Pete Mills, commercial technical operations manager at Bosch Commercial & Industrial, outlines the options to consider to optimise efficiency for both production and space heat.
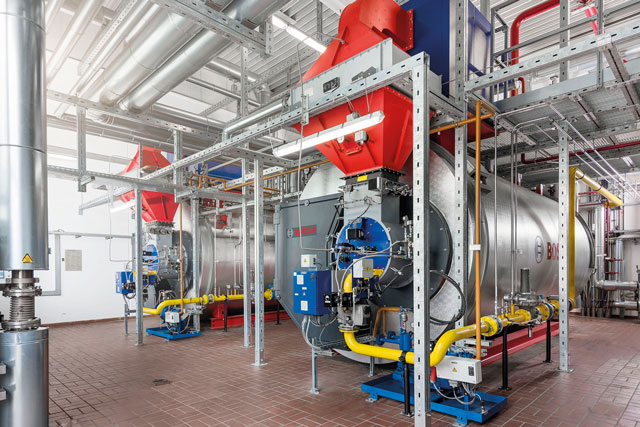
In these tough economic times, achieving good plant efficiency is more important than ever. When considering plant replacement, there are numerous ways in which plant designers can seek to optimise the output of steam and heat generation systems. A thorough consideration of the different options will help achieve efficiency goals and futureproofing.
Separating production steam from building heat requirements can bring about a significant reduction in running costs. The higher temperatures and pressures needed for production mean higher system costs and running costs. Sizing a heat generator that needs the safety equipment and operation protocols for production steam to cover less demanding heating loads as well should be avoided. There will be significant cost savings for heat demands that can operate under 110°C, where there are no requirements for supervision or monitoring. This is especially true when heat demand periods are outside production hours.
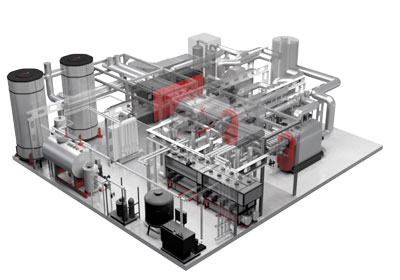
Where there is significant spread between the highest and lowest heat requirements, dividing the heat generation capacity into several units makes a lot of sense. The division should be based around the lowest load requirement, so that a single boiler can operate efficiently at this point. This will reduce cycling, as well as the wear on boilers and firing plant caused by constantly starting and stopping. Dividing the capacity into identical outputs gives the greatest flexibility and security. It reduces the need to hold several different sets of spare parts and allows the ability to swap parts in times of dire need.
The hydraulic arrangement is also significantly simplified through the use of identical multiple boilers. Hot water boilers with similar resistances and flow rates make sizing the primary system straightforward and allow for standard arrangements to be used.
Once the overall arrangement of heat generators is established, it is time to consider how the individual units may be optimised. The starting point is to consider the boiler/burner combination that will have the greatest benefit. Optimisation tools look at the benefits of slightly oversized boilers that can benefit from smaller burners while maintaining output. This has the benefit of reducing burner electrical energy as well as increasing the control range. There are other benefits too, such as reduced emission levels.
Consider at this stage how start-up programmes could be optimised to reduce the peak capacity required from the plant. Together with careful assessment of the real requirements, this can have a significant impact on the plant sizing. All too often, plant is sized with much higher capacity than will ever be needed in practice, meaning efficiency suffers as oversized boilers struggle to match the lower load demands.
Further efficiency savings can be derived from the use of flue gas economisers, which recover heat that would have been otherwise wasted. These can be constructed to operate dry or wet, depending on the overall system operating parameters. Often the additional energy will be used to pre-heat feed water, and efficiency of more than 95% can be achieved.
Any heat generating plant needs good control if it is to achieve the efficiency desired. For multiple smaller units, this is particularly important. Sequencing of individual boilers will ensure the right amount of capacity is brought in to cope with the demand. Rotation of the boilers will maintain equal run hours across the plant as a whole, meaning wear is equal and planned maintenance scheduled more effectively.
Finally, it is worth considering how the production of heat will be decarbonised in the future. Many industrial processes will always require high temperature heat to be effective. There is currently a great deal of research being undertaken into the use of hydrogen in a decarbonised gas network and this includes industrial boilers.
For large boiler plant with separate burners and gas train, there is the possibility for future conversion to 100% hydrogen. However, typically this requires a slightly oversized boiler shell, typically 10%, to meet emissions targets. As a result many managers are considering specifying the extra size at the outset, to give greater flexibility in years to come.
www.bosch-thermotechnology.com/gb/en/commercial-industrial/home/