The latest M&E Editorial Advisory Board roundtable discussed the suggestion that the Covid-19 pandemic had brought about a tipping point in digital technologies, and their potential role in economic recovery. By David Fowler
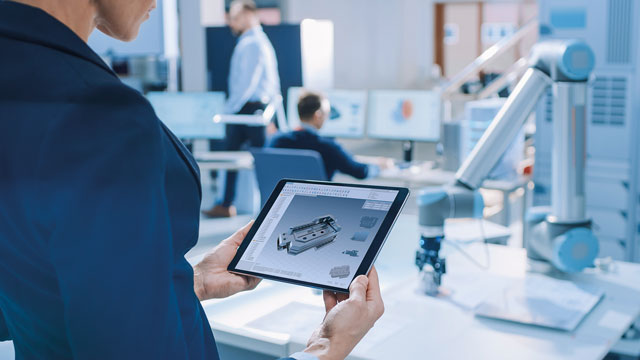
A survey at the end of last year by Make UK found that UK manufacturing companies moved quickly towards digitalisation when the Covid-19 pandemic struck.
According to the report Digital Skills for a Digital Manufacturing Future, 91% of companies said they benefitted from adopting new digital technologies during the crisis.
Over nine in ten companies said they had had staff working successfully from home, but many adopted predictive maintenance and remote monitoring of production. Nearly nine out of ten believed investing in training in digital skills had given them a competitive advantage.
At around the same time a report from McKinsey found that the pandemic had rapidly expanded take-up of digital technology across all sectors. “The survey data suggest that the COVID-19 crisis is a [technology] tipping point of historic proportions,” it said.
For the latest M&E roundtable the Editorial Advisory Board discussed their take on this trend, as well as what the barriers to adoption of the technology remained, and the role digitalisation could play in economic recovery following the pandemic.
Regarding adoption of the technology, Dennis McCarthy, director of DAK Consulting, said that in his experience, the products and services marketed by vendors could be characterised as “a solution looking for a problem” with the goal of replacing existing processes and assets.
In contrast, those who had gained from digitalisation did so by looking at how the technology could enhance existing processes and assets. He cited two successful examples. “One looked at every possible digitalisation element from additive manufacturing through to AGVs. Then they created centres of excellence, with different plants doing different things and sharing the results.” The second company looked for “pain points”, consulted its workforce and came up with about 100. It then looked at which ones digital technology could help.
“Both of them came to the same conclusion, that the gains came from pockets of automation, where you’ve said here’s an issue, how do we use digital?”
To put solutions into effect, both put together small cross-functional teams including Operating Technology specialists, a machine operator, an engineer, and a trainer.
His conclusion was that a cross-functional approach was key. “For me, where it’s been successful is in improving workflow across functions. For example, 3M improved supply chain effectiveness by linking in planning to production more effectively. Then when something caused a delay they could capture the issue automatically and deal with it. They could also test out new ideas on the fly to eliminate the root cause of the problem.”
Dr Peter Geake said his experience had concerned integrity management in major industrial hazard sites, necessary for companies to retain their operating licences. “They want to digitise that process so that it’s more economical to do and they have a high level of confidence of maintaining containment of hazardous materials effectively,” he said.
This proved more difficult than expected. Answers to questions about the decision-making process such as “what decisions do you take”, “how important are they”, “how often do you make them”, and “how does that fit into your reporting processes?” were somewhat vague. As a result it was only possible to identify “a kernel” of the process and try that out in a pilot.
“So my key comment was, don’t lock yourself into a technology you can’t adapt easily in the future – use agile-based technologies.” Because the underlying thinking needed to mature, there would be errors in the digitisation process. “You write specifications to do it, think it out, process-map it, but there will be holes in it because this is the first time it’s been done. So you’ve got to allow for that fact and choose a process that can be easily dynamic.”
Adopting the technology
How do companies decide which technologies to adopt, and how much logical thought goes into it? John Saysell, head of business development and training at MCP Consulting Group, said that in training, customers had asked for blended learning, combining training by webinar followed up by practical sessions on site. However, snags had emerged in practice. “The problem is then that people don’t do the online learning before they come to the practical stuff, because they’re busy people, so then you’ve got a big hole. You need the discipline to do two or three days’ swotting beforehand, picking up the knowledge, then we can help with the skills. If they don’t do the knowledge side then you struggle to build the skills on top of that. I can see great applications for web-based learning, but you do need to have people actively participating.”
McCarthy stressed the need “to look at the business process from end to end”, and to have realistic expectations. “In the companies where I’ve seen it work, they got a cross-functional team to look at key areas, came up with some conclusions, tried it out and went on from there.
They didn’t bring in a new bit of software, try and make it work and all of a sudden it was wonderful.”
The value of digital
How should companies decide what can be digitalised and what is its value? Geake suggested looking at business interruption costs. “You say if we don’t do this, what would be the business interruption costs, and analyse those costs. Then you know how much you can spend on the problem. If the problem doesn’t generate much in business interruption costs, forget it.”
Dr John Ahmet Erkoyuncu, director of the Through-Life Engineering Services Centre at Cranfield University, said there could be other reasons to adopt the technology, such as gaining a competitive advantage. “I think it’s a huge challenge to companies to think about why to digitalise, what should I digitalise and how do I justify it?”
