Geraint Jones, technical manager at SKF, outlines the options available to operators of machine tools for condition monitoring systems.
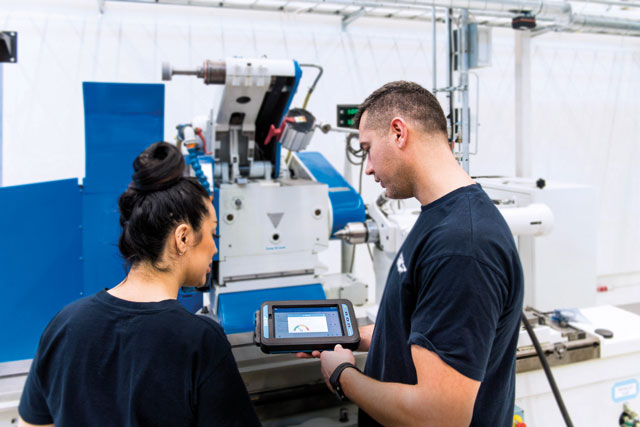
Machine shop owners and managers face many challenges, and looming large among these is the need to be sure of the accuracy and reliability of their machine tools. Such tools will not produce parts to the tolerances required of them if key components, such as their spindles, are not maintained properly. Any wear in the spindle units, or irregularities in their operation, must be identified early and rectified before they begin to cause problems, using predictive maintenance.
A successful predictive maintenance regime cannot be implemented without an effective condition monitoring system, through which the condition of a piece of machinery can be determined while it is in operation.
There are two distinct types of condition monitoring system that a machine-tool operator can opt for. They can take a manual route (offline or periodic monitoring), equipping maintenance teams with handheld devices they can use to measure and record parameters during routine walkaround inspections. Or they can automate, installing permanent sensors that transmit data across a network on their machines (online monitoring).
Picking the right approach for a machine requires the costs of collecting, communicating, storing and analysing the data to be balanced against the reliability benefits that the data brings, and the needs of the given application. For relatively simple applications such as the milling of large panels, where the spindles run for long periods of time at consistent speeds, an offline condition monitoring approach may suffice. For more complicated machining processes, where the speed and position of the spindle changes rapidly and often, an online approach may be more suitable. The two approaches can be used in tandem: online to monitor parameters that change rapidly, and offline for those that change slowly, such as thermography and oil condition, for instance.
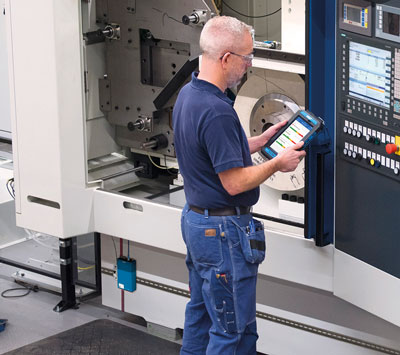
Regardless of the method employed, it is vital the right data is collected if the potential of a condition monitoring system is to be exploited fully. For monitoring spindles, the critical speed is a key parameter. The critical speed of a spindle is the theoretical angular velocity that excites its natural resonant frequency, causing it to distort and rapidly increasing the amount of vibration it generates. In most machining processes, it is important that any time the spindle spends operating at the critical speed is minimised.
To achieve this, an operator first needs to know what the critical speed of the spindle is. This can be discovered by monitoring two parameters. An accelerometer can be employed to provide data on the spindle’s amplitude of vibration. The phase change – a change in the direction of vibrations – that occurs when a spindle hits its critical speed can be monitored by combining the vibration data with a speed sensor. By combining data gathered on the speed and amplitude of the spindle on a Bode plot, the critical speed can be determined precisely.
The data gathered through condition monitoring programmes must be analysed properly. Though it can be interrogated on site, it is often more effective to send the information to a remote monitoring centre. There it can be examined more or less as it is being collected, meaning any potential inefficiencies in the operation of a machine tool can be identified more quickly. Further, it is easier for this data to be forwarded to other teams – application specialists or lubrication engineers, for instance – for analysis in much greater depth.
Advances in condition monitoring technology now mean that maintenance and operations teams can spend less time collecting data, and more time acting on it – bringing about real improvements in the performance and reliability of a machine.
01582 490049 | www.skf.co.uk