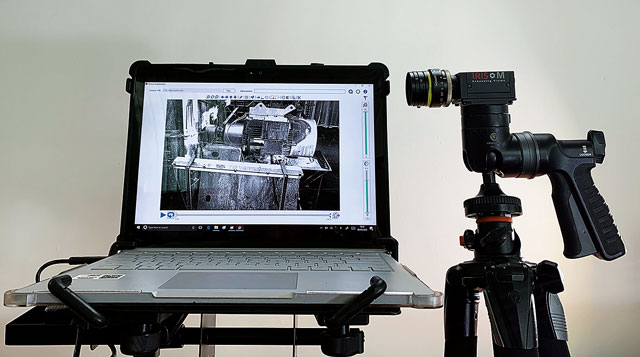
movements
Motion amplification can be a powerful tool in its own right but is even more effective when used alongside other advanced digital tools. Simon Hirst, asset integrity division manager of AVT Reliability, considers the benefits.
Causes of structural resonance
Structural resonance might be caused by something relatively small at source, but its impact can be huge. For example, fatigue damage in a welded steel connection will typically vary proportionately to the cube of the stress level. Even a resonant amplification of ten could reduce the life of a component through fatigue by a factor of 1,000.
The motion amplification (MA) video-based digital tool was developed to make imperceptible vibration-related structural issues visible. It effectively turns every pixel in a digital video image into a vibration sensor.
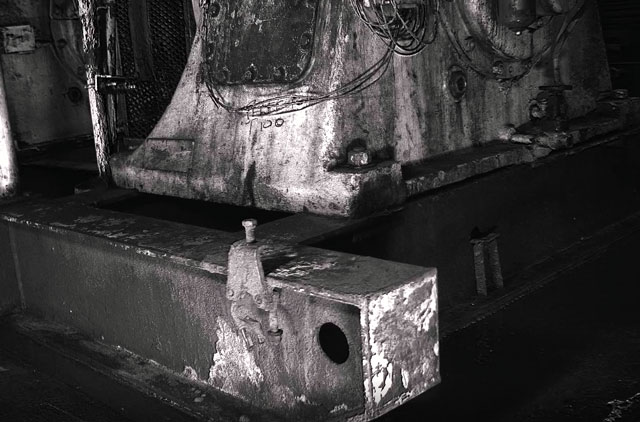
machine base.
The MA camera captures high-quality digital video images, and sophisticated software massively exaggerates the relative movement between all the elements. The resulting video enables reliability engineers to identify complex vibration modes, adverse differential movements, or areas of inadequate stiffness. Additionally, data from any point on the image can be extracted in the form of a calibrated time series or frequency spectrum, which can be used as part of a root cause analysis.
One of the main advantages of MA is the speed of data processing. Videos showing exaggerated movements can be replayed within seconds while the engineer is still on site. However, its two dimensional video is limited to the field of vision, not ideal for poorly accessible locations. It also allows room for user error.
Though a standard MA survey provides a comprehensive overview of the symptoms, it does not necessarily lead to a solution. But by employing it alongside other advanced tools and techniques, it is possible not only to diagnose a vibration problem, but also to identify and recommend what cost-effective remedial work can be carried out to solve it.
AVT Reliability often uses operating deflection shape (ODS) analysis and finite element analysis (FEA) together with a motion amplification survey to visualise the theoretical and operational mode shapes of the system and develop a solution that meets the customer’s needs.
Operating deflection shape analysis
ODS takes structural resonance evaluation to the next level. It involves taking vibration measurements from multiple points on a machine or structure, using a single-axis reference and triaxial roving accelerometer along with a four-channel data acquisition system, to measure vibration at key points of interest. Software is used to create a 3D animation which illustrates precisely how the structure is behaving in real time, clearly showing individual vibration mode shapes and frequencies.
ODS is not necessarily a replacement for MA, simply an additional, more complex, option. ODS survey results will typically take several days off site to process. Both techniques provide baseline information to identify the root cause of vibration-related problems. Then an advanced technique such as FEA can accurately predict the outcome of any corrective actions, without the need for upfront investment.
Finite element analysis
FEA, based on predictive software, allows a series of options to be tested on a 3D CAD model to evaluate the efficacy of different courses of action. An MA or ODS survey, or precise vibration measurements taken manually, can provide the baseline data on which the model is built.
“What if” scenarios are then applied to predict how the structure will respond. This can involve:
• Structural or static analysis – this predicts how the structure will respond under different load cases. It allows a range of different materials, thicknesses and orientations to be tested. Typically, this is used to evaluate solutions to areas of weakness identified by MA, for example to strengthen the machine baseplate.
• Modal analysis – This tests the dynamic response of the structure, revealing how vibration is amplified in relation to the varying speed of a motor, for example. Typically this is used to try to de-tune a resonance by shifting the natural frequencies away from any excitation frequencies.
Testing multiple approaches to a resonance problem establishes an optimum solution without investment in materials or time. It provides a clear illustration, through a series of 3D models, of what is causing the problem and the most efficient way to resolve it.