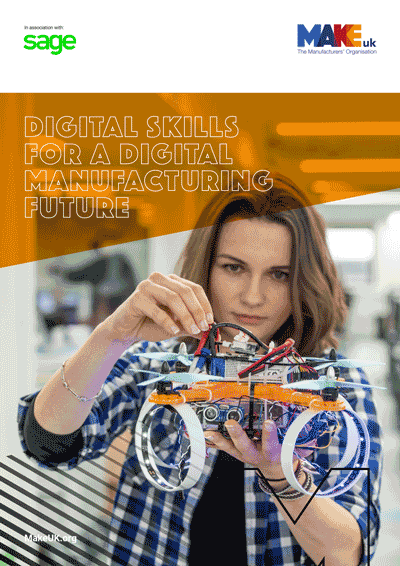
Investment in digital skills and technology has powered manufacturing through the coronavirus crisis, according to new research from Make UK and Sage.
British manufacturing companies moved quickly towards digitalisation when the pandemic struck, with nearly half switching to digital working practices within two weeks of lockdown, according to the report Digital Skills for a Digital Manufacturing Future.
Make UK called for the establishment of a National Skills Taskforce and digital lifelong learning accounts to help keep up the momentum.
According to the research, 94% of companies said that after just a fortnight’s digital installation and planning they had staff working successfully from home – in an industry associated with manual tasks and a high proportion of production-based work. And 91% of companies say they benefited from adopting new digital technologies during the crisis.
Technology adopted allowed remote working for office staff, plus predictive maintenance and remote monitoring of production. The quick adoption of remote production and monitoring systems kept vital lines working effectively, as well as allowing the switch in production to make vital PPE equipment and ventilators for the NHS. The use of digital technology was also found to accelerate innovation plans.
In addition many companies changed on-site working practices, for example splitting shifts into teams operating independently. This allowed operations to continue while reducing contact, and the opportunities for Covid-19 to spread, to the minimum.
The research also found that eight out of ten companies would continue to adopt new working practices, having seen the quick benefits. A quarter of companies polled found that using new digital technologies had boosted productivity, and 12% said it had increased production levels.
87% of manufacturers said investing in digital training gave them a competitive advantage, and nearly two-thirds (64%) had undertaken training to improve digital skills in the last 12 months.
The acceleration in digital take-up must continue, Make UK said, to promote continued growth as the sector rebuilds. Though 45% of companies said they had already changed their skills training and strategies in the light of Covid-19, cost pressures and the need to socially distance has meant that two-thirds of companies have put some or all of their training on hold. And two-thirds of manufacturers did not think the education and training system is keeping pace with advances in digital technology.
Make UK called for a National Skills Taskforce to be set up by government and industry to create a digital skills programme, and a digital skills account for lifelong learning to allow reskilling.
Make UK chief executive Stephen Phipson said: “The last six months have shown that digital was crucial in making it possible for manufacturers to continue production against a backdrop of Covid. It is crucially important that we do everything possible to keep hold of skilled people who are currently unemployed. This is why government must work with industry to set up a National Skills Taskforce to match those skilled workers with employers who desperately need those skills.”
See the full report here
- Make UK has published a plan for recovery Prepare, Implement, Lead, in which it calls for an industry group making weekly reports to the Cobra emergency response committee. In preparation for the end of lockdown and to stimulate demand it calls for the R&D tax credit to be doubled, the extension of temporary increases in investment allowances and immediate introduction of 5G technology across the UK.
https://www.makeuk.org/insights/reports/the-three-point-action-plan