Bob Wood, a technical engineer at Total Lubricants with 45 years’ experience in the industry, explains the different tests that can be used to analyse hydraulic and gear oils, turbine oils, metalworking fluids and greases in manufacturing and industrial settings
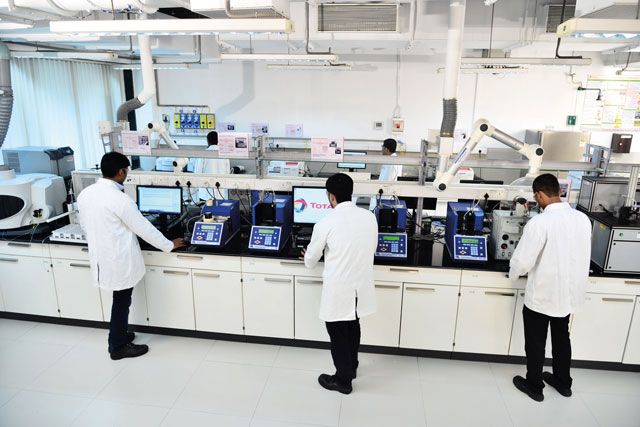
Lubricant analysis is the laboratory process for examining a lubricant’s properties. It is like a blood test, as it provides accurate information about the condition of the lubricant and the machinery and can identify potential “health issues”.
Lubricant analysis is carried out as part of a predictive maintenance strategy. By regularly analysing a sample of a lubricant obtained without stopping the machine, the state of the machinery can be fully understood, helping optimise maintenance schedules and avoid unexpected shutdowns and costly repairs.
Years ago, lubricant analysis was carried out manually by an analytical chemist and the process would take a considerable amount of time. However, as the technology has advanced, the analysis has become much faster and provides more accurate results.
In addition to advances in technology, the sample bottles have also changed. There was a time when you would examine marine samples that had been submitted in used whisky bottles that had not even been cleaned first. Everything is, of course, much more organised today.
In a manufacturing or industrial setting there are several lubricants that a maintenance manager might wish to analyse in order to make sure they are working effectively, and that the machinery is operating in peak condition. These include hydraulic and gear oils, cutting fluids, and greases, with each type having its own test suite.
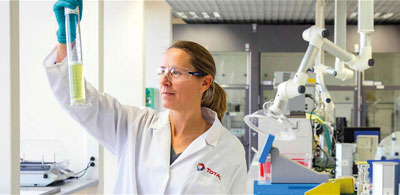
Hydraulic and gear oils
Hydraulic and gears have myriad applications in manufacturing and industry. The viscosity of hydraulic and gear oil is very important. If the oil is too thin it will cause wear, and if it is too thick it will generate heat.
Analysis for hydraulic and gear oils includes:
- Kinematic viscosity – the oil’s resistance to flow under gravity at 40°C
- The Total Acid Number (TAN) – a measurement of the acidity and oxidisation of the lubricant. Oil with a high TAN can lead to corrosion of machinery and clogged oil filters
- Wear metals – to see how the machinery and its components are wearing
- Cleanliness – how clean the oil going through the system is: it has to be clean, so the filters do not get blocked
- Anti-foaming properties and other additives – to identify whether the anti-foaming properties are still working and if any additives have deteriorated and need replenishing
- Contaminants – to make sure the oil does not contain increased levels of various contaminants. One of the major contaminants is dust. These fine particles, known as silica, can enter the hydraulic system and act like diamonds on glass, scratching and causing wear, which can stop equipment working effectively or cause it to fail.
Gears vary in size, but the biggest ones are the open gears used in the cement industry. These massive gears rotate the mills; their speed can be increased or decreased, and their torque can be increased so they can lift heavy loads, so it is important to look at viscosity, wear metals and additives remaining. Normally in a gear oil you are looking for the presence of phosphorus, which is one of the extreme pressure (EP) additives. This can be measured to identify how much of the additive remains and to give an indication as to when the oil will need changing..
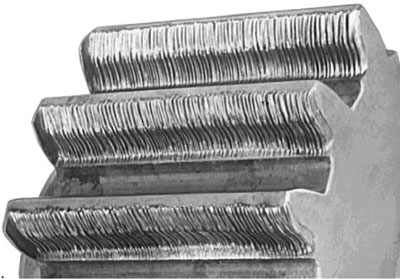
Oil analysis steps
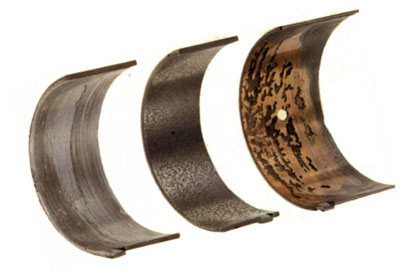
The oil is extracted at a sampling point on the hydraulic or gear system. A hand pump may be used to extract some oil into a small container, which is then labelled and sent to the laboratory for analysis. The label will state what the product is, where it has come from, how old it is and what the grade the oil is.
