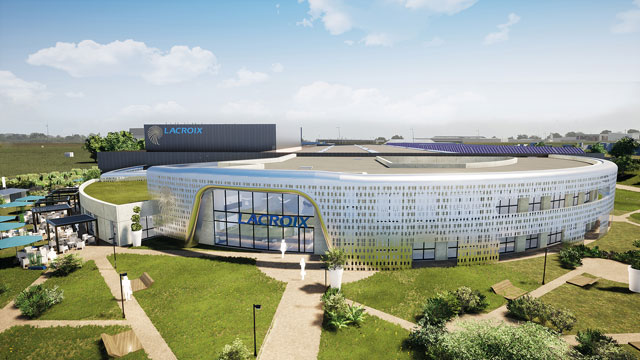
The potentially transformative impact of 5G on industry are being explored in tests being undertaken by Orange Business Services and Lacroix Electronics. Emmanuel Routier, Orange Business Services vice-president for Industry 4.0, explains
At Lacroix Electronics’ Montrevault-sur-Evre plant in France, trials of 5G technology are offering a glimpse into the future of Industry 4.0. By running full-scale tests of the technology on an indoor network designed and installed by Orange Business Services, the two companies are aiming to discover the best applications that 5G offers to industry. The network includes some virtualised network functions, making possible local data treatment and low latency.
The 5G network, based on experimental frequencies assigned to Orange, covers the entire production area. The trials are designed to see how 5G can improve efficiency and quality control, maintain optimal manufacturing environments and reduce overconsumption of energy.
Efficiency and adaptability
For electronic manufacturing, it is important to have highly flexible assembly lines where it is easy to change set-ups from one line to the next without the complexity of a cabling system. It is also important to monitor suppliers, vendors and market forecasts in real time.
5G permits the ultimate efficiency by keeping engineers and managers informed enough to adapt rapidly to changing quantity demands and urgent maintenance needs without the need to stop or reset production.
Historically, machine maintenance and product quality control have been a highly manual task, requiring huge amounts of time and manpower. 5G promises to change this. In the Lacroix trials, high-resolution photographs of electronic processes and machinery are taken. Advanced artificial intelligence algorithms can then be used to detect any errors in batches, or to discover whether a component needs to be replaced.
The ultra-low latency of 5G means that all this can be done in real time. Errors or dips in quality will be detected faster than any human or current technology is able to do. This allows the necessary interventions to happen with efficiency never experienced before.
Error detection can be reduced to milliseconds, allowing quick decision-making without having to halt production or stop the line because a component is missing or something needs replacing.
For machine maintenance, 5G promises to transform this traditionally manual task into something altogether different. Strategically placed sensors can transmit vibration, temperature and use statistics from machinery in real time to maintenance staff. Using this additional data, time taken on manual inspections will be reduced dramatically, and identification and remediation of mechanical faults can happen seamlessly.
Again, it is the speeds at which 5G can transmit huge amounts of data that will have such a transformative impact on industrial processes.
Maintaining optimal production environments
In many factories around the world, environmental factors are hugely important in manufacturing processes. The slightest change in temperature, humidity or light can be damaging to different materials and components.
Electronic modules produced for the aviation sector at Lacroix’s plant require strict temperature and hydrometric regulation to prevent damage. One of the tests being undertaken is using 5G to help in the technical management of production conditions.
Sensors and other connected equipment are used to monitor real-time measurements of crucial environmental data to prevent conditions becoming suboptimal.
In addition to helping the overall quality of production, the technology can also be optimised to prevent the over-consumption of energy over the entire plant.
The implementation of 5G means that up to one million sensors per square kilometre can be supported. Eventually, the technology will also enable to calculate the carbon footprint and energy consumption required to produce each product.
Paving the way to Industry 4.0
A crucial lesson of the current Covid-19 pandemic is that industry needs to accelerate digitisation and embrace disruptive technology as never before. Businesses around the world are relying on the connectivity provided by operators to maintain business continuity at a time of crisis.
Industry needs remote access that goes far beyond video calls with colleagues. It needs to be able to keep factories and plants running efficiently without a physical presence on site.
The trials at the Lacroix plant are illustrating that 5G will be the technology to facilitate this, and that the factory of the future may only be around the corner.
www.orange-business.com/en
mediarelations.orangebusinessservices@orange.com