Roy Davis, director of Manufacturing Productivity Improvements (MPI), said that to bring in any new technology “you have to be on a good bedrock. I’ve found over the years that sometimes there isn’t a bedrock there and you have to put that in place. Understanding how maintenance is managed throughout the business is fundamental. If you try to put digital technologies in place and you haven’t got that bedrock, all you’re going to have is automated chaos. So there’s always a lot of work in terms of a company strategy.”
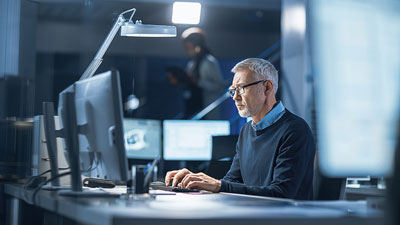
interest in digital systems.
Saysell said that MCP’s AMIS business improvement process identified five stages: chaos, reactive, control, innovative, world class. “If you’re down in the chaotic phase how are you going to be able to take on all these very high technologies?” he asked. Davis suggested that companies needed to be at least at the “innovative” stage to employ digital technology effectively.
Geake agreed. “With digitisation you’re in a world of optimisation and you’re really finding quite detailed benefits, so all the fundamentals have to be well established and practised and systemic in an organisation.”
Role in the recovery
Turning to the economic recovery post-Covid, Erkoyuncu posed the question: “Can we achieve economic recovery without digital technologies?”
Geake argued that the technology could speed up recovery: “It’s more a question of the rate you want to recover at, as opposed to not recovering,” he said. “If you want a true V-shaped recovery in your economy, you’ve got to really utilise all the technologies to drive that, otherwise you’ll get a very flat hockey stick.” But he believed the level of investment available remained an issue.
Davis was pessimistic on this point.
“Companies’ capital expenditure has been put on hold as a result of the pandemic and it will take a while for them to regain confidence to reinstate it,” he said. Strategic thinking had also been put to one side: “probably for the next six months at least, companies are going to be more interested in trying to get back on to an even keel, so it might have put everything back 12 months.”
With the UK in lockdown and the prospect of perhaps six months before more normal conditions were likely to return, how could companies capitalise on the digitalisation process and the benefits they could get from it?
Geake said: “In terms of trying to do something quickly and dirty but still using a digital approach, you can use semantic database search systems, like Watson from IBM, to dig through your data to find interesting patterns and things of that nature.” But he added: “It’s only Elastoplast: you’re finding something which will help, but isn’t the solution. It comes back to the point about knowledge and understanding. It’s a patch: it can be a very effective one and can generate some savings, but it’s a bit unknown how successful it will be.”
Erkoyuncu said that at Cranfield he had observed that “different sectors have taken very different approaches”. “Some sectors have turned their back on R&D – there’s just not enough money. But others are investing more in R&D than they normally would: they’re seeing it as an opportunity to close the gap with other sectors. It’s creating opportunities for competitive advantage.”
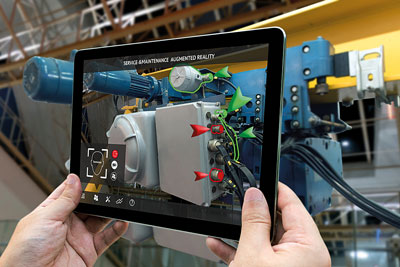
He added: “There’s also an interesting angle with skills. Many people are putting their staff through training and this is opening lots of opportunities. They’re preparing for the future and for having the skills and the appropriate culture to implement digitalisation. Some companies are really looking at how they can adopt these technologies and how they could use them today. That’s an interesting shift.”
Taking augmented reality as an example, he said: “Many companies think it’s futuristic. The reality is, it’s not futuristic any more. It can be picked up and used today. We just need to be realistic with the applications.” Conversely, though many people talk about digital twins, “people just assume it’s going to revolutionise the whole company – but it’s got to be done in stages. You’ve got to find the appropriate applications and demonstrate the benefits.”
He concluded: “I still think many companies haven’t got the relationship between the value and benefits they are going to get from the digital technology versus using technology for the sake of it. So there’s still a lot to be done, but many companies are really moving in the right direction.”
Would companies that had adopted digital technologies stick with them?
Saysell said: “I think if you can show sustained benefits then people will continue to use them.”
McCarthy added that the use of online systems in response to the pandemic had accelerated business leaders’ curiosity about how digital technology could be of benefit more generally.
“There’s far more awareness of what digital can provide and how it can improve collaboration and empowerment, and I think that it’s unlikely that the leading companies will walk away from that.”
Companies he worked with had reached a tipping point where “because digital systems are being used more, the business leaders are seeing the benefits, and the investment decisions are moving away from asking ‘will this save me money?’ to ‘will it help me to adapt or grow faster?’ “
He added: “Not every company’s going to buy that but I think there are enough out there that do want to see what the benefits would be. I think that the companies that are going to be the most successful, the ones that are most innovative, are the ones that are going to adopt it, and the ones that don’t adopt it are going to go to the wall.”