The laboratory will register the sample and put it through whichever test suite it requires. Most oils will need a viscosity check, then a look at the wear metals and an acid value test.
The test data goes to a diagnostician, who has in-depth knowledge of how systems wear. They will interpret the results to see whether the wear, for example, is within the expected limits. All levels are scored on a traffic light system, with green indicating a satisfactory diagnosis, amber showing slight deviations and red highlighting that an anomaly has been found.
The results are used to form a trend analysis looking at the oil’s health over time.
Turbine oils
The turbine oils used in power stations have a special test suite which is similar to that used for hydraulic oils. In addition to tests to look at viscosity, wear metals, TAN and cleanliness, the rotating pressure vessel oxidation test (RPVOT) is carried out. This measures the oxidation stability of an oil and how much antioxidant remains, which gives an indication of how much life is left in the oil.
Another test for turbine oils is the RULER (remaining useful life evaluation routine), which is also used to determine the amount of antioxidant additive that is available in the oil. The patch filter test (MCP – membrane patch colorimetry) is used to measure the amount of varnish in the oil as a result of oxidation that can occur when the oil gets very hot. If the hydraulic control valve, which controls the speed of the turbine, gets coated with varnish, it will not open and close properly and this can cause major problems in an industry like power generation.
Soluble cutting oils
Soluble cutting oils are used in metalworking, in machining metals in CNC machines and lathes. The concentration of the oil in the water emulsion must be regularly checked to see that it has the right cooling and anti-corrosive additives. If the cutting oil is not at the correct concentration, it will not work as effectively as it should, and tools will have to be sharpened and replaced more frequently.
From a health and safety perspective, it is also important to check the cutting fluid for biocides and bacteria. When cutting fluids are left unused, even just over the weekend, they can produce a nasty odour like rotten eggs due to anaerobic bacterial action in the stagnant fluid.
Operators also need to make sure the pH level in cutting fluid is within an acceptable range. If it is too low it can cause corrosion on the workpiece and if it is too high it can cause skin and eye problems for the operator.
It is essential to maintain the quality of the coolant to make sure it is clean, so that it lasts longer and so that the machined pieces are produced in consistently good condition.
Water hardness should also be tested. The hardness or softness of the water could affect foaming or the stability of the emulsion. If there is too much foam, for example, it can escape from the sump or tank onto the shop floor causing safety issues.
Some of these tests, for example concentration and pH, can be done on site. Operators who value their machines will do this regularly as part of looking after their costly equipment.
Grease
Grease analysis is usually done reactively when something goes wrong, to help operators understand the root cause of the failure. Looking at the grease will indicate whether there are wear metals in it and this can then be measured. Normally the amount of sample sent for analysis is very small. The grease’s appearance will show if it has been overheated, by its colour and texture – that is if it is hard.
Oxidation can also be tested to make sure the grease has not oxidised. When grease oxidises, there is a build-up of acidity, which can lead to carbonisation, where the grease hardens, reducing its effectiveness. The Ruler test can tell if all the antioxidants have been used up and the Total Acid Number can show if the grease has been overheated.
For in-depth investigation, a scanning electron microscope can be used to identify exactly what metals are in the grease, or the wear metals can be determined using inductively coupled plasma (ICP).
Other techniques along with lubricant analysis before a failure can also help to build up a picture of the reason for the failure. These include vibration analysis and thermal imaging, though this is not always possible. Vibration analysis “listens” to the bearing to make sure it is running properly and to detect wear or misalignment.
Benefits of lubricant analysis
- Reduces maintenance costs
- Helps maintenance operation planning
- Improves equipment reliability and performance
- Minimises downtime
- Lengthens machine lifetime
- Extends oil drain intervals.
Conclusion
The saying “prevention is better than cure” is very true. The cost of the analysis is so small compared with the possible failure and downtime that can occur, so it is wise to look at condition monitoring and to use a laboratory that has the necessary test suites to make sure that your lubricants are in good condition. If the results come back saying action is needed, take note of this and take the remedial action recommended.
Total’s industrial analysis service ANAC INDUS is designed to make manufacturing and industrial operations more efficient and cost-effective.
For further information, visit
www.total.co.uk/anac-industral-oil-analysis